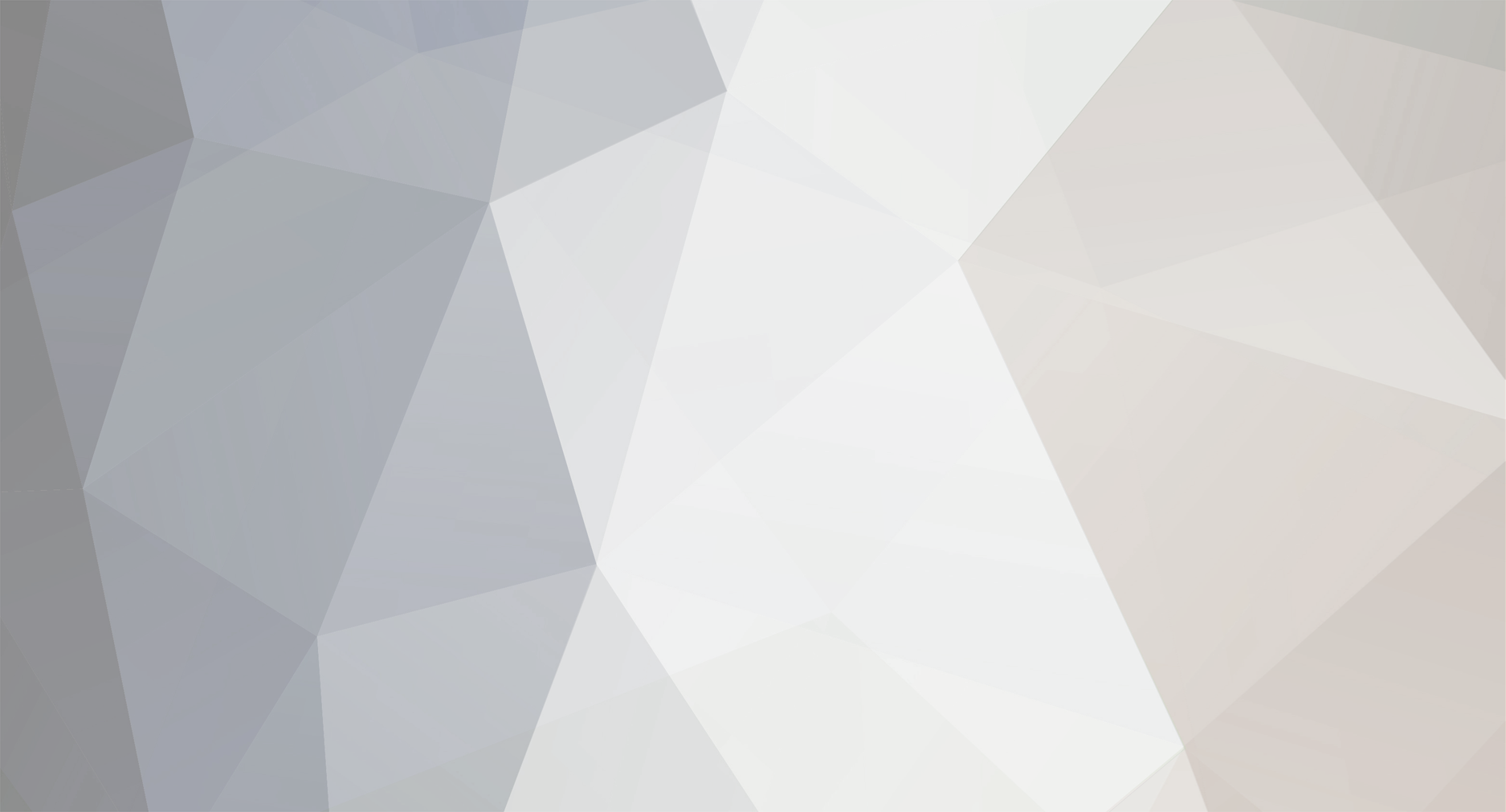
skippydiesel
Members-
Posts
6,403 -
Joined
-
Last visited
-
Days Won
67
Content Type
Profiles
Forums
Gallery
Downloads
Blogs
Events
Store
Aircraft
Resources
Tutorials
Articles
Classifieds
Movies
Books
Community Map
Quizzes
Videos Directory
Everything posted by skippydiesel
-
The concrete floor is likly to be the single big cost - compacted earth very little. Your $60K is a luxury job, no doubt with power, water, sewage mezzanine living quarters and 2 aircraft with big wing span. I can comfortably fit my Sonex in a space 8 x 8m with plenty of storage room - Kit farm shed, about $8k (delivered) less on special/sale, self erect. 😈
-
Small plane missing Victoria 18/09/22
skippydiesel replied to BrendAn's topic in Aircraft Incidents and Accidents
Naaa! your okay - you just needed to contextualise your cloud base no fly comment😈 -
Small plane missing Victoria 18/09/22
skippydiesel replied to BrendAn's topic in Aircraft Incidents and Accidents
Simple - the thrust of this Thread seems to be about allocating blame - there are the pilots blamers and the system blamers. I am not so intersted in the facts of the case , more the commentary from Forum members. I am simply pointing out that the pilot had a history of indulging in activities that are inherently more risky than knitting. It is also likly there were some system failures, (instructor/RAA) which may be lessons that serve to modify the system (a good). Coroners often reflect societal /political expectations - not suggesting corruption, just bias. I think it likly that the pilot, once free of close supervision, would likly have done what he did sooner or later - he was a male!😈 -
Small plane missing Victoria 18/09/22
skippydiesel replied to BrendAn's topic in Aircraft Incidents and Accidents
Where does this 3000ft cloud base come from? What of training from airfields at almost sea level?😈 -
Small plane missing Victoria 18/09/22
skippydiesel replied to BrendAn's topic in Aircraft Incidents and Accidents
Some observations on human nature - in particular the male of our species (all?). I know very little of the incident that forms the basis for this debate however I ask you to consider; We are an inherently risk taking species. Our stories, glorify the macho man. Our courtship behaviour is often typified by displays of dairing. (look at me!) Pilots of all levels are mostly male - do you need to ask why? Motorcycle riders (of all ages) are mostly men - see above comment. While intensive training (CPL?) will often modify, at least temporarily, risk taking behaviour/personalities, it is unlikly to be a permanent fix. If you want to see videos of aviation risk taking & rule breaking - there are probably hundreds out there. This is classic (male) "look at me syndrome". Males are far more likly to die prematurely than females, in large part due to the testosterone in our veins and the tacit expectations of society. All modern societies spend a ridiculous amount of effort on trying to prevent male risk taking, instead of accommodating , redirecting and accepting the inevitable mortalities that ensue. Our supposedly primitive forebear were much better at managing our instincts. I support any investigation that seeks to determine why an incident occured. Not so that an individual will necessarily be exonerated (or crucified) but that his (usually) actions can be seen in a holistic context. From the little I have read (in this Thread) the dead man was on a mission to risk his life in many ways, before his poor judgement finally caught up with him. The part that instructors/organisation's (RAA?) played is likly a minor one - this does not mean that systemic & personal errors were not made, from which lessons may be taken.😈 -
Small plane missing Victoria 18/09/22
skippydiesel replied to BrendAn's topic in Aircraft Incidents and Accidents
"a vfr pilot taking off with a 2000 ft cloud base." Not an issue , IF (?) he is able to maintain 500 ft clear of surface. -
Unsung Alpine Aviator Hero, Hermann Geiger (MSFS)
skippydiesel replied to FrankPilot's topic in Aviation Videos
Wow!😈- 1 reply
-
- 1
-
-
Stuck VFR on top • a 'Backcountry182' video
skippydiesel replied to Garfly's topic in AUS/NZ General Discussion
I agree it's a far from ideal situaton HOWEVER the biggest worry is the mindset of the VFR pilot. There is much that a VFR pilot can do to ensure a safe arrival - the Russian Roulette statement is pure alarmism, sorry if I offend. -
The Bing diaphragm carburettor, is nothing like the carburettors used by Ly/Con - hense my inquiry. BING: The movement of the diaphragm is controlled by manifold pressure (MAP) The diaphragm (working on the needle valve) controls fuel flow MAP is controlled by the throttle/butterfly valve connection (no mechanical connection to the diaphragm) AND the propeller, acting as a governor. My question is about the ability or not of the propeller to determined/control fuel flow in a BING type carburettor. By using wide open throttle (WOT) rather than another setting, I am attempting to remove the variable introduced by the butterfly valve.😈
-
Fatal Victoria, training and RAAus.
skippydiesel replied to Litespeed's topic in Aircraft Incidents and Accidents
Ditto - I was supporting your initial statement however went on to expand on the third party blame game😈 -
Fatal Victoria, training and RAAus.
