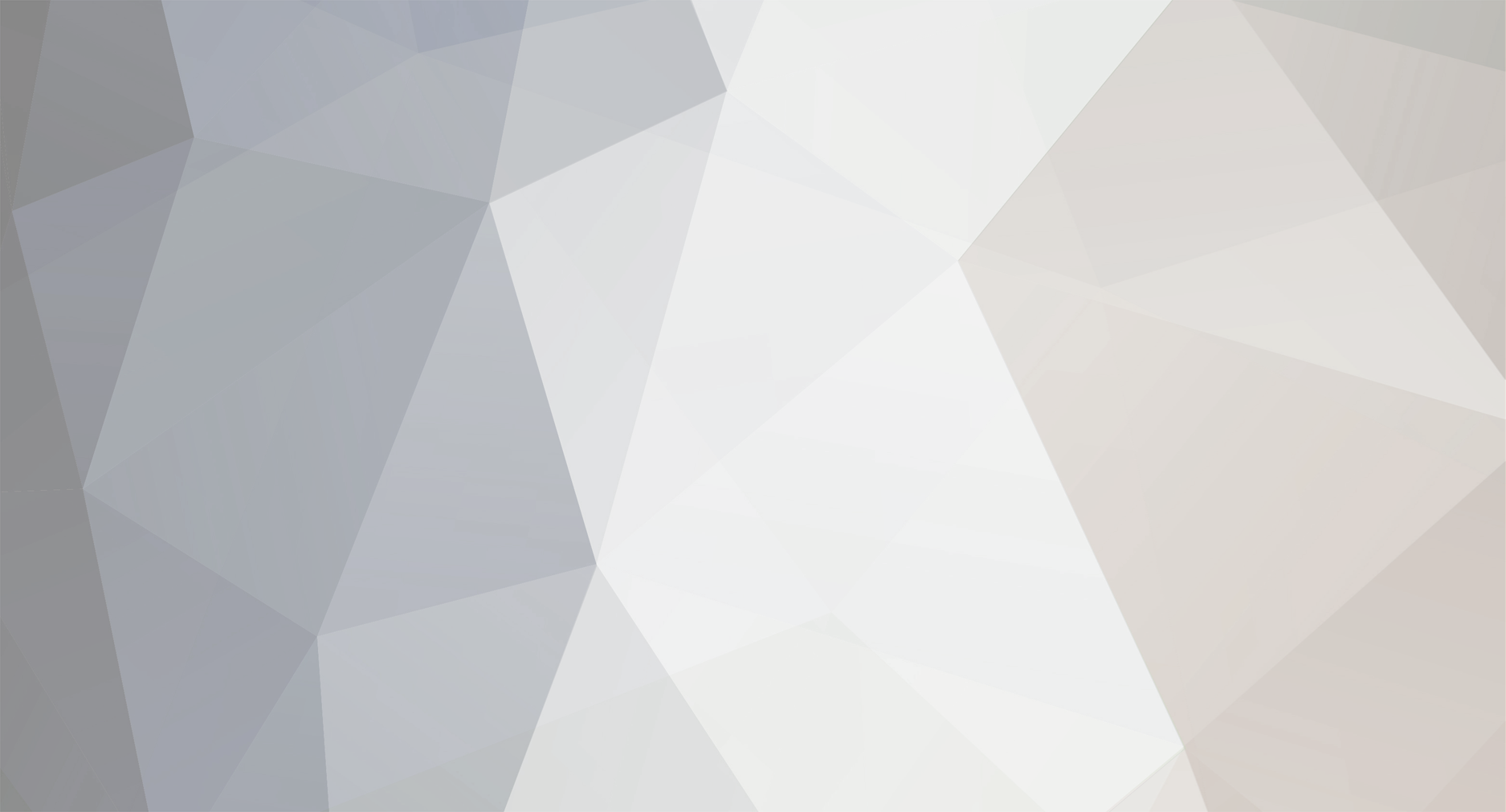
Markdun
Members-
Posts
357 -
Joined
-
Last visited
-
Days Won
4
Content Type
Profiles
Forums
Gallery
Downloads
Blogs
Events
Store
Aircraft
Resources
Tutorials
Articles
Classifieds
Movies
Books
Community Map
Quizzes
Videos Directory
Everything posted by Markdun
-
‘Quercus’ is the genus for the old world oaks down in the northern hemisphere. I’m not sure of the species for ‘pin oak’. The Quercus’ is often used in furniture and was used in boat structure. It has quite obvious ray parenchyma cells which grow out radially...this gives the wood grain an interesting look as well as making it more difficult to split, if I remember correctly from the several subjects Idid at uni last century. It’s also is hard and holds an edge well and resists denting, like our eucalyptus oaks...hence good for furniture. Unfortunately, unlike Huon pine, western red cedar and meranti, it is not dimensionally stable with changes in water content. It will warp with changes in moisture content....so not so good for doors, windows or external. Generally, I think a solid wooden prop would be difficult to make insufficiently strong if you have a reasonable airfoil ie. breaking from flight loads (thrust) or centrifugal forces. The issue are: (a) stiffness. Bending out of shape with rpm and thrust forces). Some shapes are designed so some bending changes the pitch...eg ‘scimitar’ shaped props; (b) robustness, that is, able to take the rough and tumble of a propellor for more than a week or two; and (c) not changing shape much with changes in moisture content. I’m with Spacey in that one can go way overboard on tge different types of wood. Epoxy glues, laminating, and epoxy moisture barrier and hardening coats can overcome a lot of issues. I’m sure an engineer could work out the forces, but empirically we know wood props work. Another, generality though is that the softwoods like Araucaria (hoop pine), Pinus, Douglas Fir tend to be stronger and stiffer than hardwoods (weight for weight)..this is because the wood cell fibres are longer and have tapering ends compared to hardwoods which tend to have shorter wood cells shaped like plain cylinders.....this is the reason toilet paper is made of softwood fibres (harder to tear) and newsprint (sorry, I mean propaganda print) can have a lot of hardwood fibre. I wouldn’t have a problem with using radiata pine or Douglas fir for a prop....as long as I could get clear straight grained planks radially sawn and I used several laminations and a good epoxy barrier coat. But both of them would be a right bastard to shape....neither sand well as the ‘late wood’ (dark growth rings) is very much harder than the lighter coloured ‘early wood’, so any