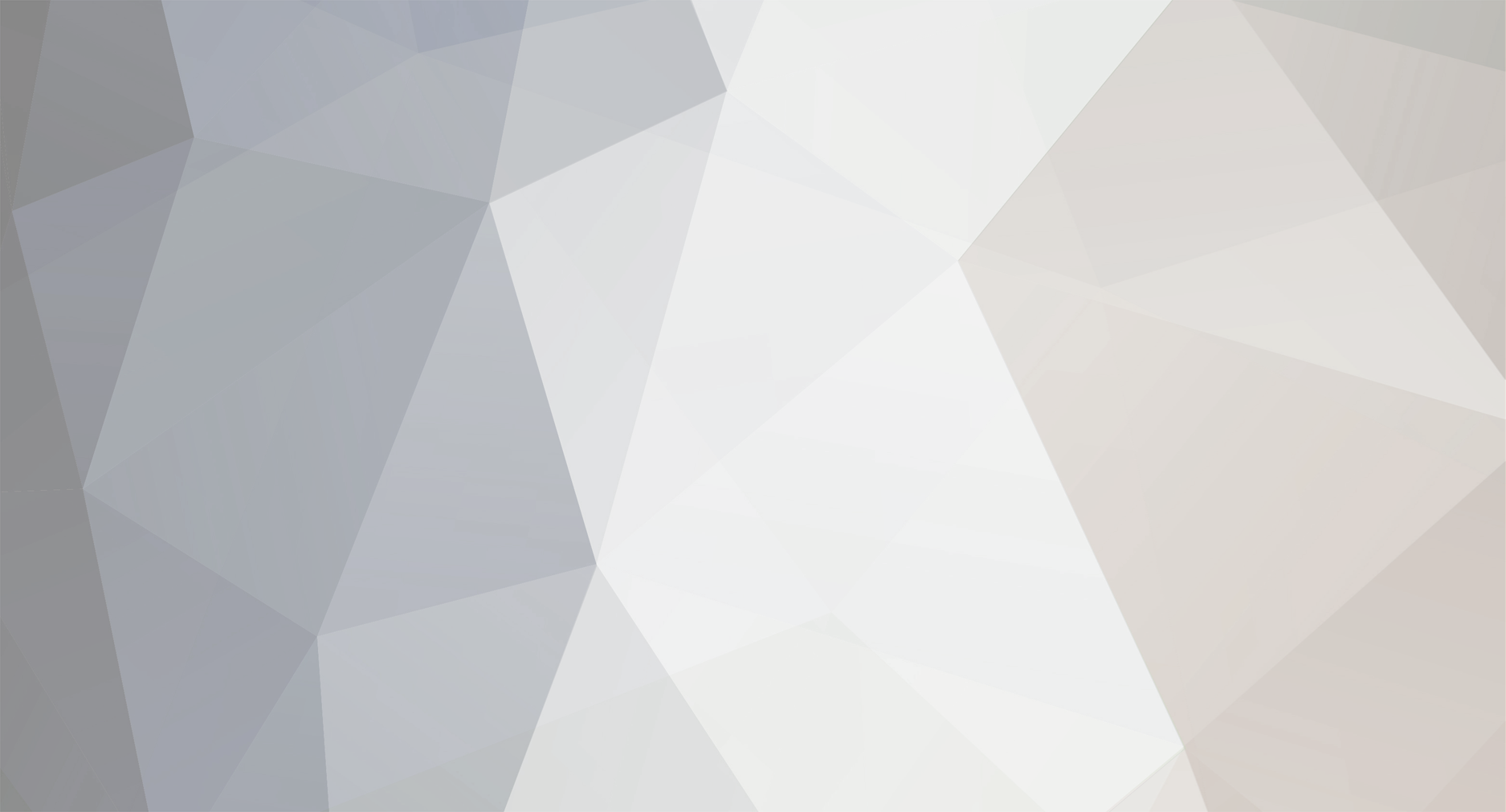
Oscar
Members-
Posts
2,485 -
Joined
-
Last visited
-
Days Won
67
Content Type
Profiles
Forums
Gallery
Downloads
Blogs
Events
Store
Aircraft
Resources
Tutorials
Articles
Classifieds
Movies
Books
Community Map
Quizzes
Videos Directory
Everything posted by Oscar
-
My extraordinary plane build ...
