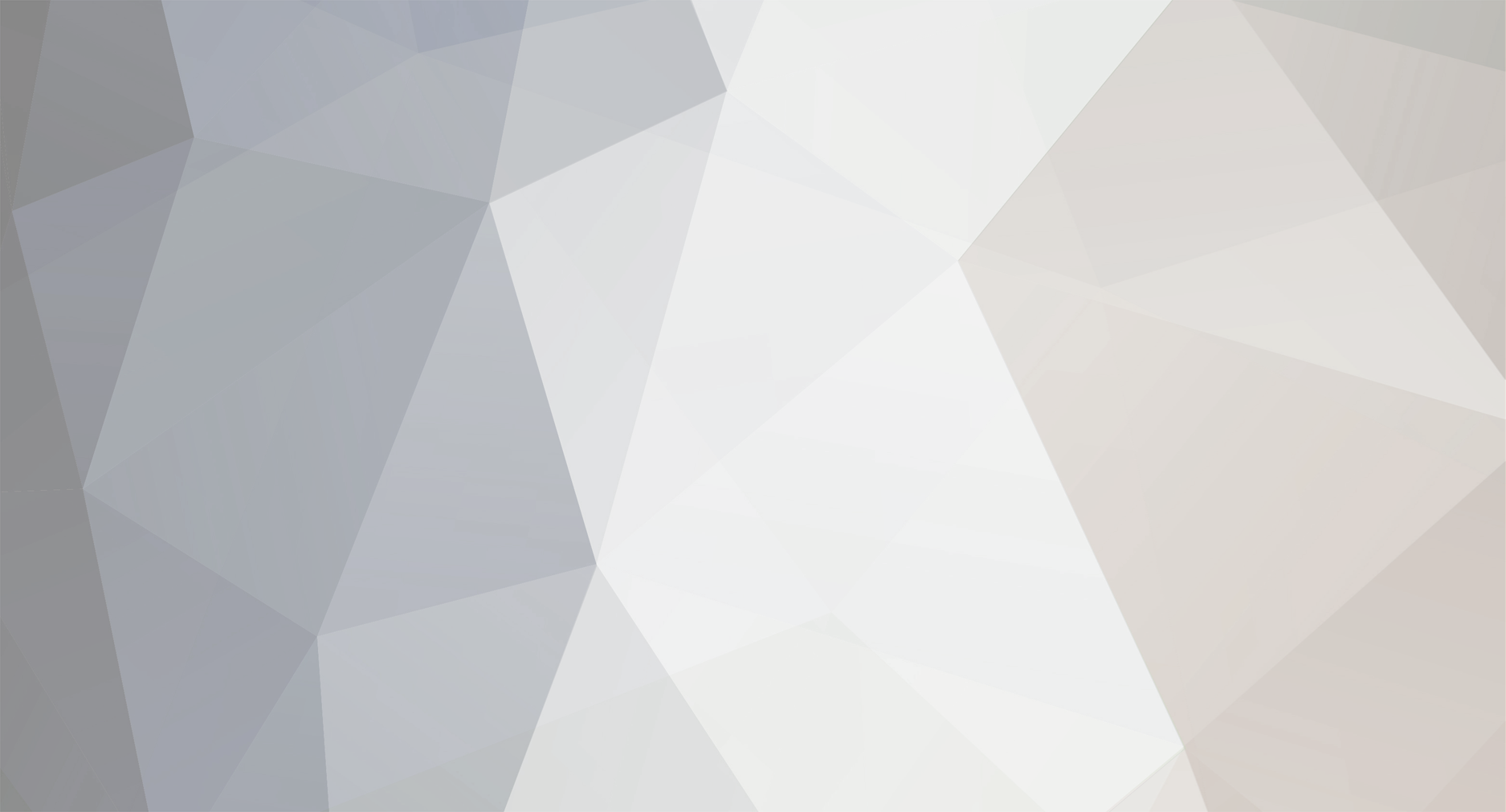
Oscar
Members-
Posts
2,485 -
Joined
-
Last visited
-
Days Won
67
Content Type
Profiles
Forums
Gallery
Downloads
Blogs
Events
Store
Aircraft
Resources
Tutorials
Articles
Classifieds
Movies
Books
Community Map
Quizzes
Videos Directory
Everything posted by Oscar
-
Measured using CAMit's gear, in their measurement room, by their chief measuring guy ( Ted) - much safer than me doing it - and to their factory-assembly specs. ( rods left for many hours to settle to their ambient temp. for measurement etc. ). I'll happily admit, I didn't even ask him for the measurements; if you know Ted, and he says it's right, then it's right. A man of few words, and not even Ian Bent questions his decisions... if Ted rejects parts straight off the machines, they don't go back for 'fettling', they are scrapped. Then, the reason why they were out-of spec. is investigated and corrected. We were mixing'n'matching parts from several engines, to build ours on a very tight budget (thanks to Ian Bent's huge generosity in even allowing us to do that using all of his facilities, and under the watchful eyes of his guys teaching us and checking us out at every step of the way, so Ted wasn't taking anything for granted in his measuring!). We were using CAMit's certificated tools and purpose-built sub-assembly workbenches with all of their special tools and with continual reference to their 'workshop' assembly instructions, which are in some places at least, a bit more detailed and informative than the Jab. Re-build manual. My co-owner and I had both built, albeit some time ago, reasonably successful 'hot-rodded' engines for club racing and rallye work; we know how to use most tools acceptably well. Following what we learned at CAMit, I can say with total confidence that I would NEVER attempt to re-build a Jab. engine at home (well, not to fly behind, anyway!) , even though I have a reasonably decent workshop. That doesn't mean I don't think other people can do a fine job, it just means that I recognise that I don't have the 'edge' of skills to do the job at the