sanding gives one big hills and deep valleys. Definitely spoke shave shaping. I mentioned stability in moisture content. All wood changes size with the seasons due to moisture content changes. This is why one has to frequently re-do prop bolt tensions with a wood prop. Some wood is better than others. Those Taswegian eucalypts sure have a nice look varnished, but they do shrink and grow. Unfortunately the shrinking and growing with moisture content changes is very uneven. Along the grain (longitudinally) there may be a change of less than 1%. From the centre of a tree trunk in a radial line outwards it’s likely to be 3-5%. Still not much. But tangentially, ie. along the growth rings, it can be 10%. So it matters quite a lot how the log is sawn into planks, or more likely, which planks you select. A plank with the growth rings parallel to the longer dimension (when looking at the ends) and with a nice flame pattern on the larger flat surface will warp and cup much more than a plank where the growth rings are perpendicular to the longer dimension. The Douglas fir main wing spars in my Cygnet (6”x1”x15’) are laminated because I could not source radially sawn planks. The other thing about those tassie eucalyptus (and many from the north island) is their density is highly variable. I think it was E.regnans that has a wood density ranging from 250 to 900kg per metre cubed. Spacey, I can’t see any significant benefit of the fibreglass. It just adds another failure possibility, ie de-laminating in flight, as well as weight, particularly if you have a hardwood prop. I know from boat building that most fibreglass sheathing really only ensures a minimum thickness barrier coating for abrasion resistance and moisture ingress, not structural strength.
-
Spacey, you will find a huge variation in the wood of any of the three eucalyptus species you mention. And I would doubt many people could tell the difference between the wood of one and the other without reference material and a good microscope. I wouldn’t be keen on meranti....too soft despite being a hardwood. I’m sure people could make a functional prop from knotty, tangentially sawn Pinus radiata....probably strong enough, but would it hold its shape, twist and withstand the odd collision with gravel and insects? I’m not sure of the point you are making regarding the broken prop? Did you break it on purpose, and what was that purpose? I would suggest you might want to consider your crankshaft. I had a very minor incident with a half VW powered Minimax with an idle prop strike (landing in long grass)...only a nick and crack on one blade from tip inboard about 10cm. 5 flight hours later total crankshaft breakage at 4500asl with uneventful out landing.
