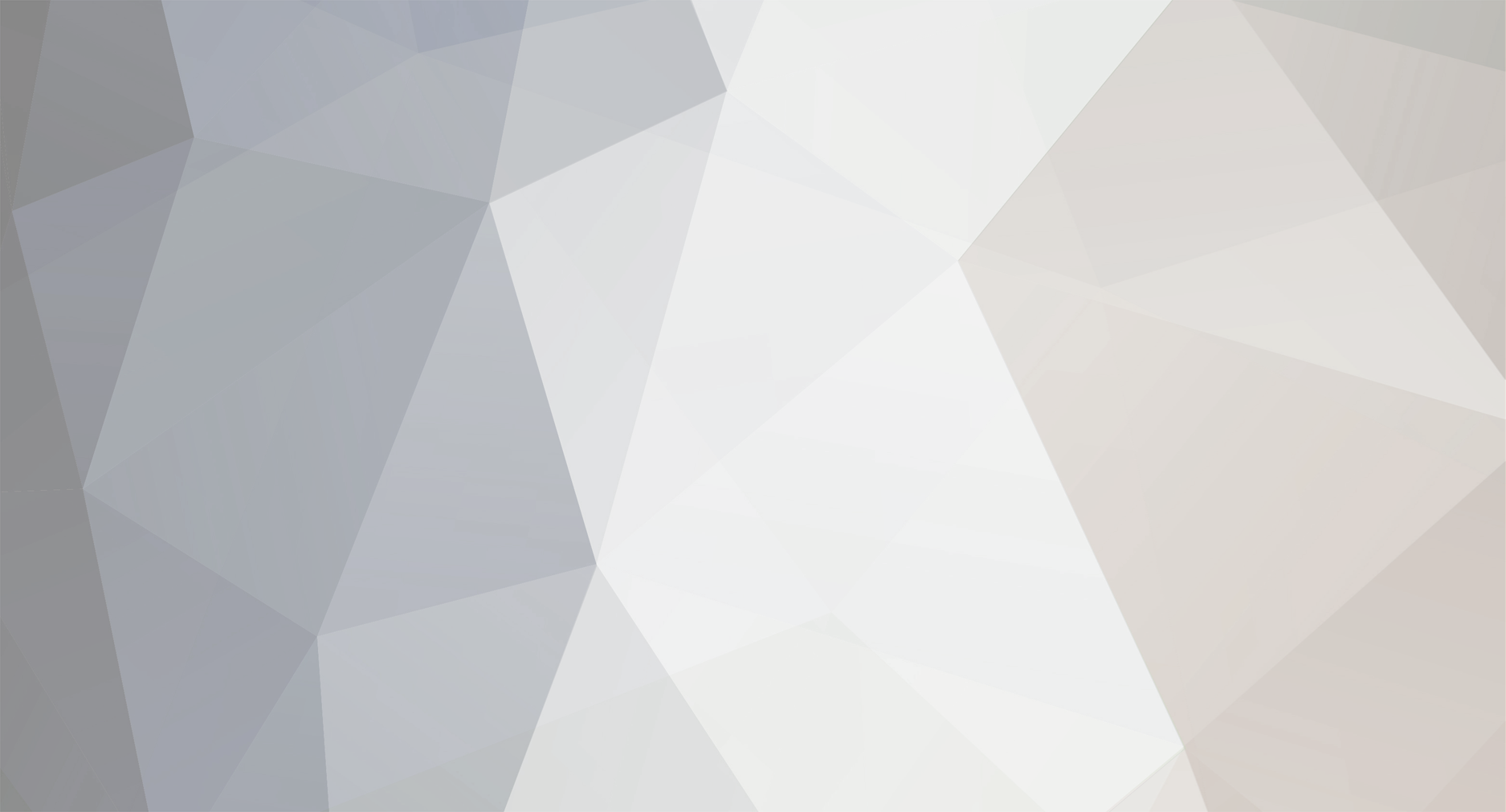
Wilfred
Members-
Posts
332 -
Joined
-
Last visited
-
Days Won
1
Content Type
Profiles
Forums
Gallery
Downloads
Blogs
Events
Store
Aircraft
Resources
Tutorials
Articles
Classifieds
Movies
Books
Community Map
Quizzes
Videos Directory
Everything posted by Wilfred
-
must be the dogs Pilot, Dog OK After Aerocomp Ditches Near Merritt Island Tue, 26 Dec '06 Newly-Built Plane's Engine Quit Near Airport A pilot completing one of the final test flights of his newly-built Aerocomp 7SL turboprop wound up going for a swim last week, after the plane suffered an engine failure near the Merritt Island (FL) Airport. "I was over the houses on the other side of Sykes Creek, so I put the airplane into glide and tried to slow it as much as I could," pilot William Lara told Florida Today. Lara built the plane (file photo of type, above) at the airport. The Montana emergency medicine physician was in town to finish his required flight training when the incident occurred December 21. When the engine quit, Lara said he kept the wings level and placed his dachshund, Sara, behind the front passenger seat to protect the dog from impact forces. He also wedged the door open. About 20 seconds after the engine quit, Lara says the plane touched down in Newfound Harbor at around 65 mph. He compared the experience to "getting hit with a 70 mile-per-hour baseball bat." With Sara around his neck, Lara says he swam about 150 yards before a nearby boater came to their rescue. Lara credited the plane's four-point seat restraints for keeping in him place during the rough water landing. "Had I been knocked out, I would have drowned. Everybody should wear seat beats. They're lifesavers," he said. Lara was treated at the scene for neck strain, and two cuts on his legs. Sara is doing fine.
