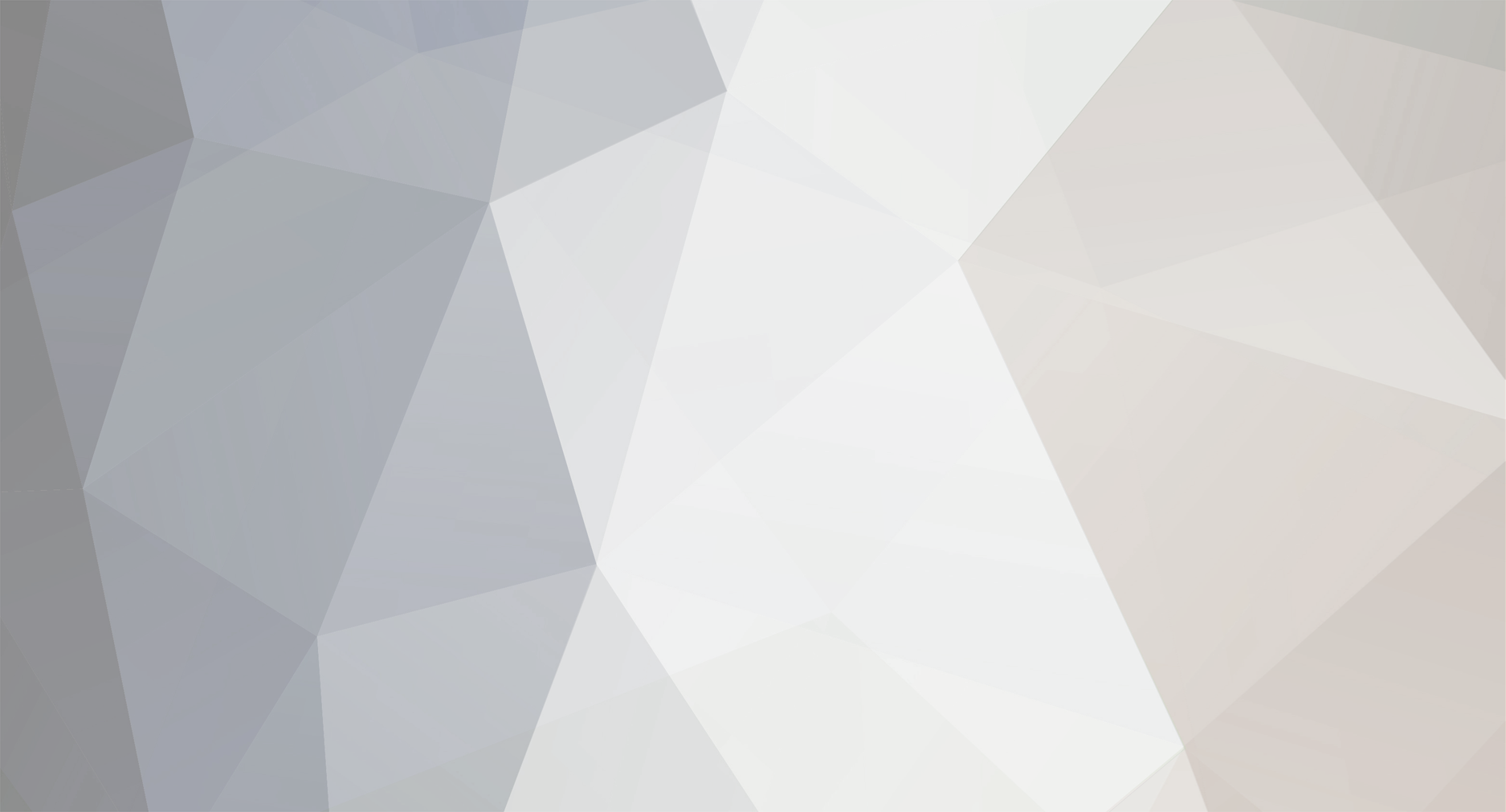
Oscar
Members-
Posts
2,485 -
Joined
-
Last visited
-
Days Won
67
Content Type
Profiles
Forums
Gallery
Downloads
Blogs
Events
Store
Aircraft
Resources
Tutorials
Articles
Classifieds
Movies
Books
Community Map
Quizzes
Videos Directory
Everything posted by Oscar
-
Which manufacturer?