skippydiesel replied to Litespeed's topic in Aircraft Incidents and Accidents
Disclaimer - My following comments are NOT about the incident being discussed in this Thread. "That said the attitude of the pilot is always a factor and as I understand it he was advised not to fly in such poor conditions but ignored the advice" We live in a time in which personal responsibility seems to have been sidelined in favour of blaming/suing thirds parties. I feel that there are two reasons for this: The various causation concepts (eg Swiss Cheese) which have rightly moved the focus on the individual (pilot)as the sole perpetrator/cause of the incident, to one that looks at the system that may have failed. The legal industry (ambulance chasers) who seek to make significant income out of bringing the matter to a court of law - popularised by TV programs & muckraker journalists. While I am in favour of concepts like the Swiss Cheese view of incidents, the PIC is and always will be, the one who is responsible for the decision to fly or not. Swiss Cheese should have the effect of proportional responsibility, not absolution (unless deserved). "in raaus you can fly lightweight slippery fast aircraft the will get you into trouble quicker than a lumbering old cessna so maybe our training needs to reflect the performance of these modern airframes. they are not draggy ultralight aircraft any more." This is a fallacy - RAA's covers a very wide range of aircraft types & performance. RAA'S instructors/schools can only deliver generic instruction. When changing to a diffrent type of aircraft it is the pilots responsibility to seek further instruction ON TYPE😈 -
Not asking for advice on how to operate prop/engine at altitude - asking for opinions on the effect/influence of prop, as governor, on fuel flow in a Rotax/Bing carburettor😈
-
Engine maintenance training by Jabiru and Rotax
skippydiesel replied to Blueadventures's topic in Engines and Props
Southeastern - Mexico?😈 -
Brains Trust stumped?😈
-
Scroll down to Aircraft General Discussion open Scroll down to Start Spare Parts List There is a lot of tangential debate , consider it educational. My recommendations are all for Gates hoses, most (fuel/coolant) of which can be obtained through REPCO, with the exception of the oil hose which comes from Hydrolink "For fuel line I use Gates Barricade EFI (also known as MPI) this is overkill for pressure rating but has slightly better temperature & permeability. This is compared with the Barricade Carburation Hose, which also meet the Rotax specifications. Comes in a range of ID's - there will be one to suit your application. Be sure to get the right size, cut carefully (I prefer to cut, so installed length is covering the whole length of the spigot at each end. Use a hose cutter for nice 90 degree clean cuts and blow through with compressed air before installation)." "Seems that there is nothing available (except from Rotax) in straight hose BUT you can purchase the following molded/shaped hose in 16.5 & 17 mm ID which can then be cut to the required lengths. Note: Most installations will require a little over 2m in total, you will have to purchase more than one of the preformed hoses, so be sure to compare the total price with Rotax supply. 02-1579 16.5mm 02- 1249 16.5mm 02-0912 16.5mm x 755 mm long 02-1415 17.00mm x 280mm long (see below) Gates Silicone comes in ID 16mm (5/8) straight & formed. Silicone hose is usually super stretchy, so I assume 16mm will push on to a 17mm spigot/barb. https://www.gatesaustralia.com.au/-/media/files/gates-au/heavy-duty/application-data-sheets/heavyduty-product-range--silicone-coolant-hose.pdf" "Check out Gates 01 -007, 03-0010 & 03-0011, multi fit, 25 mm ID, coolant hoses" "Oil - Gates 8- GTH hose from Hydraulink. Be sure to order correct ID for your application."
-
I see worrying matters in the above photos (Blue & IBob). The corrugated oil & coolant lines & the alloy coolant pipes require at least two additional joins /pipe, compared with a single "rubber" hose - this introduces unnecessary potential failure points. The use of "plastic" filters within the engine bay is strongly advised against. The use of pleated "paper" filters is also strongly advised against.