quality I saw being done at CAMit. Some of the work is time-critical - such as the case-closing assembly sequence, if using the standard Jabiru Loctite sealant on the cases - and without a lot more experience than we had, we simply could not have done it. (Watching the engine-assembly guys, who have done many hundreds of engines, was like watching an Olympic gymnast's routine - awesome). CAMit don't use that sealant on CAE engines...
-
What shells are you using? I was recommended King CR4445AM They certainly fitted perfectly straight out of the box, for a shaft and rods that measured factory specs.
-
Bruce: first up: absolutely all the best of British, mate!. Any glider pilot has a pretty good idea and experience of how to get it back on a small patch of ground safely, but I reckon I'm not the only one who'll be very happy to see your 'post-test' report! - to know that you're all good..and so is the wee beastie. I absolutely DO understand why you'd be concerned at that degree of egt spread, and two things pointing to one cause on the one cylinder, is pretty convincing, I also agree. You've eliminated the possibility of serious probe error; as for position error, when we were putting ours on, we noted that using the recommended distance from the exhaust flange put the probes at different positions relative to the bend in the exhaust stack so we sort of tried to 'average' that out a bit, but whether we managed anything at all (for better or worse!) by that, I have no idea. We didn't have my engine on the test stand for long enough to run egt reporting tests (for various reasons), and since the exhaust stacks are is in the direct prop blast, it wouldn't be likely to be very accurate anyway. If you want to get a fair idea of whether you're getting accurate (ish, even) reporting from your probes, maybe a lump of metal ( of large enough to be a useful thermal mass, but not so huge that you use up the energy resources of S.A. heating it!), with the probes making good contact, and an I.R. temp. instrument and a butane torch might get you somewhere. into the 500C range, anyway.