-
I have mostly used props I’ve made myself, but also commercial ones like Sweetapple and Sensenich. Currently I have 4 props for Jab 2200, 1 for a VW 1835 and another for a half VW conversion. I have the Sensenich 60x46 Jab ‘climb prop’ on my Cygnet and it spins up to 3200 at WOT at 65kts IAS and climb rate of 1000fpm and around 3000rpm cruise of 92kts. A great prop. for this airframe/engine combination. And very smooth. But I think the Sensenich ‘pitch’ is per the chord line and is more like a 42 or 43” pitch as measured on the flat rear prop face. I made a 4 lamination alpine ash (E.delegetenis) prop (60x47) for the Corby after another Sensenich 60x44 gave great climb but crap cruise speed....exceed max rpm. Another great prop, but just not right for the airframe. The alpine ash is much stiffer than whatever Sensenich make their props from and being without fibreglass the ash is lighter. This prop gives me 1500fpm climb at 70 kts or so at an rpm around 3100 and 110 kts cruise at 3200....still hits max rpm before Vne straight and level at WOT. So I’ve whittled a third prop; this time from 3 laminations of plantation hoop pine; 57x48. It’s a tad thicker (weaker and not as stiff as the euc) and has a wider blade area (hence the reduced diameter). I haven’t tried it yet as the current prop on the Corby is just too much fun as it is. On my props I find 3 coats of high modulus epoxy resin then 3 coats of polyurethane varnish (UV barrier) and a reasonably soft prop tape (from Spruce) on the LE works well. It’s not hard to manufacture yourself with a good square, straight edge and profile gauge, hand saws, chisel and various sanders The hardest thing is cutting the holes for the Jabiru spigots accurately. Tthe old VW conversions were easy by comparison because they were centred on a central mandrel. I’ve thought of prop copiers but it seemed like a lot of trouble. I think even really crap shaped props will work (assuming strength, balance tracking is ok).....it’s just the last few percentage points of efficiency that may not be achieved. The comments about the cost of doing it yourself are delusional. The timber is around $150, epoxy glue to laminate say $60 (though you will need to buy at least double that amount), sanding consumables ($30), epoxy saturation resin (another $100), plus syringes, gloves, brushes etc, high quality UV blocking pu varnish ($50), and then there’s your time drawing plans and computing angles and airfoils, sourcing materials, doing the actual work, making a prop balancer. If you can get below $500 per prop excluding your labour...good luck. But then if you make one, you’ll probably end up with making at least 3 before you are content to leave it be. So my guess is, factor on spending about $1500 for making it yourself. There are some negatives of making them yourself though. It is easy to make a poor performing prop by making the blade area too big and the blade too thick because you don’t want it to be too weak. For low HP motors those toothpick props that look ridiculously small seem however, to be the most efficient (some say a single bladed prop is more efficient..so maybe try cutting off one blade, replacing it with a counterbalance?). But how much is too thin? The bigger problem is that if you even consider your current prop is not ‘perfect’, you’ll end up having to make yet another one instead of reducing drag by replacing your gap tape, canopy seals, making strut fairings etc. And if you make a prop for someone else, remember that any and all performance issues will be absolutely due to the prop you made , not due to the engine being 30 years old, well past its TBO, the carb not jetted correctly, the fuel 4 month old, the aircraft exceeding its MTOW by 20%. etc etc. it’ll probably also be the source of noise in the intercom too.
-
Jasper, no debate from me on that. I just can’t fathom why the Ra-Aus seems to think shmoozing up to industry or providing services and information to the government is in members’ interests. It’s not our role or objective to be well regarded by industry, CASA, or the Government - except to the extent doing so advances members’ interests. How much do we charge CASA or the department for the information about members the Ra-Aus provides them? I don’t give a flying fig what AOPA, the SAAA, Qantas etc think of us....I just want to build, maintain and fly with the minimum of stupid ‘rules’ with no evidentiary basis of need. I’m an adult and I don’t need some patronising father figure to protect me from myself. I note an increasing number of long term members giving up; some flying outside the rules. How stupid is the medical requirement when you hit 70 (I think). The ‘standard is the same, ie. fit to drive a motor vehicle, but if you are old you have the added requirement of proving it. The only justification for such a rule would be evidence that older people are more likely to lie. Where’s the evidence for that? The staged inspections requirement in building is much the same. Where is the evidence of a problem, when it remains that the vast majority of incidents are pilot related? The Airservices class E airspace proposal was, and remains, a proposal without a clear objective or a problem to be addressed (except perhaps being a justification for Airservices expanding its infrastructure spending (ssr and ADSB coverage) to be recovered by increased charges on a diminishing fleet). But ten years or so ago Ra-Aus objected to a proposal that would have seen ADSB out devices like SkyEcho provided free to all of the Ra-Aus fleet (paid for by commercial airlines) that would have made more airspace available to us. Go figure. Rant over....now why has my Hall effect RPM sensor started giving me intermittent higher readings in the Corby, and what’s next on building a canopy mold for a new acrylic molded canopy for the old Cygnet?
