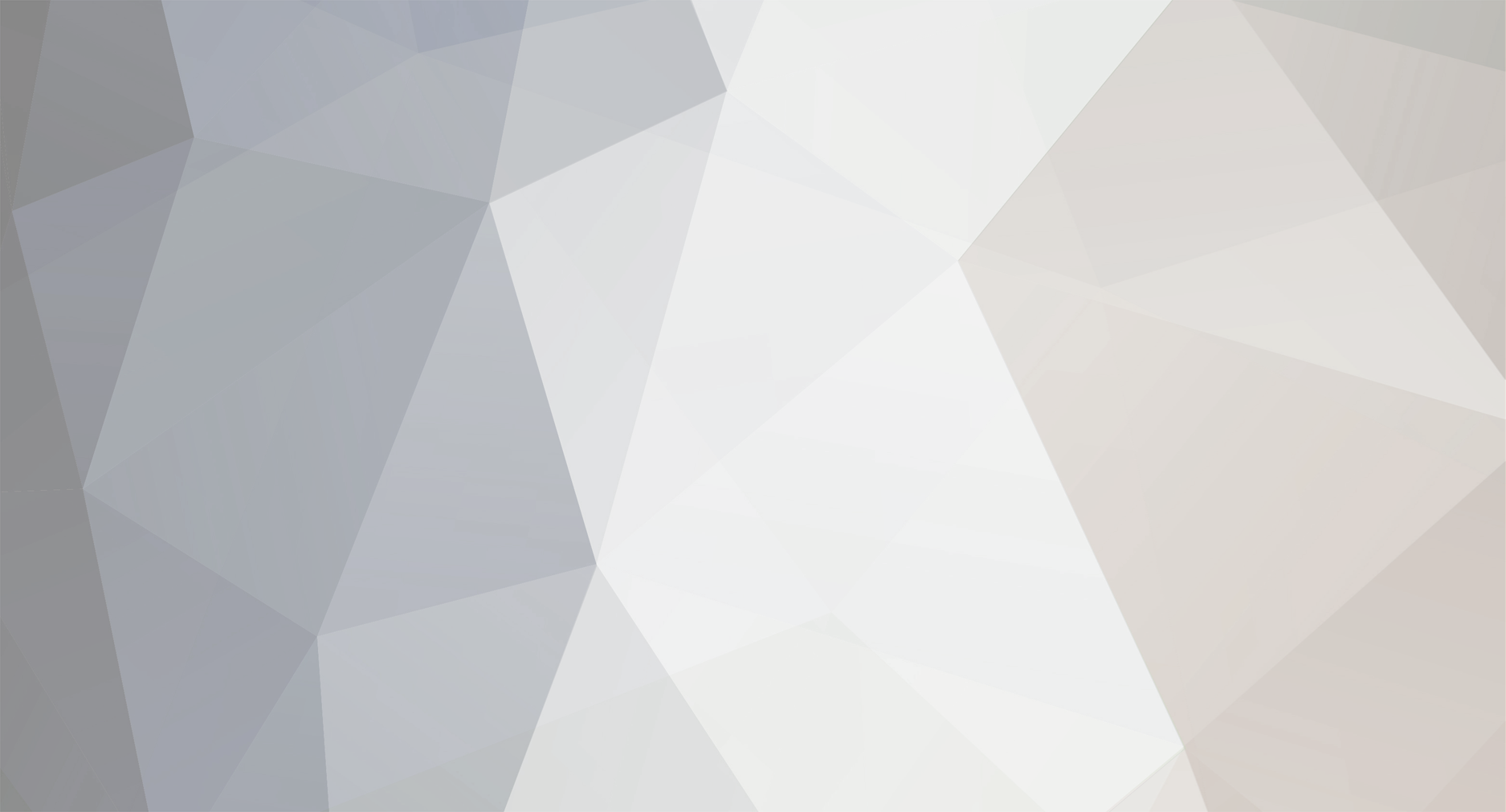
aro
Members-
Posts
1,018 -
Joined
-
Last visited
-
Days Won
11
Information
-
Aircraft
C172
-
Location
Melbourne
-
Country
Australia
Recent Profile Visitors
The recent visitors block is disabled and is not being shown to other users.
aro's Achievements

Well-known member (3/3)
-
You have some quasi-military ideas going on here. The instructor is usually more experienced, but senior is the wrong word. "The student must follow the Instructors direction?" No. When they are in the aircraft, the instructor as PIC has the authority that they have over any other passenger, to ensure the safety of the aircraft. Other than that there is no "must" about following directions. "Can not legally fly without the Instructors approval" The instructor needs to authorize the flight. That is different to command, e.g. the instructor cannot command the student to take off. Line authority? No such thing in a civilian flying school. More complex in the military, where a student might be higher rank than the instructor so the student does have line authority, and line authority and PIC must obviously be 2 different things. You are pulling in every possible meaning of command, rather than what it means in this specific context.