-
A video of a Cri Cri http://cedarriversalmon.blogspot.com/2006/12/worlds-smallest-twin-engine-aircraft.html
-
Its cool as pointed out before it dont matter Aoccdrnig to rscheearch at an Elingsh uinervtisy, it deosn't mttaer in waht oredr the ltteers in a wrod are, olny taht the frist and lsat ltteres are at the rghit pcleas. The rset can be a toatl mses and you can sitll raed it wouthit a porbelm. Tihs is bcuseae we do not raed ervey lteter by ilstef, but the wrod as a wlohe.
-
You are invited to the Kempsey New Year Fly-In and Open Day over the weekend of December 30, 31 and January 1. Kempsey is on the north coast of NSW and this event is being organised by the Kempsey Flying Club with the full backing and support of the Kempsey Shire Council. This event is a replacement for the "Great Eastern Fly-In" which is normally held at Evans Head over the same period. A fact sheet with full details is available at the link below: http://www.aeroclub.com.au/showev-997-cccead.html All the best for Christmas and the New Year!
-
Article: Wake induced roll A recent Network story facetiously warned pilots to <STRONG title=http://www.aero-news.net/news/commair.cfm?ContentBlockID=635a2db5-f38b-4939-bd97-921900a15583&Dynamic=1>"beware the wrath of Dreamlifter"[/b].In one of the superfreighter's recent headline-making events, a Cessna 172 encountered the Boeing's wake turbulence, "rolled almost instantly to a 90 degree right bank, and descended in a nearly straight nose down attitude. The flight instructor took control of the aircraft, and was able to complete a recovery approximately 150 feet above the... water..." Wake-induced roll The usual hazard of encountering wake turbulence is induced rolling moments exceeding the roll-control authority of the aircraft. According to the FAA, the capability of an aircraft to counteract wake-induced roll "primarily depends on the wingspan and counter-control responsiveness of the encountering aircraft." If the airplane caught up in another's wake has a wingspan greater than the diameter of the wake rotation, then the encountering airplane will usually be able to ride out the wake without loss of control. This is primarily why an MD-80 crew, for instance, doesn't worry too much about wake turbulence from a Cessna Citation, while the pilot of a Piper Archer behind that Cessna needs to work to avoid what for him/her may be an unrecoverable wake-induced roll. Sayeth the FAA: "It is more difficult for aircraft with short wingspan (relative to the generating aircraft) to counter the imposed roll induced by vortex flow. Pilots of short span aircraft, even of the high performance type, must be especially alert to vortex encounters." Really unusual attitudes Attempting to recover from wake-induced roll with opposite bank input (the natural impulse) may overstress the airplane and lead to disaster. Beyond 70 degrees of bank or so, or with a very fast rate of roll, it may be safer to recover by deflecting controls in the direction of the roll, and rolling all the way around to an upright position. This is where training really pays off. I took an unusual attitudes and emergencies course several years ago at Delta Aviation in Stillwater, OK. After an introduction to maneuvers including rolls (in an aerobatic-certified Decathalon, and wearing parachutes as required by regulation), instructor Fred de Lacerta presented in-flight simulations of wake-induced roll and showed how a simple aileron roll, going with the flow, allowed a pullout with very little g-loading. It's becoming quite common for corporate flight departments and ab initio commercial pilot training programs to include "emergency aerobatics" courses in their syllabi. Consider investing in emergency aerobatics course to add tricks like wake-turbulence escape to repertoire.