-
Kasper, I agree that your analysis is correct about RAa jurisdiction. Moreover, in law, only a court can impose a penalty. The police, or CASA, similarly cannot impose a penalty. If the legislation allows they can issue a person with an ‘infringement notice’ (a fine) and the person issued with the notice can agree to pay the fine. But it is every person’s legal right to not pay the fine and require the police, or CASA, to take them to court and prove, as per George Pell, beyond reasonable doubt that they committed the offence. Raa-Aus does not have that legal power to take you to court (unless they can start a private prosecution). In fact, I know of a case where a CASA prosecution failed (pre AUF days) because the person in CASA that authorised the prosecution didn’t have the delegated authority to do so. where I think your argument comes apart is Raa-aus, does have a form of contract with members. This is the essence of corporations.....the members (equity holders) essentially have a contract with the other members as set out in the corporation’s constitution or M&A of association. This is what a member actually means (unlike gyms where ‘member’ really means customer). So while the RAa-Aus may go whistle Dixie in regards to imposing fines or periods of imprisonment, it probably can suspend a person’s flying privileges etc, refuse to register an aircraft etc. The ‘rule of law’ is more than just criminal, it also includes contract, torts, and equity (something our PM needs to learn). Of-course, if the person couldn’t care less about their membership and flies contrary to the tech manual etc that’s their business. Arguably, if Ra-Aus is aware, they could dob the person in to CASA. But it seems the precedent set by the reluctance of churches to dob in paedophiles or our current prime minister to dob in rapists or ministers illegally spending our money, it would perhaps be prudent if they kept shtum.
-
Skippy, a friend with a Rotax is ‘gunna’ put a TOCA on his to decrease warm-up time and reduce the workload involved in the manual TOCA here in Canberra.....gaffa tape on the oil cooler, which is what I use in winter on the Jabs to assist getting oil temps above 65C. I’ve just taken them off for the summer. Bruce, I machined up an alloy adapter fitting that goes between the Jab plenum and the Bing with an ‘airfoil’ shaped brass bar which can be turned with a screw driver and locked in a position with a lock nut. Mine just is vertical, but you could have one horizontal too. I haven’t bothered fitting it as my cruise egt spread is ok....it’s just on climb where it goes all over the place depending on the day and what constellation the moon is in.
-
The claim that the Bing CV carb is ‘altitude adjusting’ is just marketing BS. It’s a constant velocity carb. It’s not as bad as a plain slide carb but not hugely different in terms of getting richer with increase in altitude. It is much better than a plain slide carb in terms of ‘pick up’ and generally doesn’t need an accelerator pump. Size for size theCV also needs to be a bit bigger than plain sliders and for any given engine the plain sliders are argued by the motor bike racers to deliver a slight increase in power. In my experience the cv carbs are slightly more difficult to tune and much more sensitive to inlet runner lengths....you can get harmonic pulsing of the piston/diaphragm. like koalas and wombats, carburettors are doomed to extinction. Everything is going EFI....more reliable and cheaper. How many people now have glass panels for primary flight instruments? I’ve heard of one in flight EFI failure and that was due to fatigue cracking of a 10cent 10A glass fuse that powered the EFI computer. It should have been an automotive fuse designed for a vibrating environment. EFI is also doomed and will be replaced by E.