Oscar replied to bexrbetter's topic in Aircraft Building and Design Discussion
Actually, Bex, you've seriously piqued my interest. Who is your 'Mate, a well-known engine designer and builder?' Oz engine designers are pretty thin on the ground, AFAIK. I can only think of two with any claim to aero-engine design and one with actual experience of aero-engine building, at least in numbers to suggest 'well-known' status. Of course, we have LOTS of good 'engine-builders', in the sense of assembling seriously good high-performance race engines with many bespoke parts of their own design, but a total, certificated / certified aero engine design and manufacture? It's a long way to the TBO, if you want to roll your own... -
My extraordinary plane build ...
Oscar replied to bexrbetter's topic in Aircraft Building and Design Discussion
Cheaper, better, maybe a bit slower... But I'll bet Raptor don't have such spiffy benches. -
My extraordinary plane build ...
Oscar replied to bexrbetter's topic in Aircraft Building and Design Discussion
Jeez, guys - give Bex a break!. I mean, we have Raptor aircraft promising a five-place, 230 kts cruise, 7 GPH (25 litres/hour), for about US$130K . Pressurised! For $50k, you can (maybe) get a brand new trike..... For about $50k, and your effort, you can put a Sonex into the air. Bex is proposing much more than that, for much less cost. What's not to like? -
The early Jabs. used those, too - re-stickered Facet. But they won't handle any aromatic fuel, Jab issued a warning on them several years ago, from memory.
-
With just 170 kgs of usable weight, that means that with two standard crew at ( I believe, 77 kgs for the FAA standard?), 26 kgs of fuel load available. A wee bit over 2 hrs range, but with 45 minutes of fuel required to remain at the end of a flight, you're looking at 75 minutes endurance for your flight plan. So, hops between stops of the order of maybe 150 NM... That's actually not unexceptional for the earlier crop of Euros ( as we discovered with the rego debacle several years ago, where some where found to be only effectively single-seaters for much beyond a couple of circuits! - witness the MTOW thread for a classic example). So, for a bit of a toddle around your local site and maybe a 'hamburger run', this thing could be fun, but you'd have to be a patient man to throw on your Maverick suit and helmet, climb aboard with your mate in his Goose outfit and head off to Ausfly at Temora from say Caboolture to buzz the strip...
-
Ignoring Turbs will give you more headspace to chew through the real issues. Works for me...
-
My extraordinary plane build ...
Oscar replied to bexrbetter's topic in Aircraft Building and Design Discussion
And here's the perfect interim engine for it: (and Aussie, to boot): http://www.coaxe.com.au/video As you can see, they already have a prototype running (well, turning, with the input of a small electric engine), and powering a pair of automobile fans almost properly located on the shafts! Disclaimer: the Director of this company approached me one day in the local Aldi carpark at Mittagong, and I'd have a job right now helping with the build if I could invest, oh, $100K or more and pay my own wages. Sadly, I'd left my chequebook in my other pants and missed out on the opportunity of a lifetime. -
My extraordinary plane build ...
Oscar replied to bexrbetter's topic in Aircraft Building and Design Discussion
Well, it won't really be an issue when everybody is attending the Bunning's Saturday Afternoon 'Build Your Own Aircraft' workshop and sausage sizzle... If it'll fit in the hole, that'll be beaut. Tighten it down and Bob's yer uncle. A revolution in aircraft building, it will indeed be!. -
My extraordinary plane build ...