-
Probable Cause No Pulling Over By Brian M. Jacobson About the Author ... Brian M. Jacobson is a corporate pilot and aircraft owner who lives in White Lake, Mich This article originally appeared in IFR Refresher, Oct. 2005 Probable Cause Many years ago a friend of mine who owned a Chevy Nova wanted to know exactly how far he could go on a tank of gas. So he put a five-gallon can of gas in the trunk and drove until the tank ran dry. I happened to be riding with him to a Civil Air Patrol meeting when the engine sputtered and died. We pulled over to the side of the road, poured the five gallons into the gas tank and continued on our way. I don't remember how many miles my friend said he got from that full tank of gas, but the accident we're going to discuss reminded me of his experiment. How many times have you driven with the fuel gauge hovering on "empty" and have passed a gas station for one reason or another? I would say that most of us are guilty of this at least once or twice. If we run out of gas, we simply pull off to the side of the road like my friend did. It might be an inconvenience because most of us don't carry five-gallon cans of gas in the back of the car, but it would be unusual for someone to get hurt or killed just because they ran out of gas. The ramifications of running the tanks dry in an airplane are far more serious and our flight instructors tell us this from the first day we set foot into a cockpit. Most of us heed that lesson but there are always some who don't. None of us can afford to pass up an airport where fuel is available because we think we can make it to our destination. If we don't know for sure that we have the fuel on board to get where we want to go then we are bound by good judgment and common sense to make a fuel stop and get some more, even if it means we will be late for Cousin George's third wedding. The pilot of a Beech B60 Duke apparently thought he had enough fuel to make it to his destination, but he miscalculated by about 13.5 miles. The pilot had departed Houston's Hobby Airport (KHOU) on an IFR flight to Dekalb-Peachtree Airport (KPDK) in Atlanta but he would never make it. Three hours and 13 minutes later the airplane crashed half a mile short of the runway at Fulton County Airport (KFTY), an impromptu alternate and just 13 miles from KPDK. The pilot, who was the only person on board the aircraft, was killed. It would seem that this is an open and shut case of fuel exhaustion, and it is. Even so, there is more to the story, facts that can't help but raise questions about the pilot's attitude towards fuel planning and safety. A Known Problem The story begins nearly three weeks earlier, on a day late in July, when the pilot flew his Duke to Houston from Atlanta. Upon landing at Hobby Airport, he experienced a complete loss of engine power. He told the line service supervisor that he had flown approximately 100 miles with one engine feathered and that the second engine quit when the aircraft was on the ground. However, he was able to get both engines restarted and taxied in to the ramp. He told the supervisor to put 40 gallons of avgas in the aircraft's tanks, 20 gallons per side, and the engines apparently ran normal after that. Twelve days later the aircraft returned to KHOU, but this time the pilot turned the airplane over to a maintenance shop on the field with the complaint that both engines quit at one time or another when the throttles were brought back to the idle position. A mechanic ran the engines the next day and verified the complaint. He suggested to his supervisor that both fuel servos should be sent out to a repair station for evaluation. The units were removed from the aircraft and sent out to a local facility. When they were returned, the facility said that nothing could be found wrong with them, although the right one ran rich at low speeds. The facility spent part of several days making adjustments to the engines' fuel systems. In the meantime, the shop supervisor contacted the pilot and asked him if the problem had occurred only when the weather was extremely warm. The pilot indicated that that was the case and that it had occurred once with each engine. The shop supervisor then asked the pilot if he had the fuel boost pumps on when this occurred. This time, the pilot wasn't sure and acknowledged that he may not have turned them on. The Duke is powered by two Lycoming TIO-541-E1C4 engines that produce 380 horsepower each. This is a high-performance, turbocharged, fuel-injected powerplant that requires skill and knowledge to operate. The Duke's flight manual states that the boost pumps should be turned on for takeoff and landing and that they should also be on in cruise when needed to prevent fuel flow fluctuations. The shop supervisor felt the problem occurred because the boost pumps were not turned on, allowing the heat inside the cowlings to vaporize the fuel in the lines and creating a vapor lock. That would cause the engines to run poorly on the ground and possibly to quit when the throttles were retarded. He did some additional research and was told that, to be safe, he should be certain that the fuel systems were properly adjusted. The following Friday the pilot called the shop and told them to button up the airplane because he had to fly back to Atlanta. The supervisor explained to the pilot that they were not yet finished with the work: The right engine setup was complete, but the left engine needed to be matched to the right. The pilot said he needed the airplane, but that he would return in a week and that they could finish the work at that time. This put the supervisor in a tough spot. While he felt the airplane was safe to fly, he couldn't return the aircraft to service because the work was not yet complete. That apparently didn't faze the pilot, who agreed to take the airplane even though there was no sign-off in the logbooks. The aircraft was towed out of the hangar and line service personnel topped off the plane with fuel. Need Some