-
It is relevant - the instructor cannot be PIC if they are not in the aircraft! It is in the definition of PIC, quoted previously in this thread from both CASA and RAAus (and FAA) - you just don't like it. "Command" refers to command of the aircraft, not people. I did my first solo in an aircraft without a radio not that long ago (1990s). When the rules were developed, that would have been common. They're not going to change the definition of PIC just because sometimes the student is within sight of the instructor and radio is available. There are many more situations where the instructor isn't in a position to be any use. Solo circuits, where they are not going to stand out in the weather for an hour to watch you. Area solo and solo cross countries where you are well away from where the instructor could be able to "command" anything.
-
There's no grey area. You just think the law should be different. The instructor is not in the aircraft. The person flying the aircraft has final responsibility for its safety. Let's take a scenario: A student takes off on their first solo. While they're on downwind, another aircraft lands gear up and blocks the runway. The instructor looks at where the aircraft stopped, and tells the student over the radio they can land over the top of the disabled aircraft in the remaining runway. The student points out they have 3 hours fuel and plenty of daylight and would rather circle the airfield and see if the runway can be cleared. Who is responsible for the decision of what to do? Answer: the pilot in the aircraft. No question. They are pilot in command and responsible for the safety of the aircraft. They can take the instructors advice, but they make the final decision.
-
Yes. If the student signs that document (probably incorporated into signing out the aircraft) they are bound by the terms and conditions. There isn't really an argument that they shouldn't be because they are a student. Whether the terms and conditions are fair is a different argument. There are many contracts that we would argue are not fair.
-
CASA make the rules. CASA say they are in command and have authority and responsibility to make decisions for the safety of the aircraft. CASA are clear. You are muddying the waters because you think the rules should be different.
-
You understand the idea that you have a contract with the insurance company saying that they will pay (according to various terms and conditions). Why do you think you can't have a contract with the student? It doesn't matter whether they are trained or not - it is the contract that matters.
-
Why does the insurance company pay when they were not even present? Because you have a contract saying they will pay. What you say might be correct, if there is no contract and you try to sue them for negligence. But there is almost certainly a contract (terms and conditions, and a signature accepting them) which spells it out. Then all that matters is who the contract says will pay.
-
If they are solo, yes they can override the direction of the instructor if necessary for the safety of the aircraft, and there is an expectation that they will do that if required. They are in command of the aircraft. The instructor sets the circumstances where that happens, and gradually widens it as they gain experience. The reason you have minimum solo time is to give the student experience in command.
-
You keep quoting imaginary laws. djpacro quoted the actual, real regulation that says that a student is pilot in command when flying solo. Like it or not, they are in command of the aircraft. Or the definition from RAAus: Pilot in Command (PIC) For RAAus student and pilot purposes: the person in control of the aircraft when not in the company of an Instructor and referred to as solo flight time The instructor has made the judgement that they are ready for command when they send the pilot solo. The circumstances might be limited (whether first solo through to solo cross countries) but it is still command time. But PIC isn't necessarily relevant for insurance purposes anyway. For insurance, what matters is the terms and conditions you signed up to. Which is why it's a good idea to check them before you hire/fly.
-
aro started following Voltage Regulator Failed and Insurance excess
-
The first step is what does the contract you have signed/accepted say? In theory, the student could be liable for everything regardless of who is PIC. An example where that might be likely is if the student owns the aircraft. You might have rights you can't sign away (consult a lawyer on that one), but to enforce them might require suing the instructor. As far as who is initially responsible for paying for damage, you can very easily create a contract that specifies that.
-
Isn't the antenna cable coax with the shield attached to the BNC connector at each end? So the shield ends up attached to the antenna and ground plane at the antenna end, and the radio at the radio end?
-
Rotax do allow Lithium batteries and even sell them under the Rotax brand - so in theory it should be OK. But Rotax specify max 22 amps from the regulator, and the batteries list charging current as 5-15A recommended 60A max so I'm not sure how that works together. Is there something that reduces charging current to keep the maximum load under 22 amps?
-
If the failures are being discussed on the Rotax forum, that's probably where you will find opinions on the alternatives. If there are few people here who have failures, no-one is likely to be able to make a comparison. One thing I have heard is that high load isn't good for the Rotax regulators. One of the characteristics of the EarthX batteries is a high initial charging current, which seems like it might overload the regulator.
-
Couldn't you drop the 95.10 registration and register it under 95.55 e.g. change to 19-1103? What was the obstacle?
-
Join the SAAA and learn?