Oscar replied to bexrbetter's topic in Aircraft Building and Design Discussion
Aircraft spec. bolts are in inch sizes.... -
Fabulous picture. I remember, when walking around the NASM one at Silver Hill ready to be taken down to the main Museum, how massive the 'paddle' blades on the prop. were, for what is a compact aircraft. As with all NASM restorations, it was 'concours' condition - not really 'production' finish - and that one is every bit as good. I've had the good fortune to see many superb refurbs on warbirds as part of my job when at the AWM in the USA, (US Air Force and Navy Museums, San Diego and 'Planes of Fame' and at Duxford and the Mosquito museum in the UK, close up, and the 190 has a unique presence. If you might liken an Me109 to a Doberman, then the FW190 is a Rottweiler - a very, very fit Rottweiler...
-
DooMaw - building a STOL
Oscar replied to Head in the clouds's topic in Aircraft Building and Design Discussion
Actually - small thread drift here, HITC, I hope you don't mind, but it does hark back to your own experience mentioned re extreme use of rudder in a dangerous situation - that 'low-flying aircraft check', saved a horrible accident once. We were winch launching; a Blanik with two aboard had just given the 'all out' and was starting to roll, when the CFI screamed 'bung off'' - which they did. About five seconds later, and an F111 did a pass straight down the centre of the strip at about 50 feet and maybe 350+ knots - would have collected the wire for sure. The CFI had done a 'Darby-check' glance out of habit - hadn't actually seen the F111 coming but noticed a patch of heat haze where there should not have been one and simply reacted out of one of those 'prickles on the back of the neck' moments. The pressure blast, dust, grass and turbulence, not to mention the noise 'thump', left us all shaken to hell and several gliders that had been parked tidily awaiting launch, parked most untidily - but undamaged. The CFI (Noel Winterburn, damn good bloke and Instructor, of course) apparently left the RAAF in no doubt as to his feelings in the subsequent call he made to complain... -
DooMaw - building a STOL
Oscar replied to Head in the clouds's topic in Aircraft Building and Design Discussion
DJP - be fair!. From what I've seen, most Ag. pilots don't even drop the tail onto the ground until they're pivoting on one main beside the spread heap / chemicals truck.. Taxying? Waste of time... Cross-wind? - minor irritation... I used to fly gliders a bit at Forbes, and part of the 'all clear above and behind' check, was a scan of the horizon to see if Darby Munro was headed in. Darby simply flew straight back to his hangar from wherever he'd been working, and from the air, one could see the shadow of his plane get slightly further away at fence lines. He'd long, long ago decided that 'circuits' were a waste of time and avgas. His departures were more easily noticed - if you heard an engine revving, he was coming from his hangar, but on what heading, you never knew. You just held off launching until he'd buggered off. Local legend had it that he'd - one time only - taken his Pawnee down to Bankstown for a check of the instruments and had returned swearing that he'd never go again because he'd had to get to 1500 (?) to enter the circuit and that was bloody dangerous.. AFAIK, he lived to a ripe old age - lack of tailwheel use notwithstanding.! -
DooMaw - building a STOL
Oscar replied to Head in the clouds's topic in Aircraft Building and Design Discussion
That's a very reasonable observation, though it's also obvious that HITC has well considered the bending potential for the long tube and increased its O.D. considerably. But, of course, as the tube bends, the alignment of the rod ends falls increasingly outside the centre-line of the tube, increasing the bending moment... and also stressing the rod-end threads (though, it looks to me as if they are 1/4" so should be well strong enough). I've been rejuvenating the complete rudder circuit on my Jab ( early LSA55), which uses 3/16 male rod ends, and I've been less than impressed by the number that have bent threads. (They'll all be replaced.) They are obviously strong enough for the job in radial loading, but (and I think this has been due to long-term bloody poor maintenance practices), since just about all of them have some axial deflection in their travel and haven't been properly set-up, they've suffered from inadequate stand-off height and have had the threads bent observably by eye (and more observably, when put in a lathe chuck and spun). Some of the standard AN 3/16 washers have ended up bent like belleville washers, with strong witness marking on the rod-end housing attesting to the contact. (also most did not have any form of retaining washer on the outside of cantilevered bolts - not a problem with HITC's application, for sure!) I've used a pair of unbent ones to determine the required stand-off height - and as HITC said in his post above - the best way is actual assembly and observation, and the patience to go back to the lathe etc. and make the fine-tolerance bits to fit the case. Getting it RIGHT, takes a whole lot more time and effort than just getting it to FIT. It's actually satisfying work, for a perfection-junkie (which is my way of avoiding the term 'anally-retentive'), but I am sure any CAR35/Part 21M engineer will tell you that a goodly part of their work has come from correcting stuff that has just been 'made to FIT', instead of getting it right in the first place.. Edit: just saw that HITC is ahead of us both, and has the situation in hand. HITC - I have a considerable length of 80-duro poly bush rod, of 50mm diameter, I got to make up the one missing compression do-nut on my Jab front leg, and would be proud to contribute a bit for you to make up a grommet for your retainer, if you'd like it. P.M. me with the postal address... -
A family member and ex-CAR-35 engineer, had more problems with getting his professional fees paid by Doctors than any other group for their maintenance issues. Yet I know a seriously good Orthodontist who has built his own GA-exp aircraft, and is a damn good pilot. Can't put people rigidly into boxes, though some tend to gravitate towards a recognisable norm...