Help At 5:50 p.m. Central Time, the pilot picked up his IFR clearance to KPDK and was airborne by 6:31 p.m. A little less than three hours later, the pilot, who was now talking to Columbus (Ga.) Approach, reported that he was getting low on fuel and requested a direct clearance to KPDK. The controller asked if he was declaring an emergency but the pilot said no. The controller then switched the aircraft to Atlanta Approach Control. Upon initiating contact with Atlanta Approach, the controller verified the aircraft's low fuel state and asked how much fuel the pilot had. He responded that he had about 30 minutes remaining. Although there were no delays going into KPDK, the controller suggested that the pilot land at another airport and offered to help him find a suitable alternate. The pilot agreed and asked for an airport with more than 6,000 feet of runway. The controller suggested Fulton County Airport, which was 45 miles and about 15 minutes from the Duke's position. He told the pilot that the airport had a control tower and a runway that was 5,796 feet in length. The pilot advised that the runway length was fine and requested a change of destination to the Fulton County airport. The controller also advised the Duke pilot that KFTY was 13 miles from Peachtree and that he could always re-evaluate the situation once he got closer to Fulton County as to whether he would land at Fulton or continue on to Peachtree. But the Duke pilot told the controller that he would land at Fulton County, perhaps an indication that the pilot realized that his fuel state was reaching a critical status. At 10:39 p.m. local time, the pilot told the controller that he had the airport in sight. The controller cleared the aircraft for a visual approach to Runway 8 and instructed him to contact Fulton County Tower. Just before making the switch, though, the pilot reported to the approach controller that he was having "some problem with the engine" and requested a straight-in approach, which the controller approved. When the pilot made his initial call to the Fulton County tower, he advised that, "We are probably going to need some help off the runway." One minute later he told the controller that he had lost both engines and that he didn't think he could make the runway. That was the last transmission from the pilot. Know The Limits The aircraft came to rest on a grassy island between the parking lot of a commercial business and a public service road in an industrial park. An FAA inspector was at the site of the accident approximately 45 minutes after it occurred. Although both fuel tanks were ruptured, the inspector found no sign or smell of fuel at the accident site. The only fuel retrieved was about three ounces from the plane's fuel system. A subsequent investigation of the engines and fuel system failed to reveal any contributing mechanical problems. The weather at the time of the accident was VFR with calm winds. The 40-year-old Duke pilot held a private pilot certificate with single-engine, multi-engine and instrument ratings. The NTSB report stated that the pilot's total time was approximately 1,800 hours, but an FAA inspector's report put his total time at 1,282 hours, 26 hours in type, and 30 hours of flight in the preceding 30 days. He had a current medical certificate and biennial review. The inspector's report also indicated that the pilot had taken recurrent training during the last three years, but there was no information about how long he had been flying the Duke. The fact that the pilot ran out of fuel on the westbound leg to Houston on one trip, and then had the problem with the engines not idling on another, seems to me to be unrelated. As the mechanic suggested, the hot July and August weather probably played a part in the idling problem. Coupled with the pilot's apparent lack of knowledge of the airplane's systems, his not turning on the boost pumps before landing probably contributed to the incident. Lycoming turbocharged engines run hot. When there is little cooling air inside the cowlings, like there would be after touchdown on a hot day, the boost pumps force cooler fuel from the airplane's tanks into the engines. If the pumps are not turned on the fuel in the lines under the cowling will vaporize before reaching the engines causing them to sputter and quit. The question is, why would the pilot attempt the same flight, albeit going eastbound, when he  from what we can tell  ran out of fuel the first time? Most pilots who have that experience will not have it a second time, because they will insure that the amount of fuel on board is sufficient at all times. Another question is whether or not the engines were being properly operated. The Duke has an advertised range of 1,010 NM so the flight from KHOU to KPDK  a direct-line distance of 615 NM  is well within the plane's capabilities. But to achieve that requires careful power/ fuel management and monitoring. Failure to do so can cause excessive fuel consumption resulting in a considerable reduction in range. We'll probably never learn the answer to those questions, but we can still learn a few lessons from this accident: If you don't know how many hours you can fly your airplane to dry tanks, then you need to find out. That doesn't mean you will do what my friend did with his Chevy Nova. Instead, over the next two or three short trips, figure out what the overall fuel burn per hour is for the aircraft and divide it by the number of gallons you have on board. That will give you a good idea of how long you can stay in the air. On longer flights the fuel burn should improve, but the difference between the short trip figures and the long trip figures will give you a little extra time aloft beyond your planning times in case of an emergency. However, you should never allow the fuel levels to get so low that you need to depend on that difference. If the airplane is new to you and you don't have enough experience with it to know exactly what the fuel burn is, be very