-
I’ve had few silent moments, all with VW derivatives and nearly always due to the idiot mechanic, me. First one was an EFATO from a broken head bolt at 100’, giving one good cylinder in a half vw motor. Zigged and zagged between the eucs and herefords. Cause was secondhand head bolts with a nick in them from the original vw cooling shrouds. Second was a broken rocker bolt in the half vw at 500’ over a dry lake. Third was a broken crankshaft at 4000’. I had previously noticed oil leaking from the prop hub seal ...but did I do anything? Fourth was several broken prop bolts causing a bit of a shaking in an 1835cc vw from wrongly using ht bolts. Landed in a rapeseed field after shutting engine down before it ripped itself off the front completely. Learnt to use malleable bolts and Bellville washers on the prop, but obviously not enough as my fifth engine out was, ‘is that a bit of an increase in vibration?, yes, better go land. Oh, the vibration has gone, and what was that shiny spinning thing that went whizzing off...must be the prop. Gee, the engine is running real smooth now. Now where is that airstrip?’ I’ve never had the ‘too much air in fuel tank’ problem, and I’ve generally considered an engine out as a ‘where have all the thermals gone’ issue that requires an out landing and fly accordingly....ie. only over terrain I feel comfortable landing on. Nev is correct....have a plan for when the engine fails. I would add....practice, practice, practice dead stick landings and speed/energy/glide path control. I do miss the spoiler/air brakes of gliders in my Jab powered Corby! I’ve been much more frightened on a commercial charter in a twin engine Cessna flying to Yuendumu with 8 govt VIPs on board. The plane was critically short of fuel because the pilot the previous day flew several hundred miles off course to the wrong airstrip and he thought that aggressive leaning would get us there. The last 100nm with lots of tapping of fuel gauges and then flashing red lights on the panel the pilot was flying above 4wd tracks between the sand dunes. We definitely took to the whisky at chairman’s lounge at the Alice, and the pilot of the red rat jet we then took to Brisbane kindly agreed to my suggestion he inform the passengers over the speakers that the plane would fly to the correct airstrip, Brisbane, and had more than enough fuel for the trip. My VIPs in first class cheered. Mark
-
For a Jab 2200 I would have thought 36lph would be about 150% of max fuel flow and ok? I was getting 40lph in my Cygnet, and 33 in a Corby Starlet (both Vw 1835, which drinks a max of around 20lph). Both just had a paper filter in the gascolator. When I upgraded both planes to the Jab2200 I kept the gascolator filter and installed the recommended inline filter....and gravity flow rates diminished to a tad over 30....not good enough, and I blamed the valve springs in the Jab fuel pump rather than the filters. I get over 60lph on both with electric. Still the max flow I’ve seen climbing out at WOT at 3100rpm with the Jab is 24lph except the 30lph ‘indicated’ when the facet pump is turned on....but that is a lie caused by pulsing. I do wonder just how many people test fuel flow rates....it’s not hard to take off the float bowl and collect the fuel in a large measuring cylinder.
- 15 replies
-
- 1
-
-
- need help
- pressure guage
-
(and 1 more)
Tagged with:
-
Seems a good argument to go back to no fuel pumps, mech or electric, and no pressure gauge, relying only on Newtonian gravitational forces for fuel transport from the tank to the carby, which I did for over 700 hours without a problem. If gravity fails there are much bigger problems to worry about.
- 15 replies
-
- 1
-
-
- need help
- pressure guage
-
(and 1 more)
Tagged with:
-
This is what I use. 0‑15PSI /4" Pressure Transducer Sensor Output 0.5‑4.5V/0‑5V for Water Gas Oil | eBay Output is linear....0.5V is 0psi, 4.5psi is 15psi. It Does need a regulated 5V supply. I tried a 0 to 10psi model but it failed almost straight away, so hence the 0 to 15psi one, which has given 100hours of no fault operation on a Jabiru engine with mech pump and facet boost pump. My display range is 0 to 7.5psi. (And there we go again with archaic units of measurement,) I know of one problem caused by fuel pressure monitoring on Jabiru and Rotax 4 stroke installations — when the electric facet pump is switched off the fuel pressure drops close to zero for a second or two until the poppet valves in the mech pump on the engine start working. No-one without fuel pressure monitoring has reported this issue. It’s the same logic as Trump has when claiming that increasing testing for Covid increases the incidence of the disease.