-
Considered Andy Campbell's operation at Jaspers Brush?
-
"developer faces jail for flying plane"????
Oscar replied to cooperplace's topic in AUS/NZ General Discussion
Some years ago now, a guy who lived in a converted shed on our farm ( long story..) had a small road traffic accident. When the Police got things sorted, it turned out he only held a Ukranian driving licence, issued in 1946... and he'd been driving in Australia since about 1948, when he emigrated here. There is a fairly well-authenticated story, of a case where an order for a new Cessna 172 elevator was sent to Rex Aviation at Bankstown - then the Cessna agents. There wasn't enough information on the order for them to identify the correct part, so they got onto DCA (the forebear of CASA at that time) for further information. DCA couldn't trace any aircraft to the owner or location - a Station somewhere near where NSW, Qld, SA and NT meet.. So, they had one of their Inspectors drop in when passing by. What followed, I would not believe as anything but urban myth, except for the fact that a family member was working at DCA at the time and had been involved in trying to track down what actual Cessna it was. You need to place in perspective here: this was the era when Australia 'rode on the sheep's back', and HUGE wool cheques were not uncommon - in good years. He duly landed at the Station home strip and saw a 172 tied down, with a bent elevator. A cheerful station owner came out to greet the Inspector. 'I'm from DCA', said the Inspector. "Great - Dingo Control Authority - I need to talk to you guys' was the response. The story was: this Station owner had been at the Birdsville races quite a few years before, and had placed a large side-bet with a mate on the outcome of a race. He won; the mate didn't have the cash, but handed over the key(s??) to his 172, and the Owners Manual. The winner had gone back home, read up the manual, cleared a simple strip out the front of the Homestead and several weeks later drove back up there and flew it back home. He'd operated it for something like 8 years - never off the station - for stock/fence etc. inspection - when one day, he taxied in near the tank stand where he usually tied it down and it rolled back in the wind, hit the tank stand and bent the elevator. His Avgas came in on the same truck with the diesel and everything else, from Broken Hill. The DCA Inspector informed him that he would HAVE to place the aircraft back on the register, but stated that he would ( and did) arrange for a PPL to be issued to the owner. Those were the days when DCA (or DoT, morphing into CASA) actually worked with the aviation community, instead of against it. -
So - since the website gives zero information on this: what is Pete's background and CV for aircraft design?