conservative when flight planning. Each time you fill up the tanks you will have more fuel burn information that will help you with your future trip planning. >Determine how many hours you are willing to stay aloft in IFR conditions and VFR conditions and never exceed those times. If it becomes obvious after takeoff that a flight will take you beyond your maximum allowable flight time, find an airport, land and get some more fuel If you plan your flights so tight that you are on the ragged edge of making it to the airport, what are you going to do if you are told to hold at the destination because there is an airplane stuck on the runway or the landing gear doesn't come down and you need time to troubleshoot the problem? You need fuel on board to give you the time to do these things. Don't press your luck. An extra fuel stop may take some time, but it is better than winding up half a mile short of the runway being carried away on a stretcher
-
MyTraffic X Enhance Your Flight Simulator X Traffic This first add-on for Microsoft Flight Simulator X from Aerosoft creates realistic in-flight and aircraft ground traffic using the exact aircraft and airlines including the customized radio communications on the airports. Worldwide dynamic and realistic AI-Traffic! MyTraffic X generates more than 475,000 daily flights at 7,800 airports worldwide and adds them to your Flight Simulator X skies. From general aviation, regional jets, military aircraft, freight services, right up to the intercontinental airliners, My TrafficX brings FSX to life! The AI traffic corresponds to the real life air traffic throughout the world. Take-offs and landings take place with the correct aircraft types and airlines on each airport. ATC will address the aircraft with their correct call signs. Many intercontinental flights are taken from the published schedules of the airlines. MyTraffic X also supports the new features in Flight Simulator X such as the jetways, which dock on to the aircraft, ground vehicles, baggage carts, etc. A total of 154 aircraft types in more than 3,000 liveries are available for the AI traffic display! From a simple single engine aircraft to the Heavies. No more fantasy airlines in Flight Simulator! Regional Airliner, such as EMB145, Yak40, DHC8. Fokker50... Medium range, such as B727, B737, Airbus A321, MD-80, Il62... Heavies, such as MD-11, B747-400, B777-300, IL-86... Cargo, such as AN12, AN 124 and C5 Galaxy The DVD also includes an updated version 4.1 of MyTraffic 2006 for FS 2004 so you get double the bang for your buck!</LI>
-
<TABLE =contentpane> <T> <TR> <TD =contenting width="100%">Leisure Flight Proposes Draft Regulation </TD> <TD =ing align=right width="100%"></TD> <TD =ing align=right width="100%"></TD> <TD =ing align=right width="100%"></TD></TR></T></TABLE> <TABLE =contentpane> <T> <TR> <TD vAlign=top colSpan=2>At a follow up meeting between CASA and industry on 30 November 2006, Leisure Flight Australia proposed a draft regulation for self administration of private GA. A follow up meeting to the October industry/CASA “summit†was held in Canberra on 30 November 2006. Among others, CASA made a presentation on how industry should structure a safety case to satisfy CASA and the Minister that self administration could deliver a safety outcome at least equal to that under CASA administration. The Board of Leisure Flight wanted to increase the momentum, so decided to draft a regulation for discussion purposes to present at the meeting. This proposal was presented by Peter Bennett, and was followed up by an interlocking presentation by Trevor Merton on behalf of the Warbirds Association. The concept was well received. As a result, CASA has asked us to create an industry team to develop the regulation. They will contribute as necessary, but want industry to lead the push. This is exactly what we want too. At last we have the opportunity to make rapid progress. Eventually the presentations from the meeting will be posted on the CASA website. In the meantime you can download the LFA presentation here and the Draft Regulation here. Please read and send your comments to Peter Bennett for consideration as the regulation is fleshed out and refined. If you or your organisation has relevant expertise and are not yet a member of LFA, please join now and help us in this important process.</TD></TR></T></TABLE>
-
http://www.auf.asn.au/cagit_trophy/cagi.html This should be a planning consideration for Xmas Trips
-
USB Missile Launcher Reviewed (Verdict: Nobody's Getting Any Work Done) How fun are these USB Missile Launchers? Very. A single launcher comes with 3 foam missiles, a three foot USB cable, sound effects, and a Windows XP control program. Once installed, you control the cannon with either your mouse or the arrow keys, and fire with the space bar. We kinda wish they came with more missiles, since three is just going to get you maybe a minute and a half worth of pleasure. Nobody likes it when you've shot everything off after 90 seconds. But at $35, they're not too expensive. Buy a few and watch your productivity soar. Does soar mean go down? turtle
-
Heated USB Slippers Go 'Dual Core' Heated USB Slippers Go 'Dual Core' Technology marches on, and now even heated USB slippers have gone "dual core." Thanko now gives you an individual control for each foot with its latest USB Warmer Slippers ($33) with a two-step temperature control switch for each slipper, letting you crank up the heat on one foot while leaving your other foot lukewarm. USB heated slippers have come a long way since their inception way back in 2005, and now there are advanced models that cover your ankles, and even have a very special bear attachment. Even so, never were they as technologically advanced as this. But jeez, who wants to be tethered to a PC like this? It must feel like a ball and chain.
-