-
Nev - In case you got the impression from my previous post that I think it doesn't matter, I would never argue that one should NOT have egt monitoring, and on all pots. Especially with our dodgy fuel quality if using Mogas, I believe it's an essential precaution to have any 'out-of-normal' situation reported as quickly as possible so one can take appropriate action. My (probably badly-explained) contention is that with non-factory installations and instruments, it is going to be very difficult to be sure that the actual numbers you may be seeing on the instrument, are telling you the 'real' temps. that you are getting. With a fully-tested engine in proper testing conditions, where the variables can be virtually eliminated and the engine is torn down and inspected throughout the test process, it is entirely possible to determine that 'X' egt temp being reported by a specific egt set-up, is 'safe', or 'best' etc. - and for replications of that set-up, using TSOd componentry, you can have pretty good assurance that if you fly to the numbers you see, you are doing the right thing by your engine. If you are doing your own aftermarket installation (as I have done for my engine), I don't think it is probable that you are going to get the level of uniformity of installation that guarantees the same reading from each sensor, just for starters. Those old Gunson 'colourtune' plugs (which are still available, I just saw) were very popular 'way back when'... and in fact, I know that they were used, with a fibre-optic line back to the cockpit, in testing the R.R.-built Continentals for use in the Victa Airtourer (and found problems which irked R.R., btw). Just popping on a set of egt's and seeing some numbers come up that one doesn't like, doesn't necessarily mean that there is something radically wrong with your engine. Personally, if I had inspected the engine and seen decent evidence that on average, from real-life flying, the combustion appears to have been decent for all pots, I'd be more inclined to look at the numbers you are getting on the instrument as reporting a 'normal' situation and file that away as a reference point. Then, what you have is an 'alerting' set-up for sudden out-of-limit operation.
-
Becoming obsessed with egt spread, may not be the most productive exercise. Because of the differences in the exhaust runners, it is very difficult to ensure that you even have your egt probes measuring the same point on all four ( let alone six!) runners in relation to the standing wave pattern of the exhaust gas at any given combination of revs and load. Then, also, you have the problem of assuming that your egt probes are all registering with a similar accuracy - and who has test gear capable of checking at around 700C? I've set up a calibration test rig for cht senders: It uses a 100mm diameter x 300 mm or so long brass rod, heated by a stove element, into which we placed two laboratory-grade mercury thermometers. The cht sensors ( CAMit-supplied and from a highly-reputable supplier, not eBay specials!) were attached by tapped holes into the rod and the temps. at each sensor were also measured with a multi-meter temp. probe. The temps. at the test rig and the recording instrument were carried out with the complete reporting circuit to the instrument being that attached to the engine. It took nearly four hours to record both the rising and falling temps at 10C increments. The results showed that the cht sensors were reporting at the instrument, within 2%. And, we found that there were peaks and troughs in the accuracy throughout the range: you cannot just take one or two measurement points and assume that the reported temps. are linear with temp. changes. A reliable, measurable 200C is easy to achieve in a calibration set-up; 700C is not. It's a very long bow guess to assume that any differential of your test of your egt probes in boiling water can be extrapolated to the same error at 700C. A 2% error factor, at the critical cht's, is nearly 4C. Add in a bit of very minor deviation from 'best practice' flying, and you'd easily get 10C +/- of optimum for climb-out. And: that measurement is across four or six cylinders with identical temp. take-off points.. Now, let's think about realistic errors for egt's. ASSUMING all of your egt's are positioned absolutely symmetrically with regard to the standing wave patterns for the exhaust runners, a 2% reporting error at 700C is 35C. I've added egt's to my own Jab engine, and I would not dare to claim that they are absolutely symmetrical in position - and we tried damn hard to achieve that. I would not suggest that what gets reported is within 5% of actual. When I built racing engines, we used 'plug-chop' to check the individual mixture to each cylinder, to tune our Weber DCOE carbies delivering one throat per cylinder through a straight (and very, very carefully matched) intake tubes to the cylinder head. 'Plug-chop' means a full-power run down the main straight and cutting off the ignition at full power and high load, so one could see the deposits on the plugs and identify if any cylinders were not operating at maximum combustion efficiency. We used colour-charts to determine the efficacy of combustion temperature to the optimum. 'Plug-chop' is NOT a good idea for air-cooled engines: it would introduce severe thermal shock. However, I suggest that inspection of the individual heads and piston crowns will give a fairly good indication as to whether your Jab. engine is running - in real-life conditions - reasonably, or badly. No matter what your egt instrument reporting is telling you, if all your cylinder heads and piston crowns have a uniform 'warm-caramel' colour with minimal deposits, then you are chasing your tail to try to get your reported egt's to all match. Your time would be better spent on improving the head cooling efficiency.