-
This just sent from RAA: ( part note only:) Accident at Katoomba Airport 27 February 2016 RAAus is saddened to advise members of the death of Mr Rod Hay. Mr Hay died in an accident at Katoomba Airport on 27 February 2016 involving Jabiru 55-3692. The damage to nearby trees in conjunction with the extensive damage to the propeller and lack of visible external damage to the engine indicates the engine appeared to be operating at impact. To fully examine the engine, RAAus is conducting a supervised engine tear down with officials from ATSB and Jabiru. The control systems of the aircraft were all confirmed as connected to key points after impact and all damage is consistent with impact damage. At present our preliminary assessment of the evidence appears to support a possible loss of control with the cause as yet undetermined. RAAus will continue to work with authorities on the investigation and advise members again once we have more information. I think that this fairly timely and reasonably adequate initial report on a very sad and disturbing occurrence is a sign that RAA has recognised that Members have a genuine need for reasonable advice in the case of serious accidents. The quick respopnse after the Moruya accident was better information than we have had out of RAA for some years and the people in RAA involed are to be thanked, I believe, for this significant improvement in communications. It has also been a relief that this particular thread has not instantly degenerated into formula 'Jabiru' bashing posts and everybody has been respectful and reticent to assume a position on the initial report. It is - in my belief - a good step forward that ATSB is involved, so we may get the results of trained, expert accident investigation. RIP Rod Hay - the type of stalwart of the RAA movement.
- 98 replies
-
- 15
-
-
-
-
And excessive costs for main gear tyre replacement.
-
WOW: Superman. The official figure for a Piper Warrior Ground Roll is 595 feet: 181 meters. Of course, that is only what was achieved by a professional test pilot flying for certification purposes. Measuring from Google Earth, the Piano keys at Moorabbin are around 30 metres long. I am impressed that you can negate the rules of physics. Any of those Worriers still airworthy?
-
Nev: the Seeker is a bit 'squirmy' to land, for sure. But if you pull it back to the end of the elevator travel, it settles into a high-drag mush that is fairly reminiscent of a well-developed side-slip, without the sideslip components. You just hold everything on the back stop and play the throttle to achieve the aiming point.. and actually push the sick sightly forward to soften the flare.
-
With reference to HITC's marvelous post: do manufacturers ( or their agents) 'not 'Lie, but just BS a bit' - to quote Elwood Blues. A couple of years ago, one distributor of a particular aircraft that has sold some numbers here, had banner quotes on his site that listed the 'Stall speed' figure ( for the aircraft at 450 kgs. and the 'Cruise speed' (for the LSA version at 600 kgs). That 'Cruise Speed' was about 95% of VNE, and absolutely took NO reference to Australian gust conditions for Vra - and was, by owner report, about 20 knots over anything that was even remotely comfortable... The brochure is intended to make you buy. The POH is what you should fly to.