-
The Comet's glory days • 1953 newsreel film
skippydiesel replied to Garfly's topic in AUS/NZ General Discussion
No ASIC! As a child, flew with my parents in a Comet (probably lucky to survive). Beautiful looking aircraft. Unexpectedly small interior. Love the pilot(s) flight cap & gloves - no recollection of these when invited up to the flight deck.😈 -
Hi Bobcharl, I have no comment on the corrugated metal hose supplied with some kits. All the information you need, to purchase non OM hoses, meeting Rotax specifications, can be found in "Started a spare parts list" for 17mm & 25 mm coolant hoses plus fuel & oil hoses. Unfortunatly there is quite a bit of tangential discussion to wade through but it's there. If you are can't find it/unsure - get back to me😈
-
Are you sure? - This is a Rotax 912 - there is no direct mechanical linkage to the fuel metering system (as in a LyCon). As I understand it, fuel metering is achieved through influencing the manifold pressure, which is a direct result of rpm. The RPM can be manipulated by the; throttle which is connected to the "butterfly valve ",No 3 in above diagram propeller pitch 😈
-
"...spare $400k tucked under the mattress.......150kts cruise with a 912ULS and retractable landing gear." It's certainly a Shark🤣 Sonex Legacy, Rotax 912 ULS, CS prop, fixed undercarriage, 150 knots (indicated 5500 ft AMSL) complete aircraft around the $140k AU mark😈
-
Okay - So I have a Rotax 912uls with Bing carburettors (below) - the amount of fuel being delivered depends on manifold pressure, which can be controlled either with the throttle/butterfly or the propeller pitch. It seems to me that, in theory, the manifold pressure/vacuum, at a given rpm, will be the same whichever governor is in use. My theory does not seem to hold good for load (needing power/fuel to move) must come into the system somewhere.?😈
-
(Not much activity on the Forum , thought I would put this up for debate) I seek your learned clarification on the above topic; I have always understood that a carburettor engine speed (rpm), is governed/controlled by the amount of air:fuel allowed into the engine. The PRIMARY mechanism that determine the amount of air: fuel is the "butterfly" valve, which the pilot controls using the throttle. The butterfly is opened/closed at will, influences the air pressure/vacuum in the carburettor body, which then opens/closes a needle valve allowing more/less fuel to mix with the air. Then there is the SECONDARY mechanism, the propeller. Depending on blade pitch the propeller will also act as a governor. Fine pitch will allow higher RPM, Coarse pitch will restrict RPM. So - IF I have my 912ULS at Wide Open Throttle (WOT) and I have a Constant Speed Propeller (CS) I know I can use the pitch of the prop to control engine RPM but can I also control fuel consumption. Put another way; With fixed pitch prop, I want to select 5200 RPM for a reasonably economy/ good power, cruise setting. With a CS, engine at WOT, can I select a pitch, that will reduce engine RPM to 5200 FOR THE SAME FUEL FLOW as above (no change in WOT)?😈
-
Doubters may debate all they want - my information is from the real world; ATEC Zephyr, Rotax 912 ULS, Fiti 2 blade ground adjustable prop, optimised for TO - 100 knots, 5200 rpm, consistent slightly over 12L/hr - flight planned at 13L/hr single pilot, 14L/hr two up - always had more fuel in the tank, at end of flight, than planning indicated. Sonex Legacy, Rotax 912 ULS, Airmaster CS 3 blade prop, 130 knots, 5000 rpm, still working on it however seems to be consistent at around 14L/hr, currently flight planning at 15L/hr. While engine setting RPM, pressure altitude & load will influence the fuel burn, for a given airspeed, I like to have a conservative fuel burn figure that I can use for flight planning. I am not intersted in minimal fuel to get the job done. Back to Moneybox's commuter flight, Cue- Northam. The only concern I have with my fuel calculations, is the Wikipedia information of 110 knots @ 75% power - should this be significantly incorrect, then the fuel planning is out. This is where my advice for real world performance testing comes in. Go fly at various power settings (preferably with full load on board) , work out the fuel burn for the whole flight - decide at what airspeed/power you will commute at and use this fuel burn + fudge factor/speed to flight plan. Not rocket science😈
-
I am working from Rotax published data AND my own experince of, about 15 years, flying behind a Rotax 912ULS - you want a working fuel consumption figure + a conservative fudge factor for planning purposes - you now know how to arrive at it😈
-
"I wish I could confirm everything you say skippy but it's a bit difficult to calculate while the plane is sitting in my backyard " I hope you will take the time to test fly the Sportstar - a significant part of this will be calculating fuel burn at diffrent power settings. Fill tanks to brim, Load passenger seat (if no passenger use ballast) Go fly for, say,an hour. I would start with a high power setting (worst case/highest fuel burn) 5500 RPM - Note altitude, OAT, Indicated airspeed & Ground speed- Land Note time (Hobbs) Measure fuel into tank to same level. Calculate fuel burn/hr at that setting. Same process at lower power settings. I would not go below 4800 RPM. The result will be average fuel consumed for the whole flight, including run up, taxi, climb, cruise descent. Try for consistency. Rotax publish estimated fuel consumptions at various settings; Cruise (98 RON) 4800 RPM, 65% /29.5Hg/13L/h 5000 RPM, 75% / 29.8Hg/14L/h 5200 RPM 30.0Hg/15L/h 5500 RPM 30.1Hg/19L/h I think these are correct (not sure)