-
Sorry, absolutely right, I meant to add 'and run it under load', inadequate coffee intake for rational; thought...
-
Bruce, I seriously think that's a bad idea. If you do try it, please fly off - if you get that far - in conditions where you can pull carb heat and still climb to a safe height and land again with carb. heat on - assuming that your carb. heat bypasses the air filter completely. May I respectfully suggest at least a primary test, off the aircraft? Take the SCAT hose off, and attach it to a strong vacuum cleaner , set it up with a decent approximation of whatever bend is normally in the SCAT hose ( and secure both ends somehow so that the SCAT hose remains approximately in the same curve as installed; a couple of saddle clamps, a a bit of board and some racer-tape may suffice for that). Run the vacuum cleaner and note the effort introduced by the SCAT tube. Then, set up your straws in the SCAT hose and repeat the test and see how much extra load (if any) that places on the vacuum cleaner, and whether that load tends to distort the SCAT hose. A vacuum cleaner doesn't produce a hell of a lot of vacuum, but it'd be a better than nothing test. An even better one than that, would be to use a real engine of around the same capacity - a Subi 2200 engine would be perfect - and run it at the same revs as your Jab engine runs i.e. up to around 3200, so it's flowing the same air volume.
-
There's probably something in the FAR's that doesn't approve it - but personally, I'd use it...
-
Well, that's why I deleted it!. Didn't fit the circumstances, you were ahead of me already. I can only comment on the early airboxes, but it's normal practice for GA that the hot air will bypass any filter. I agree that silicon hose SHOULD be a better option, but there's a reason that there are requirements for negative-pressure handling. As long as you don't have a serious kink point, I personally believe that silicon hose is a good alternative; the safety factor is probably if the silicon hose is moulded for the turn.
-
JJ - just before you throw on that silicone hose... An engine is a remarkably good vacuum pump, upstream of the cylinders. The reason that SCAT rather then the smoother SCEET tubing is mandated, is because of the possibility of the inner liner detaching and blocking the air inlet, due to vacuum. SCAT does have some resistance to vacuum ( though not much). I like silicone hose - BUT, if it can become pinched, then the vacuum could close it off almost entirely. The possibility of a constriction in the primary air entry route, is the reason why the hot air bypasses the air filter - it's the 'fail-safe' for induction air.
-
My extraordinary plane build ...
Oscar replied to bexrbetter's topic in Aircraft Building and Design Discussion
Bex - not to be pedantic, mate, but aren't extrusions produced from a die, not a mould? Are you SURE your supplier has the cow by the correct teat??? ( Assuming that they aren't going to supply noodles, that is! -
My extraordinary plane build ...
Oscar replied to bexrbetter's topic in Aircraft Building and Design Discussion
Where, oh where, is the button for 'Oh gods, not AGAIN'?' -
Bruce, that rubber flap is there to prevent backfires blowing the airbox apart / the scat inlet tube off. NACA ducts are not particularly good at scooping air against any back-pressure; they are a low-drag way of allowing air to move from a higher-pressure area into a lower one. The worst problem for Jab. induction, is swirl from the airbox and cobra-head, any flow-straightener in the scat tube will not do anything useful. It took the guys who transplanted a 2200 into a motor-falke a great deal of trouble with flow-straighteners etc. to try to get fairly even chts and egts at all throttle settings; they had the whole inlet tract extensively instrumented, and did many, many test flights over almost a year. The whole issue almost becomes a 'black art', without really serious testing regimes, to get a decent balance across the operating range. The Jab. USA stuff is probably a very good place to start with your experimentation.
-
And the weight / stall speed limitations for EASA country recreational ( or Ultralight category) registration being what it was /is, is the reason why Jabiru had to develop the 'UL' spec. Jabiru from the Australian spec. machine despite the fact that Australia had reciprocal rights for T/C recognition - despite our more generous specification. Sod-all to do with the actual competencies of the aircraft going in either direction into /out of Australia in practical terms, a question of the 'box' of regulations into which the respective aircraft had to fit to gain registered status.