- 15 replies
-
- need help
- pressure guage
-
(and 1 more)
Tagged with:
-
Thruster 88 it seems the rest of my reply didn’t make it. But I wasn’t responding to ‘certified and TESTED’, but your previous statement which was ‘old and certified’. I maintain that just because it was done that way in the past, and even if it worked, it’s sometimes worthwhile to look at alternatives. The ‘old certified’ isolators I have come across probably worked reasonably well (‘worked’ as meaning providing reasonable safety), but they weighed a substantial amount. But I think the safety provided by a battery fuse provides similar safety for a big weight saving, and if I’m doing a power off out landing, not having to turn off the battery isolator is one less thing to distract me from getting my landing just so. The sick cow fable. Farmer A who had a sick cow attended the local annual field day. Farmer A explained to another farmer, Farmer B, about the sick cow’s symptoms. Farmer B responded that he had had a sick cow with the same symptoms and that the generally accepted approach was to treat the cow in a certain way. The next year Farmer B saw Farmer A again at the annual field day and asked A how it went with the sick cow. Farmer A responded that he did what Farmer B suggested, but the cow died. Farmer B then remarked that his cow also died when treated that way too.
-
That’s two fuse holders. The bottom one has a 150A fuse (starter motor), the top one I think has a 50A and goes to the master switch on the panel and a 25A circuit breaker.
-
Australia is being de-metricated!
Markdun replied to Old Koreelah's topic in AUS/NZ General Discussion
You forgot the 10 weeks to a month; ten months to a year. -
-
Australia is being de-metricated!
Markdun replied to Old Koreelah's topic in AUS/NZ General Discussion
Pubs are the worst. I go in and ask for a half litre of beer, and get the response ‘ do you mean a pint?’. ‘No, a half litre, 500mls’. ‘How about a schooner?’. And now I’m thinking of a multi-masted sailing vessel where the formast is shorter than the following masts. So I ask, ‘do you sell beer in ‘firkins’ or ‘pins’?, as I now could really do with 1/10 of a pin of beer? And then the barman gets shirty, ‘are you taking the piss?’ No, I say, it seems despite this being a metric country you want to use old British units of measurement. You will find ‘firkins’ and ‘pins’ are real, legitimate, but ancient, measures of beer, like pints. How about some claret instead of beer? ‘OK, a small or large one? ‘WTF does that mean; Do you ever buy petrol by the ‘small or large’? I was more thinking of a hogs head actually.... sometimes it’s just so difficult to buy stuff! BTW my aeroplane has a wing span of 52 cubits and a MTOW of 3009 D cell batteries. For those interested in aeronautical units, it’s quite an interesting story as to why UK (& Australian) aircraft ASI is in knots, but the USA use ‘mph’, whatever that is. The answer is about the number of seats in fighter-bombers (money cost), workload and the value of aircrew (human cost). The US didn’t care about any of the costs. -
Agree
-
I’m sure this set up is reasonably safe. But just to be clear: the logic of a system being ancient and on ‘certified’ aircraft means nothing. It’s the same as the fable of the farmer with the sick cow.
-
I’m no expert, but: if the isolator is a an electrical controlled solenoid even once turned off, you still have power to the isolator/solenoid control switch. If its a mechanical switch, it means you either have the battery in the cabin or a bunch of large heavy copper wires in there with you that will still be live too, or a mechanical link to the isolator if it’s remote from you. And if your electrical fire is due to a short in the AC side of your charging system and/or the voltage regulator, isolating the battery will not affect this. Finally, assuming an electrical fire is due to a wire overheating and burning the insulation on the wire & then cutting through your wingspar, that would be due to excess current... which would be prevented by an appropriate sized fuse or circuit breaker. There is one scenario I could contemplate, and that is a lightning strike. Andeven then, I’m not sure an isolator would help. I experienced a lightning strike on a yacht...it vaporised the vhf antenna, the current flowed down the antenna coax to the vhf radio, which caught fire, releasing all the magic blue smoke that makes all things electronic work, and there to the ground bus and to the engine to earth in the saltwater through the gearbox and prop. All, and I mean ALL, electrical items connected to the negative bus, switched on or not, was toast. FWIW & that’s not much, I use an old aircraft battery isolator solenoid as a 200A relay on the yacht to power the electrical anchor winch. Finally, that smoke in the cabin might not be electrical, it just might be that your trusty plastic oil catch can decided to spray 50ml of old engine oil onto your exhaust (don’t ask)!