-
Don, the figures for KCAS are required for certification / certifying purposes, to be accurate and validated - and the flight testing has to be carried out by an approved pilot to a a specific regime. I believe that you can - normally - trust them. The POH figures will be for IAS: so they are what you fly to, off the instruments. However, there is (or should be) an IAS/KCAS error chart in the POH, so if working out e.g. adequate strip length for a hot-and-high-and heavy takeoff, you need to calculate from the KCAS figures and THEN convert them to the IAS corrected figures, for the ASI to actually tell you the correct information. HITC's enormously useful information should be digested by all: but there is one additional factor that has not been covered. That factor is, the actual elevator power available in the effect of wing downwash on the tailplane. That effect is not weight-dependent, but attitude-dependent. Speed makes a small difference to the impact of wing downwash on the elevator power, but in a flat, gentle approach stall, very little. ( In a dynamic stall - could be a VERY different reaction). If you read the information supplied by Dafydd Llewellyn ( http://www.recreationalflying.com/threads/do-vortex-generators-really-work.117300/ - post #6) you will find that 'stall-speed' is often limited not by the airflow separation speed/AoA, but by the elevator power available in the wing downwash at a specific speed/AoA. In other words, if the elevator power is reduced by the wing downwash, you may not get to the the ultimate lift potential of the wing ( and hence the lowest possible stall speed) because the elevator cannot drive the aircraft to the peak airflow separation point AoA. The Sunbird Seeker was required to be able to fly at marginally above the stall speed, held in a flat yaw of (I think) 25 degrees so the camera could be pointed at the powerlines. You can pull the Seeker back to just above the stall- using power to maintain height - and fly it around like a dodgem car: full rudder one way going to full rudder the other way- and it just bloody sits there and points itself at where you intended. I've done it. That handling result was the end product of several years of work with VG's in particular, to balance the aerodynamic interactions. FWIW, I think it was early last year that the chief FAA 'Light Aircraft' directorate test pilot flew the Seeker and stated that it had 'perhaps the best stall characteristics of any aircraft I have ever flown' - and recommended to the FAA that they contact Dafydd Llewellyn so they could understand the principles involved. That's a pretty convincing endorsement of Australian expertise, IMHO. And the point is: it is possible that the KCAS stall speed for your aircraft at the lower weight, is limited by elevator authority - NOT weight. The same elevator may have sufficient power ('authority') to pull the thing back to the same (or very slightly more) KCAS at higher weight for a very similar speed. In other words: you have an aircraft with a capabilty of achieving a KCAS at stall at 700 kgs, that could well do considerably better at a lower weight - but the elevator can't exert enough authority to exploit the lower weight, due to the downwash.
-
Billet is far more reliable in material spec. than cast; in fact, it was the extremely high rate of rejects from casting that steered Jabiru away from its first attempts at manufacturing (the 1600 engine). Cast and forged is reliabl;e - for a seriously volume manufacturer such as Lycontinental or even Rotax - but a small-volume manufacturer such as Jabiru has to balance the additional machining costs for billet manufacture against the waste costs of having to recycle defective castings. For a manufacturer that can order tonnes of product, it's easy to return material supplied that by test is defective without penalty. A 'small' player, is forced to compromise. Personally, I would not be at all prepared to scoff at the idea that this particular head had a material defect. It's the first one I have heard of with this type of failure, in what must have been around in excess of 7,000 heads produced. That's pretty small odds, but that's no relief to the poor owner who is sitting there with a broken engine. There are very probably decent 'spare' heads out there, sitting in sheds, that may be of help with refurbishment - I have some, but they are REALLY early models. For all its reputation on sites such as this, I have ALWAYS found Jabiru to be extremely helpful and informative if presented with a good explanation of the problem. They WILL go the extra yards to help you out.
-
Bruce: THIS - is what it takes to provide adequate airflow for cooling on the ground for prolonged running of a J2200 engine ( my engine in the piccy..) for certification test purposes It's fed by an around 6hp 3-phase electric motor running a very large centrifugal fan ( about 800 mm diameter), adding pressure to a 4-square foot approximately inlet tract for forced air from the prop. blast. Each head and barrel cooling duct, has an independently-controllable butterfly to keep individual pots balanced. The damn cooling set-up when running almost drowns out the engine... The centre outlet, as yet unplumbed, is for airflow specifically to the oil cooler. The two outer ducts as yet unplumbed are for the Jab 3300 engine. You can't see anything of the enormous supercharger than supplies air at ICAO-standard pressure for sea-level to the inlet tract, to keep mixture constant, run by another electric motor. Now, think about the inlets to your engine in a standard Jab. cowl...