Morphis ESP Motion Simulator: $300K and You're There Now you and your seven closest friends can tuck yourselves into the Morphis motion simulator, giving you an aviation-quality sim experience that's sure to elicit a variety of responses from ecstasy to nausea. It's equpped with a high-rez 3D visual system and ass-kickin' audio to give you that thrill ride eperience in your own home. This is the same company that's been making thrill rides and flight simulators since 1998, and now they're offering it for common folk such as you and me. We were all set to order one for our home office until, uh-oh, we saw the $300K price tag. – Charlie White
-
Technical Analysis: Microlight Structural Analysis http://www.atsb.gov.au/publications/investigation_reports/2006/AAIR/aair200601173.aspx ATSB Aviation Safety Investigation Brief 200601173 report on the technical analysis investigation into the Microlight Structural Analysis of Airborne Edge microlight aircraft registrations 32-4456 and 32-4388. turtle
-
Enhanced Aviation Radio System The E.A.R.S.2 (Enhanced Aviation Radio System) is a standalone system to connect a cell phone to your headset. In three steps the system is set up: Plug headset to E.A.R.S.2. Plug E.A.R.S.2 into radio or intercom system. Connect E.A.R.S.2 cell phone cable into headset jack The system then allows you to talk and listen on your cell phone through your headset, which is great for filing and closing flight plans, contacting ATC/FSS or any other location. In the event of an avionics failure, you can still talk right through your headset with your cell phone or a handheld radio E.A.R.S.2 will not interfere with radio transmissions (using an interrupt system). The unit works independently so no need to worry about passengers listening to your calls. Passengers can even use an MP3 player to listen to music without you having to. The unit uses one 9-volt battery to amplify the cell phone volume through your headset. The unit will automatically go into "stand-by" mode until making or receiving a call. Battery life is approximately 18 months in stand-by and 25 hours of talk time. The E.A.R.S.2 sells for about $100
-
Remos G-3 Light Sport Aircraft The Remos G-3 aircraft was designed eight years ago but only recently began selling under the new light sport aircraft rules in the United States. The aircraft has side-by-side seating for two, a high wing, tricycle landing gear, folding wings, and carbon fiber and composite construction. Capitalizing on a cockpit width of 46.8" (an increase of more than five inches over the Beech 58 Baron), German engineers developed a wrap-around windshield and blister side windows that offer great visibility. Cockpit size and insulation, along with a useful load of 704 lbs., permit big and tall pilots to sit comfortably in well-padded seats, allowing for extended cross-country flying without the normal levels of fatigue. A stainless-steel exhaust and after-muffler were engineered to exceed rigid European noise standards. The folding wings reduce the size of the Remos, allowing for home storage or "tucking" into the corners of most existing hangars already housing a resident aircraft. Elevator and rudder locations assure quick response to any changes in power settings. Entry and egress are easy through large cockpit doors that seal tightly when closed. Instrument panels can be configured for basic VFR up through advanced IFR systems. Power for the G-3 is provided by a certified Rotax 912S, 100-hp, four-cylinder, four-stroke engine. High-performance hydraulic disc brakes are a departure from the typical cluster braking mechanisms found in most LSAs. At gross weight, 1320 lbs, the manufacturer reports the G-3 will take off in 330 ft, climb at 1100 fpm, cruise at 120 mph, and stall at 45 clean or 38 with full flaps. It has a glide ratio of 1:17 and a range over 500 miles with 5 gph fuel burn. For more information visit the Remos Web site.
-
Ì understand that without a valid PPL oraccompanied by aGA instructor you cannot fly through controlled airspace. (being accompanied by a PPL does not meet this unless the PPLis PIC. If you have a microair transponder in the JAB i have found that with some brands of mobile phones the altitude can be up to 400 feet out. I I dont know what effect there is on the position. The flightcell works well and i guess on a lenghthy trip you could briefly turn the phone on to check calls then turn it off . Check your phone and see if it effects the transponder. The next g ones seem to be the worst as well as the motorola cdma's. others on the forum may be more able to qualified to comment on these issues.
-
Just Flight announces the release of the Schweizer 300CBi Just Flight have announced the release of their first ever helicopter simulation add-on. A small helicopter but a great simulation! One of the most popular General Aviation utility and training helicopters in the World is now available for FSX and FS2004. The S300CBi is modelled in extreme high-quality detail based on extensive research on the real-world aircraft. The aircraft is supplied with a set of unique tools to customise and enhance your rotary flying experience.
-
http://www.rtx-av-engines.ca/PDF/techinfofuel.pdf Some interesting articles http://www.ultralightnews.com/features/fuelrec.html http://www.faa.gov/aircraft/safety/alerts/saib/media/CE-07-06.pdf http://www.sportpilot.org/magazine/feature/2006%20-%2006%20June%20-%20Power%20On.pdf http://www.deh.gov.au/atmosphere/fuelquality/publications/review-non-automotive/operability-4.html http://www.nak.no/mikro/html/Teknisk/Etanol_rotax.html http://www.rtx-av-engines.ca/PDF/techinfofuel.pdf http://www.avweb.com/avwebflash/12_30b/briefs/rotax_v6_192786-1.html
-
Heck Airfield Based Ultralight Nose-Dives into Paddock - Pilot Sustains Minor Injuries November252006 Police and Emergency Services were called to an aircraft crash at Jacobs Well in SE QLD after a ultralight nose-dived into a cane paddock The aircraft had just taken off from nearby Heck Airfield - a popular sport and recreational aerodrome - when the mishap occurred - the pilot received only minor injuries and was taken to hospital for treatment Up until a few years ago the Heck Airfield was a small and almost insignificant airport supported only by a handful of recreational and home-builder pilots Recent upgrades and lengthening of the main runway have turned this once sleepy cane paddock on the edge of Moreton Bay into a thriving busy and progressive airport