-
Only, if you can guarantee equal air delivery to each cylinder.
-
I agree that multi-point efi would be a huge step forward - and Jab. engines for drones used by the Israeli drone manufacturers have this already, they come out of the engine factory with multi-point injector housings installed in the inlet tubes - BUT you can't use them on a certificated / certified aircraft - only an e-LSA / 19-reg / VH-experimental. This is not a case of intransigence by the manufacturers, but a failure by the regulators to adopt an intelligent approach to engine reliability risk assessment. Multi-point, egt-responsive fuel mixture control solves WAY more problems than it potentially introduces, but the regulators have an aversion to allowing any 'new' risk into the matrix - instead they prefer to continue with 'known' risks for which they have established 'fixes'.
-
DooMaw - building a STOL
Oscar replied to Head in the clouds's topic in Aircraft Building and Design Discussion
Mighty strong - absolutely.... lovely work, as always. -
Well, yes Roscoe, but the rest of your aircraft looks fantastic as well. They blend....
-
Oh, bugger. Then, Jabiru has the entire say. A huge pity - a 230 with a CAMit six, would be just the duck's testicles for a great aussie general-use airplane. If I win Tatts, I'll do one in a heartbeat - or half of that.
-
Russ - it depends on whether it is a 'C' reg. - meaning Certificated, according to compliance with a CASA-accepted international ICAO standard ( in the case of a J160C - BCAR S) plus a Part 21M engineer's approval of 'compliance' - or a 'D' model, Certified by Jabiru as ASTM compliant. The differences are, in practical terms, negligible. There is NO difference in the airframe, the engine weight or performance etc. WHAT the difference is - is that in the case of the "C' - Certificated' model, a Part 21M engineer can certify that modifications comply with the standard under which the Certification was issued. In the case of an ASTM Certified aircraft, it is the manufacturer's sole responsibility to determine whether any modifications are acceptable to IT - as the 'authority' responsible for the aircraft. Any individual manufacturer is not going to be routinely bothered with 'approving' a modification to its aircraft - since it would have to test and be assured that the modification is acceptable, in order to take the legal responsibility of having approved it. Some are: I know that Tecnam, for instance, has a very good approach to someone designing a fix for a problem to its aircraft, while Foxbat takes entirely, and somewhat aggressively, the opposite position ( though ultimately, Foxbat did improve the poorly-designed component..). So: if you have a J 160C with an engine that does not correspond to the J160 TCDS, but that has a Part 21M engineer's certificate of compliance, you should be OK. However - the really stupidly mired MARAP initiative, has complicated even that process. CASA needs to be taken out and kicked ( again, there is a conga-line of kickers awaiting it) for obfuscating the MARAP procedure. Your solid-lifter engine SHOULD be kosher. I'd happily - more happily - fly behind a CAMit engine than a Jabiru engine.
-
Anjum - good for you!. I've worked on rebuilding a Thruster - in fact, a family member has about four or five of them - and you won't catch me flying in one, unless bound, gagged and anaesthetised. But, I accept they have their place - preferably, tethered and between your deckchair and the sun. I've been very extensively rebuilding an early, crashed ( and written-off) Jab. over several years now ( it's a hobby..) and that has included quite a bit of 'glass repair work - which is why I am a bit 'hot' on the differences between c/f and a simple 'glass composite structure. I could not have done the work I have done, to the wings and fuselage, had it been c/f - well, at the very least, without the facilities of McConaghy's Yacht factory, that build some of the top racing c/f yachts in the world (Wild Oats, for one). A Jab., operated with due respect to its nature and limitations, is a damn good general-purpose aircraft and a very safe one, both from a structural and an aerodynamic POV. They have no particular (or peculiar) aerodynamic vices, and they are simple to inspect and maintain. They handle Australian conditions very well - including rough strips, hangar rash, being stored outside in conditions from any place in the country, be it wet and humid to dry as a witch's tit. They are most definitely NOT Ferraris, more like Landcruisers. You don't see a lot of Ferraris off the beaten track..