-
Well, I do hope ATSB recognises the seminal work that Turbs has done....
-
Scotty, if all the AD's were done, were the through bolts replaced? I ask this because, if they were, with aged crankcase sealant it is very possible to get cracking of that when the tension on the through-bolts is released, which will lead to crankcase fretting. That does in NO WAY explain the cylinder head situation - and I'll agree that an inclusion in the material may well have been the cause. BUT I'd - if it were my engine - be doing a full teardown at this point. I also have an 'old' engine - though completely rebuilt and upgraded to CAE specs in most areas a couple of years ago, but only test run since then - so this is a very serious query and in no way a defence/excuse for Jabiru. I'd be most keen to know whatever you find.
-
Lots to digest there - but it's NOT the ' Reliability of Sport Aircraft Engines' research project that was supposed to be completed in October 2015. That is the one that is supposed to reveal the truth about the reliability of engines used in recreational and sport aircraft. One wonders why it is now four months overdue - in an investigation started in July 2013. Perhaps the reporting is not considered reliable? ( just a thought here, and perhaps they should have just asked Turbs in the first place and then would not have needed any further research....)
-
Which equates to 43.6 8-hour days of running. 6300 litres of fuel at 18/litres/hour ( conservative for a J3300 engine at those power settings.). About 7 years of operation for a private owner at average hours. A controlled environment that can be measured and reconciled back to 'standard' conditions from the measured results. Tear-downs and measurements. Put very, very simply: you cannot test an engine to either ASTM or FAR 33 / EASA standards, by building a frame, bolting the engine on and trundling that out the back of the shed and firing it up and providing the operators with a sandwich pack and a couple of cans of Coke. The only aero-engine manufactured in Australia that has been certificated is the Jabiru 2200C ( to JAR 22H - same as for the Rotax 912A.) That was managed by Alan Kerr as a contractor to Jabiru.
-
Link to the document?
-
Dafydd Llewellyn and I think George Markey spent years fighting Paul Middleton on just this issue, when spin training was removed from the Pilot Certificate requirements. I am not sure of the reasoning behind Middleton's antipathy to spin training, though it MAY have been that he believed spins to be some sort of terrifying bogeyman in the closet for recreational pilots. Once again, as many have mentioned, I think it is noteworthy that spin recovery training and continuing competency - and I mean PROPER spin recovery, not just incipient spin reaction training - is an accepted part of glider flying. When thermalling, glider pilots are working the thin edge of tight, slow turns in rough air and that moment when the stick pressure goes loose and the aircraft starts to drop the inside wing is so familiar that the response is ingrained in muscle memory. You don't even glance at the instruments, nor does the cardiac rate go up - at worst, you curse the slight loss of height incurred in the recovery.. Never having had that experience in powered aircraft, I can accept that the transition - which in gliders is quite gentle, really - can be very sudden, sharp and extreme. However, the certification / certifying standards for ultralights requires a 'civilised' standard of handling. Not all, by any measure, achieve this in all situations - and power-off with the reduction in airflow over the tailfeathers is a prime suspect in a number of otherwise relatively benign aircraft. People who are uncertain of their competence in spin / incipient spin recovery, would do well to look at any intended purchases with an eye to more than just its 'hot' looks.... For those who perhaps don't understand the 'loose stick /wing drop' reference, the best analogies I could offer are the feeling on the steering wheel of a car hitting black ice or a motorcycle hitting an oil slick hidden by a wet road surface, in poor light that hides the oil slick colours. Even with modern power steering that masks the effort needed to hold a car steering against the slip-angle, the transition to zero load on your hands is tangible ( and for motorcycle riders, you ABSOLUTELY know the front end is slipping away, because the damn bike is dropping into the corner like a stone. It is NOT a welcoming feeling).