-
The Hummel Bird: Here am I sitting in a tin can Futurists in the mid-twentieth century loved to dream up worlds filled with incredibly convenient personal aircraft. If that vision had come to pass, I suspect vehicles like the Hummel Bird would have been manufactured by the millions. This tiny 13 1/2 foot long aluminum homebuilt aircraft is often powered by a modified VW bug engine (once plentiful, inexpensive and conveniently air-cooled). With a 37 hp engine the aircraft cruises at slightly more than 100 mph (161 kph). It requires only 300 ft (92 m) for takeoff and weighs a mere 300 lbs (136 kg) empty. There's only room for a reasonably slim pilot in the compact cockpit. Morry Hummel worked in the Curtis Wright experimental department during WWII. He learned to fly after the war and his first design was based on the Windwagon by Gary Watson. Hummel purchased a set of plans in 1979 and set about modifying it as a taildragger with larger bulkheads and a full canopy. The aircraft was completed in 1982 and dubbed the "Hummel Bird" in a Sport Aviation article. The name stuck. In 1999, four years after a serious aircraft accident, 84 year-old Hummel set about designing the Ultra Cruiser - an all metal ultralight aircraft. It first flew in 2000. Plans and parts for the Hummel Bird are available from the Hummel Aviation website, along with parts and kits for his popular Ultra Cruiser. I can only hope that I have such a productive retirement! http://hummelbird.com - The official Hummel Aviation site The images are of Dave King's aircraft [Holobrook Ultralight Club, Australia]
-
AirScooter II Ultralight Helicopter This 65 HP Ultralight Helicopter demonstrates that personal helicopters in the back yard parked beside the family car may not be a far fetched concept. If you can’t wait to get your hands on the real one, you can always buy the model version for now. “Going back to the future of rotor craft design is the basic concept of the AirScooter VTOL (Vertical Take Off and Landing) vehicle by AirScooter Corporation of Henderson, Nevada. “The original Sikorsky rotorcraft helicopter concept was based on a coaxial design much like the AirScooter,†says Woody Norris; internationally recognized inventor and AirScooter Corporation co-founder, “what we’ve done is package the coaxial design in a modern light-weight craft that allows for intuitive control and incredible maneuverability.†By eliminating the need and complexity of swashplates, collective and cyclic control through a coaxial rotor design a number of benefits beyond conventional helicopter designs are immediately realized. First; enhanced, intuitive flight controls are achieved by simple motorcycle-style handlebars and the absence of a tail rotor. To gain altitude, simply throttle up like you would on a motorcycle, turn left or right on the handlebars for craft rotation and move the handlebar assembly as a joystick for directional control (including reverse). No pedal controls are necessary, which means someone without the use of their legs can just as easily fly the AirScooter. Handlebar controls represent the most distinguishable feature of the AirScooter. AirScooter’s patented design also provides an amazing level of stability whilein the air and during flight.â€Â
-
A good pilot is always learning -- how many times have you heard this old standard throughout your flying career? There is no truer statement in all of flying (well, with the possible exception of "there are no old, bold pilots.") I've owned two airplanes -- a Cessna 120 (for about seven years) and co-ownership of a Beech Sierra (for six weeks -- a story for another day).Obviously there were many differences between the two. One difference was the ability to preflight the engine. The Cessna's cowling was held with two sturdy latches on each side. Simply twist two key-type latches and the entire cowling half swung up and over the top, exposing the entire engine for preflight inspection. I can't tell you how many times I pulled small bird nests from the engine, dry straw that could block cooling air flow and cause an engine overheat, and in a worse-case scenario catch fire in flight and bring down the airplane. There were also cold winter days, during the time I was forced to store the Cessna outdoors, when I scooped handfuls of snow from the aft engine compartment, snow that would have blocked air flow before engine heat melted it off, and possibly entered the carburetor, strangling the engine. By contrast the Sierra's cowling was similar to most lightplane designs. There is a small door to reach the oil dipstick and oil filler, but for streamlining and engine cooling the cowl itself is firmly sealed, requiring significant effort to open up the engine compartment for inspection. For the short time I had possession I had to store the Sierra outside as well. During one preflight inspection I could not see any birds-nest material looking through either the oil door or the nose inlets. As I walked around the airplane, however, I saw a small bird fly from the outlet underneath the rear cowling. Laying down on the ground and looking up through the underside of the engine I found a huge mass of straw and twigs-a bird's nest-that had been "installed" overnight. After pulling the cowling and completely cleaning out the hazard I vowed to make plugs to close off all cowling openings when the airplane is stored. I would have, too, if I'd been able to stay in the partnership. Aero-tip of the day: Thoroughly inspect the engine compartment for foreign matter before every flight. In most airplanes this means lying on the ground and looking with a flashlight through any openings on the underside of the engine.