-
Anjum - you're welcome. It IS an important distinction, because it goes to the heart of the Jabiru design and manufacture philosophy, and has implications for the performance as well. Jabs are very simple aircraft, with a very low parts count, and are very tolerant of hard use. They can be repaired simply ( for most things) and reasonably cheaply, by people with good 'glass skills and the requisite knowledge. They don't have that 'edge' in performance of the high-tech machines coming out of Europe, but they do have good, 'solid' performance, and in Australian summer conditions, you will find that they will cruise in safety at a max. rough speed that often exceeds that of the Euros. They bounce well.. and the total cost of operation is one of the major reasons why such a considerable percentage of the RAA training fleet WAS made up of them, prior to the CASA action.
-
Jabirus are NOT made of carbon fibre composite. They are made of a simple, hand-laid, ambient-temperature curing epoxy and glass fibre composite, which is precisely the reason that they are flexible and extremely impact-tolerant. If you have every seen the result of a serious (double-fatal) crash of a cabon-fibre shell cabin, as I have, you will immediately understand why the occupant-protection capability of the Jabiru is far better than for the carbon-fibre aircraft.
-
With respect to everybody who has contributed to the discussion on ramp checks etc. - this has veered so far off the thread, that it should (and usefully) be placed on another thread. It is an important matter for discussion, but it progresses understanding of the possible causes of this tragic accident not one whit. IF - and I stress that - this aircraft had a W&B issue that caused it to go into an unrecoverable flat spin from a presumably normal training sequence (and the Instructor concerned had such vast experience that it is hard to imagine that he would have allowed an exceptional situation), then surely the focus needs to be on the factors that caused it to be in that condition. It was a originally a one-off, 914-engined version modified from the model that had been tested for compliance with the spin recovery requirements, that had been subsequently returned apparently to a 'normal' specification, 912-engined, model. The 912-engined model is, I believe, routinely used for training and I am not aware of any problems with them. This thread needs to examine and deliver information, when it becomes available, as to why this specific aircraft apparently got into the situation that led to a tragic crash. I use the word 'tragic' here, in the sense that by all reports to date, it is suggested that the flight was a routine, low-risk training flight with both the Instructor and the trainee experienced pilots - not some high-risk episode. It was not some 'take-off after last light', or 'fly into IMC conditions' episode. There are some very serious questions to be answered (and we may never get all the answers). But - those questions are NOT ones resolved by debate on ramp-check issues. Can the Administrator please move the 'Ramp-check' debate to an appropriate thread of its own, and return this thread to examination of the relevant issues?
- 182 replies
-
- 10
-
-
stall practice: what can go wrong?
Oscar replied to cooperplace's topic in Aircraft General Discussion
Russ - you need to go fly some gliders - seriously. I am crap at powered aircraft landings - I arrive over the fence fine, but then try to get the thing on the ground as short as possible, from glider experience, and it doesn't translate well. BUT: when you have no engine to modify the approach, you focus on being always in the circuit at about 45 degrees angle of declination to the threshold. You DON'T worry about hitting 'turning points' in the circuit and using power to compensate for being too low, or reduce power to compensate for being too high. You use the brakes to wash off excess kinetic energy..at the last moments. You keep height in hand, and waste it through sideslip when it is absolutely redundant. When all that training comes into play, is when you have to outland on a patch of ground you have never used before. When the lift dies unexpectedly, you select a field, and you HAVE to land on it. There are NO markers - other than a fence line. You select a 'target' arrival point, and the concept of flying a standard circuit is complete pants: you fly whatever pattern 'gets you to the Church on Time.'.. IMHO, the 'standard circuit' is a convention introduced to ensure that a sky full of aircraft don't collide. I flew as a passenger with a family member as pilot, from Mittagong Strip into Bankstown quite a bit in the late '60's - and in foggy days, he would track down the George's River at well less than 400 feet, under the fog, turn left, and land on a taxi strip. The Tower ignored him until some CFI's of FTOs on the strip complained that their students were starting to consider that the main strips were optional..