-
Don, every bit of that is true - and reasonable. BUT - it also implies a ready acceptance of risk by the operator contrary to warnings and sometimes explicit instructions to the contrary! - which most RAA-class aircraft operators do, all the time, quite normally and almost always without incident. You fly a rotax-912 powered aircraft. In the Rotax 912 Engine Operators Manual, General Instructions, para 1.4: 'WARNING!. Non-compliance can result in serious injuries or death! Never fly the aircraft equipped with this engine at locations, airspeeds, altitudes or other circumstances from which a successful no-power landing cannot be made, after sudden engine stoppage.' I'm in no way having a go at Rotax engines here - I think Jabs. have an entirely similar warning - and AFAIK, there is a basically similar regulatory requirement for any operation of our class of aircraft... which is routinely ignored, without problems, for probably hundreds of thousands of flights every year. If we all actually scrupulously followed the manufacturers / regulators instructions to the letter, I can think of several airfields routinely used within about 30 minutes drive of my place - Mittagong using the 24 strip, and Wedderburn - that almost no RAA aircraft should take-off from. ( Mind you, Mittagong has been used quite successfully, a number of times in the last several years, for Jabs. dead-sticking in as an unplanned adventure on their flight..) Then, there are people who really stretch the envelope - like the turkey who turned up at Camden about 12 months ago, kicked the tyres on a Jab. and (incompetently) did a fuel check - on an aircraft that had been sitting out on the airfield completely unused for many, many months, fired her up and headed straight out towards Bindook - over some of the lousiest tiger country you could possibly choose to be clawing for height above. Surprise - Jab. engines don't run on water... or on air alone, as in the Runcorn case. I suspect that Rotaxes also require a suitable air/fuel mixture to keep providing thrust. What I am trying to point out here, is that very many operators of our class of aircraft routinely place a reliance on the noise staying on, contrary to the advice of the noise-maker and the 'general' provisions of the regulations under which we fly. Realistically, if we all DID observe all of those, the opportunities for flying would be hugely limited - BUT, by NOT following to the letter the advice and either explicit or implicit requirements, we are taking a risk against which we have been warned. We hand-off maintaining a margin of safety to the reliability of the engine. And we hand-off that margin of safety to the engine for our convenience or pleasure. Nobody FORCES us to fly in dangerous circumstances (even if the regulations / noise restrictions / airspace restrictions / availability of better airfield sites etc. make it bloody difficult to avoid). Now, (pure - not motor-equipped) glider pilots do NOT have the luxury of handing-off the risk to the engine. As a basic rule (at least in my gliding days), if you are at 1,000 feet AGL and in no lift, you damn well start your landing (and I've clawed my way back up from less than 600 feet, and I reckon Ingo Renner could climb out on a cow-fart from 50 feet, but he is a god with a special, personal arrangement with gravity). Gliders have an l/d that provides a far greater choice of area for out- landing from any specific height than any RAA aircraft - but the principle is, and the laws of physics are the same for both. A glider has airbrakes - and they make a huge difference for what is a 'safe' outlanding field. So: in practical terms, you have a greater chance of finding a safe outlanding spot in a glider from ANYWHERE, at any height, than in an RAA-class aircraft. Very, very few glider accidents happen in out-landings. Again: what is my point? Well, it is this: if we choose to rely on the engine running to get from anywhere to anywhere else irrespective of the potential for a safe outlanding, when the said engine does not provide an explicit guarantee that it will continue to run - we are accepting a risk against which we have specifically been warned. RPT passengers step aboard an aircraft in the confident expectation that the seat they occupy will end up at the chosen destination. An awful lot of money goes into supporting that expectation. RAA operators/passengers step aboard an aircraft that flies under less-stringent requirements for reliability. The quid pro quo for that, is that we need to operate it with due respect for the difference. As a crude analogy: if you go to the observation deck of the Empire State Building and take the elevator back down, you have every right to expect to arrive at the ground intact. If you jump off the observation deck with a BASE jump chute and you end up as pavement pizza, you (or more accurately, your successors) probably have little claim against the chute manufacturers.