-
After an investigation into a few isolated field reports, it was discovered that in some instances conventional 50/50 water - glycol coolant mixture could begin to boil off before the maximum cylinder head temperature was reached. To address this issue and maintain the highest level of flight safety, Rotax issued the initial version of Service Bulletin SB-912-043 / SB-914-029 in September 2004. This bulletin changed the coolant specification for the 912 & 914 engines from a 50 / 50 water - glycol mixture to a 'waterless' coolant with a much higher boiling point. This change was made to insure that coolant boil off could not occur in any circumstances provided that the engine CHT limits were respected. Subsequent to the initial release of Service Bulletin SB-912-043 / SB-914-029, Rotax has continued to examine this issue, and now recognizes that for some 912 & 914 engine installations conventional 50/50 water - glycol mixture coolant may be a viable alternative. Conventional 50/50 water - glycol coolant solution is inexpensive, readily available and has excellent heat transfer properties. Understanding the benefits provided by conventional water - glycol coolant in some applications, Rotax has now released a new revision of Service Bulletin SB-912-043 / SB-914-029. With the release Service Bulletin SB-912-043 R2 / SB-914-029 R2, use of conventional 50/50 water - glycol coolant is once again allowed, provided certain conditions can be met. In order for a 912 or 914 series engine to be safely operated with conventional water - glycol coolant, SB-912-043 R2 / SB-914-029 R2 mandates that both cylinder head temperatures AND coolant exit temperature must be monitored at all times. Coolant exit temperature must never exceed the boiling point of 50/50 water - glycol coolant mixture AND engine cylinder head temperatures must never exceed the maximum permissible values set out in the appropriate engine Operators Manual. To meet these requirements a coolant temperature sensor and cockpit mounted coolant temperature gauge must be installed in addition to CHT instrumentation. The coolant temperature sensor must be installed in the coolant line between the outlet of the expansion tank and the inlet of the coolant radiator (please refer to the Cooling System section of the appropriate engine installation manual for more details). Installation of the coolant temperature sensor must not impede or restrict the coolant flow. The installed coolant temperature gauge must be appropriately marked with the maximum allowable coolant exit temperature. Installation of the coolant temperature sensor and gauge will allow the pilot to monitor the coolant temperature throughout the entire engine operational range. If for any reason the coolant temperature approaches or exceeds the maximum permissible value (approx. 120 C (248 F) in a cooling system pressurized to 18 psi (1.2 bar)) the pilot will be able to take the appropriate action (reduce power setting and / or terminate flight). Once again, installation of a coolant temperature gauge DOES NOT alter the requirements for the monitoring of engine cylinder head temperatures and respecting published CHT limits. In some aircraft installations, the liquid cooling system may not be able to maintain a coolant exit temperature below the boiling point of conventional 50/50 water - glycol coolant. This may be due to the size of the coolant radiator, the design of the engine cowling, operating profile, or other related factors. In applications where the coolant exit temperature may exceed the boiling point of conventional water - glycol coolant, SB-912-043 R2 / SB-914-029 R2 requires the use of 'waterless' coolant only. When 'waterless' coolant is used, monitoring of the coolant exit temperature is not required. The boiling point of the 'waterless' coolant is higher than the maximum allowable cylinder head temperature, therefore the coolant cannot be boiled off without exceeding the engine CHT limits. Use of 'waterless' coolant DOES NOT alter the requirements for the monitoring of engine cylinder head temperatures and respecting published CHT limits. In cases where 'waterless' coolant is used and engine cylinder head temperatures exceed the maximum permissible values, the coolant system must be repaired or modified in such a manner as to increase the cooling capacity of the system. More information regarding coolants for 912 & 914 series engines, including recommended brand names, can be found in Rotax Service Information SI-912-016 / SI-914-019 (August 2006). All owners & operators of 912 & 914 series engines should obtain a copy of this Service Information document. If there is any question regarding the selection of the correct coolant for a particular engine installation, the engine owner / operator is strongly encouraged to contact the nearest authorized Rotax Service Center or their aircraft manufacturer.
-
Fuel Vents... UNOBSTRUCTED. It's a common step on an airplane's Preflight Inspection checklist. But what are you really looking for? Why is it so important to check fuel vents for obstruction? Tank types There are three main types of fuel tank commonly installed in general aviation airplanes (note: some airplane models may have more than one type of tank installed): Bladder-type tanks-flexible rubber tanks, like big, thick "balloons" in the wings or fuselage. Metal or fiberglass tanks-sealed containers for fuel set into the wings or fuselage. "Wet wings" -- portions of the wing structure themselves that are sealed to contain fuel and prevent leakage. Fuel vents Just like a portable gas tank for a lawn mower or boat, your airplane's fuel tank requires a "push" of air pressure to keep fuel flowing toward the engine. A blocked fuel vent can cause a vapor lock that cuts off fuel flow -- causing a fuel starvation engine failure even when there's a lot of fuel remaining in the tank. Fuel vents come in many designs and location, but usually consist of a stick, or probe, extending below the wing or fuselage. Orientation of the vent is critical -- if it is not properly slanted into the slipstream it may actually create suction from the tank, instead of pressure into it. Each individual fuel tank may have its own vent, or several tanks may plumb into a single vent line. Secondary vents may be recessed in the wing, or consist of a simple hole drilled in the aft side of the primary vent. Secondary vents are your back-up in case bugs, dirt or ice block the primary. Fuel tanks have another reason for proper venting. If a vent becomes obstructed the suction created by a fuel pump (or even a carbureted engine) can be so great that the tank collapses. Bladder tanks may bunch up so fuel can't get from parts of the tank into the engine; hard tanks can dimple and bend; and wet wings may collapse to the point the airfoil shape is disrupted and aerodynamics severely compromised. A metal "tip tank" that collapsed in flight under the suction of fuel draw, after its vent line was obstructed by an insect. (photo courtesy American Bonanza Society) Few Pilots Operating Handbooks tell precisely where fuel tank vents are located, how they need to be oriented, whether they have secondary holes that must also be open, or even how many fuel vents there are on the airplane. Your best bet is to contact a user group <STRONG title=http://www.airaffair.com/Library/_clubs.>("type club")[/b] for your particular airplane type for the proper tank vent inspection requirements. Aero-tip of the day: Check fuel vents for orientation and lack of obstruction during every preflight check.
-
I seem to be the one to post most of the accident reports If they are related to RAA aircraft then i post in the incidents Accidents forum. Most however are related to GA aircraft so they get posted in the GA forum. turtle