-
Just had a look at the last image in the OP at 500%, and yes, it's pretty obvious that the two head bolts either side of the damage must have been under-tensioned ( for whatever reason) and the head has warped and lifted enough to allow the gases to escape. That greyed area, you can see what looks very much like flame scouring, and there is what looks like a trace of burnt oil in the very bottom of the flame-gouged track through the fins. Also, the burnt oil around several of the other head bolts suggest that most of the head bolts were not at correct tension. WHY that was so, deserves close attention.
-
Jonathan Aleck certainly signed it into force. Whether he actually wrote it, is less certain; it would be slightly surprising if someone of his expertise would thinkingly paint CASA into a corner from which it is, at the very least, going to have the devil of a time escaping without scorched hide.
-
It may well do - but the older information has been digitised but NOT databased. That means that a Google serach on specific search terms is the only possible interrogation, and since there was no controlled vocabulary, it's hit and miss as to the accuracy of any specific search by terms.
-
Then, it a massive inclusion of crap in the billet - and needs to be reported to RAA as a defect, so that all heads from that batch of material can be withdrawn.
-
Ok, several important issues here. Firstly, RAA systems have been archaic, in terms of modern IT-based information retrieval capability, for many, many years. The vast majority of RAA records-keeping has - until about three years ago - been paper-based. Secondly, there has not been any rigorous 'investigation' regime for incidents until very recently: at the very best, we have had summary conclusions for the cause of incidents derived by people in the field, almost all of whom have had no idea of (nor guidelines for) the information they should have been collecting and analysing. While I believe that the current Tech Manager has made very, very significant strides in this area, I also have reason to believe that investigation and analysis of incidents remains of patchy quality. Thirdly, RAA has very limited power in regard to taking 'corrective action' on technical matters. It has NO power in regard to ASTM ( LSA) certified aircraft technical issues and also no power in regard to Type Certificated aircraft technical issues. RAA has power in regard to Operations and the administration of Compliance with applicable standards. That is a fairly restricted window of opportunity for RAA to 'take corrective action'.
-
That is quite an old Jabiru head - thick fins. I can't see from the piccies whether it is the Mk.1 heads or the Mk. 2 heads. So that engine, with only 5 hours on it, has been sitting around since at least before about 2008, I think. It looks to me like mechanical damage from a broken push-rod; and I'd be looking at corrosion causing binding of either the lifter or the valve gear from growth of the rocker bushing causing the push-rod to break, thrash out the push-rod tube, and finally impact the head fins.
-
No, CASA is the one that has to explain that. It assembled raw data from various sources and compiled the spreadsheet. RAA vociferously ( check it on Google, Turbs) maintained that CASA had failed to analyse the data with which it was supplied competently - if at all. The Instrument - relying on the CASA spreadsheet for validity - was promulgated ( another long word with which you may have difficulty) before Skidmore came to office. And the reason, Turbs , that your 'data' has never been questioned, is that it is completely unreliable. Nobody takes it seriously enough to even challenge it. Sad for you, but true. And the FAA 'standard' is NOT a 'standard': it is a guideline for calculation from reports, the actual likely incidence of incidents (note spelling). It has precisely NO imprimatur for 'action' under ICAO rules. Do try to keep up with reality here, Turbs.
-
Don't forget the prescriptive nature of authoritative actions and the safety of kindergartens. And the experience of Speedway Victoria.
-
That 'last minute data' was DEMANDED by CASA. And you do not know the specifics of the demand. So don't try to deflect blame onto RAA for supplying information that they were required to supply. The RAA Board Member I referred to, has vastly more expertise than you in the technical administration of Sports Aviation, and frankly I can't be ar$ed to explain all of that to you. You and your spurious reasoning, don't matter.
-
So: by the ATSB figures, correlated to the FAA benchmark, AT LEAST ALL Rotax, motor-vehicle converted engines (VW, Subaru, Suzuki etc.) should have been simultaneously subjected to the the same restrictions - in the name of safety. Probably even some Lycoming and Continental models.. Would you care to enlighten us, oh Delphic Oracle, as to why this did not happen? I, for one, will be fascinated to hear your reasoning.