-
You know, I have by log unpowered landings numbering in triple figures - and I know people who have them numbering in FOUR figures. Some of them in paddocks far, far from home - possibly even in different States. I can't claim the 'different States' but I've ended up in paddocks completely unplanned. Been towed out, either behind another aircraft or on a trailer - and in EVERY case, the aircraft I had flown, flew the next day. My first solo fight, I took off under the power of an 1800CC, horizontally-opposed, four-cylinder aircooled four stroke petrol engine, and landed with that engine not running. AS REQUIRED by my Instructor. The next student fo it took off maybe ten minutes after I landed. The aircraft I flew were called 'gliders' (or, in the first solo case, a 'motorglider' or aerial barge, by some, me included). THE ENGINE - for fixed wing aircraft (helicopters are an affront to nature that need not be considered by sensible people) does NOT - except for the Harrier and the Osprey, I think - provide lift. ( OK, add some Northrop + DC Comics devices way back in the past..) THE ENGINE provides thrust, which when translated into airspeed over a lifting surface provides LIFT, which gets us up to where we can fall down again. AIRSPEED over a lifting surface - producing LIFT - is what allows us to remain in the air. Gliders don't have engines! - try to keep up with me here. Gliders utilise gravity - that force that sucks us all back to earth - in order to fly! Without being able to convert gravity into kinetic energy, gliders would be just odd-shaped balloons... Gliders fly, by falling rather slowly through the air and finding air that rises faster than they fall, to climb. And they are damn good at it: the world's distance record for gliders currently stands at 3,009 kms for around three turning points. Absolute altitude, 15,460 metres AMSL. Oh, and they have been proven to stay in the air for in excess of 56 hours. AND THEY ALL LAND WITHOUT ANY ENGINE POWER.
-
DooMaw - building a STOL
Oscar replied to Head in the clouds's topic in Aircraft Building and Design Discussion
I made the connection when I awoke early in the morning with a 'Eureka' moment, because it explained why Jabiru had gone from individual pedal stops to the torque-tube mounted ones: the stops only have to meet the 300 lb load case and by doing that, automatically meet the 200 lb load case... I'll bet HITC has had plenty of those 'look at the design, and see a better way' moments as he's gone along- because his design has so many elegant solutions in it. As an aside, the J160 and later rudder + nosewheel linkages mechanical design is SO much better than what's in my LSA55, it's really quite an excellent example of experience improving the breed ( though I dislike the rudder-centreing arrangement). -
DooMaw - building a STOL
Oscar replied to Head in the clouds's topic in Aircraft Building and Design Discussion
DJP - no longer confused, I worked it out, I had misinterpreted what I'd been told. ... HITC, sorry to hijack your thread there, but I guess it's the sort of thing you have to deal with every step along your way with the design, so it's not been completely irrelevant. -
DooMaw - building a STOL
Oscar replied to Head in the clouds's topic in Aircraft Building and Design Discussion
DJP - I am slightly confused. 23-397 says: §23.397 Limit control forces and torques. (a) In the control surface flight loading condition, the airloads on movable surfaces and the corresponding deflections need not exceed those that would result in flight from the application of any pilot force within the ranges specified in paragraph (b) of this section. In applying this criterion, the effects of control system boost and servo-mechanisms, and the effects of tabs must be considered. The automatic pilot effort must be used for design if it alone can produce higher control surface loads than the human pilot. (b) The limit pilot forces and torques are as follows: Control Maximum forces or torques for design weight, weight equal to or less than 5,000 pounds1 Minimum forces or torques2 Aileron: Stick 67 lbs 40 lbs. Wheel3 50 D in.-lbs4 40 D in.-lbs.4 Elevator: Stick 167 lbs 100 lbs. Wheel (symmetrical) 200 lbs 100 lbs. Wheel (unsymmetrical)5 100 lbs. Rudder 200 lbs 150 lbs. 29-399 says: §23.399 Dual control system. (a) Each dual control system must be designed to withstand the force of the pilots operating in opposition, using individual pilot forces not less than the greater of— (1) 0.75 times those obtained under §23.395; or (2) The minimum forces specified in §23.397(b). (b) Each dual control system must be designed to withstand the force of the pilots applied together, in the same direction, using individual pilot forces not less than 0.75 times those obtained under §23.395. So - what I think you are pointing out, is that for BOTH pilots stomping on the same pedal in a linked dual control system, the maximum force restraint has to be: 0.75 x 200 lbs x 2: 300 lbs applied to the linked pedals. Now, in the J160, the stops are on the leading (from the pilot's perspective) torque tube that connects the rh pedals, and acts against a reinforced area on the trailing (from the pilot's perspective) connecting torque tube. The rudder push-pull cable is attached to the pilot-side rh pedal upright. But, since either side pilot can be the one pushing the pedal, each individual pedal has to be able to withstand 200 lbs, surely? If I have got this straight, it would be only in a cable-joined pedal system, that the 0.75 reduction of cumulated effort would apply? In the LSA55 style pedal system, each pedal is individually stopped, so I think the 200 lb limit at each pedal, applies - yes?. -