-
Water? Do you have an espresso machine in the cabin?.... now that would be style, although require more landing stops! I make up my own CHT probes. Just bought some J or K thermocouple wire (can’t remember which),at one end expose the wires and twist together, then crimp into an appropriate, other end plugs into the RDAC. For EGT I buy $12 Chinese probes and mount them in a Jubilee clip with a 5mm stainless pull rivet (remove the pull shank and insert the 3.2mm egt probe into the rivet). Oil pressure & fuel pressure are 5v, 3 wire probes $25 each, as is the Hall effect rpm sensor & the Arduino current sensor. Only fuel flow sensors are expensive, but then I took an old Navman fuel flow out of retirement. I compared it to the Red Cube and could find no performance difference once calibrated.
-
Actually I have 3 fuses in the engine bay.A 150A for the starter motor, a 50A for the supply to the cabin and everything else, & a 15A on one of the AC wires going to the voltage regulator. I did have a 100A for the starter motor , but it blew, so I upped it to 150. The 150 and 50 amp fuses are mounted on the battery box with one large wire about 12cm long going to the positive terminal of the battery. I copied the set up from a friend’s Tecnam where we had to change one of the fuses which had corroded through (plane left outside in the rain by training school). The fuses in the AC charging wires is the one supplied with the Powermate regulator. It’s just a standard automotive inline blade fuse. BTW don’t use the fuses with a wire in a glass tube; the wire bends and work hardens with vibration, then breaks. Yeh, I know the Jab engines don’t vibrate, but I do have a friend who has an engine failure because of this.... the fuse was to his high pressure fuel pump on an EFI. Only use fuses where the fuseable element is supported.
-
Actually I have 3 fuses in the engine bay.A 150A for the starter motor
-
Yes, particularly when warming up the oil on those cold frosty mornings after the fog has lifted. I’ve never had icing in the carb in either with the Jab motor or the VW, both with CV Bing carb’s mounted in similar places at the rear of the motor & just below it. My VW set up had a ‘T’ there on the inlet runners with a flange bolted to the crankcase which kept it warm like the Jab inlet. Still I’ve known of people who have landed on a railway track wrecking their undercarriage, saying it was due to icing. So I’m cautious. Same for vapour in the fuel.... not so much for the Bing carb which has a reasonably large float bowl to separate out the vapour, more for the Rotec TBI carb I have on the Corby.... never experienced it and don’t want to! RF guy, I suppose people use the LM335 because most commercial engine monitoring systems allow for it as a plug and play. And it’s cheap and readily available.
-
fuel gauge for Jabiru
Markdun replied to Bruce Tuncks's topic in Instruments, Radios and Electronics
Bruce, Radiant make a cheap fuel gauge with a sender attached to the outside of a fibreglass tank. In my view you can’t have too much fuel remaining info, but if you are down to the last 10litres ie. the dregs, you ought to be finding a place to land rather than looking at a fuel gauge. I was flying a delivery of a Tecnam from WA to the east coast and we had that very long leg from Kalgoorlie to Forest with a forecast of some headwind. It was an unknown aircraft to me so I figured the resistive analogue fuel gauges and the digital fuel flow s as rough guides only, particularly so as I had to have the LAME that ‘fixed’ the fuel tank leak by removing the evidence of the leak by cleaning the fuel stain, re-do the job. On filling the aeroplane for the first time I was rewarded with an avgas shower getting into the left seat. Anyway, on the flight to Forest every 15 minutes I did a quick calculation of estimated fuel burned and fuel remaining from our 100l full tanks at Kal and compared this to the 3 gauges on the panel and my flight plan. All pretty much correlated. It would have been nice if the previous owner had connected the RS232 serial output from the GPS to the fuel flow meter so I could have played a bit with airspeed to find the lowest fuel burn per nm. The owner/passenger in the right seat was a bit amused; there were plenty of airstrips to land at, but having to flag down a train and organise a refuel would take weeks. We arrived at Forest with over 35l remaining, mainly due to true airspeed cancelling out the light headwind. -
Bruce, yes. I just used one of the spare ports on the MGL and hooked up an LM335 to it. It is inserted into the boss on the opposite side of the throttle butterfly shaft of the Bing carb. And yes, I use it to assist in determining use of carb heat as a sort of prophylactic against icing, though more often I use carb heat to cool down the EGTs sometimes. Ditto for the coil/ignition unit. My thinking was that as the MGL RDAC has the ports I may as well use them and the LM335 are only a couple of dollars.