DooMaw - building a STOL
Oscar replied to Head in the clouds's topic in Aircraft Building and Design Discussion
I do know that Dafydd Llewellyn and Alan Kerr differ on the necessity for stops at both ends of the Jabiru push-pull cables! - and both are very, very experienced and respected engineers. As is, of course, Bill Whitney. Between those three, you have a majority of ultra-lights ever designed and produced in reasonable numbers in Australia covered... add in Grahame (?) Swadling and you have just about the lot, other than the guy who did the Brumbies, I think. Both Dafydd and Alan worked extensively on all aspects of development of the Jabs. in the early days (up to the 160, at least) so a simple end-user like me can't separate the advice... I know Dafydd Llewellyn prefers accurate stops at both ends, I THINK Alan is content to have rudder pedal travel with positive stops for serious pedal-pushing but considers that fine adjustment can be taken out at the control surface end. I can see his point: all the components in the control circuit have a rated force in excess of 1200 lbs. However, since Dafydd will be doing the test flying of my aircraft, I'm not going to even think about trying to send him aloft ( and he probably wouldn't go, anyway..) unless he is happy with everything... and I don't think the rudder horn will happily accept anything like a serious force, though being a glass construction, it does have flexibility on its side. Possibly interesting story: When I came to fit the new rudder to the new fin, I found that it was a bad match. At the bottom, it was a good fit into the fin 'channel' -but at the top, it was about 6mm too narrow, resulting in a 6mm or so step from the t/e of the fin to the rudder on the starboard side. Aerodynamically, horrible. Took me a while to suss out why: Jabiru had simply extended the rudder spar moulding from the LSA rudder spar vertically, without taking into account the divergence due to the increased height of the fin. After consulting with Alan Kerr - who had done the structural justification work - I split the rudder spar and inserted a new web to bring the rudder into proper alignment. Having to work 'inside-out' was a challenge... And, the resultant weight change and moment had to be calculated to ensure that the possibility of flutter as a result was within the parameters of the original flight testing!. Jigs had to be built.... I suspect that a lot of people don't realise just how much thought and effort needs to go into making changes. You can't just decide that 'a bit more of X would be good' and take a hunk of aluminium and a handful of rivets and throw them onto the aircraft, because a different aircraft has that feature and it seems to work.... adding VG's without really, truly knowing how to get them to work effectively and safely, is probably one of those areas where some people get great results and some either get poor results or even make their aircraft dangerous. -
DooMaw - building a STOL
Oscar replied to Head in the clouds's topic in Aircraft Building and Design Discussion
As always, exemplary work, HITC. Anybody who underestimates how hard it is to get a complex welded structure NOT to be pulled out of whack by weld shrinkage, has never done any... I used to build space-frame sports cars (Clubman-class, like Lotus Super 7's on steroids) and if you didn't consider the weld-pull - and the tube attachment sequence - you could get really, really frustrated. Engine mounts are the same deal... and you have many dozens of such welds, and they all look perfect!. You have every right to have a small plaque made up quoting the Ozymandias dictum: 'Look upon MY works, ye mighty, and despair". Something discreet, of course, and placed unobtrusively in the cockpit. Those who don't understand instantly, won't ever. And, control stops at BOTH the input and control surface end, are 'proper practice'. I have to put the rudder pedal stops in to our Jab, having changed the entire fin and rudder for a J120/UL one from the old and broken LSA55 one, and consulting my friendly ex-CAR 35 engineer, was fairly horrified to learn that the FAA requirement is for 200 lbs force at the pedal for EACH pedal - so if both in the front seats have an 'Oh shit' moment and hit full rudder together, there's 400 lb force to be resisted from being fed into the control line / rod at the pedal - and therefore multiplied by whatever mechanical advantage there is from the pedal to the line / rod..