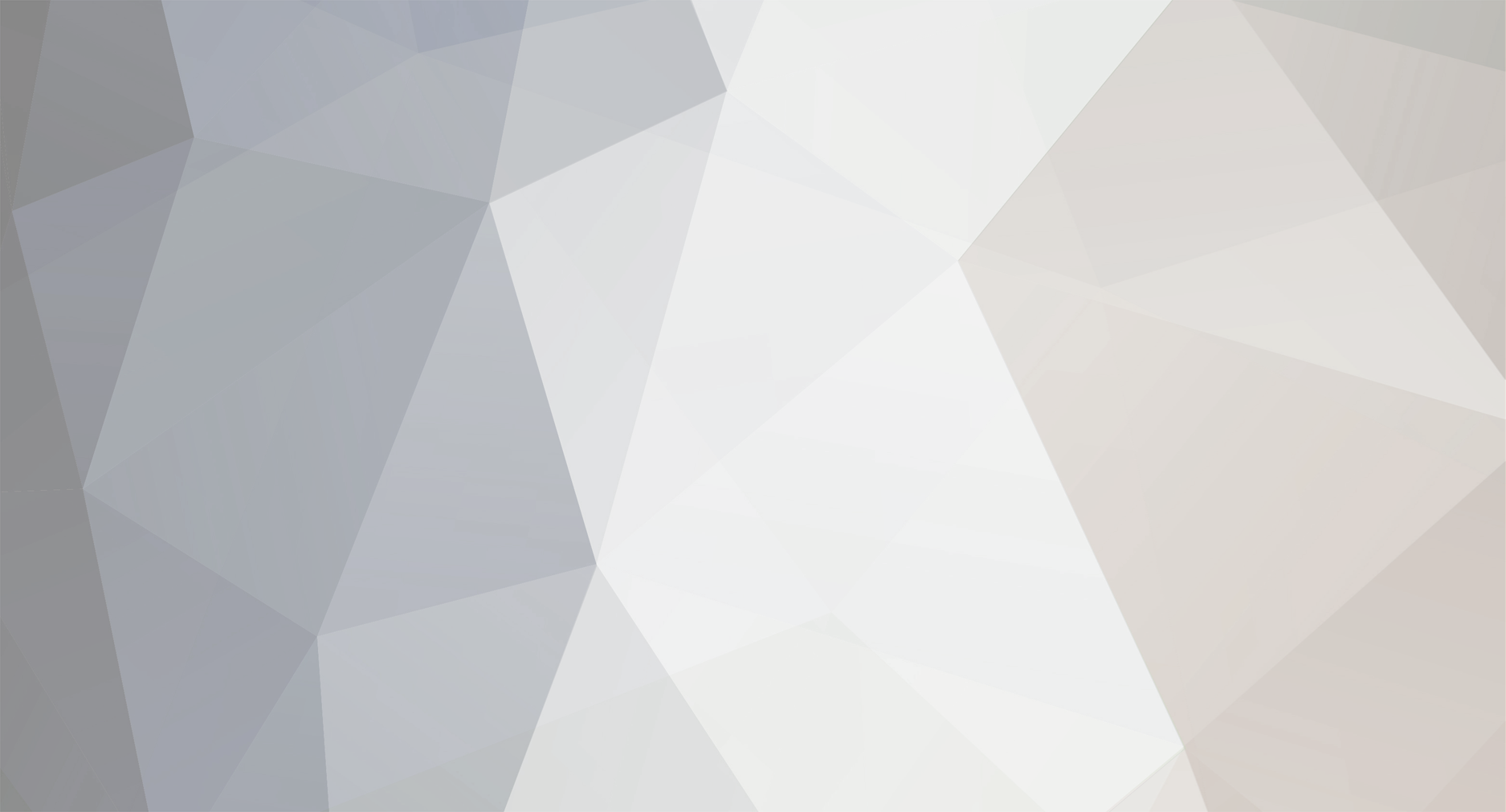
Wilfred
Members-
Posts
332 -
Joined
-
Last visited
-
Days Won
1
Content Type
Profiles
Forums
Gallery
Downloads
Blogs
Events
Store
Aircraft
Resources
Tutorials
Articles
Classifieds
Movies
Books
Community Map
Quizzes
Videos Directory
Everything posted by Wilfred
-
Aircraft Tire Selection and Maintenance By Kim Santerre Maintenance An aircraft tire is a sophisticated, computer-designed, multi-component product consisting of three major materials: steel, rubber and fabric. Taking this down a level, there are multiple types of nylon and rubber compounds in tire construction, each with its own special properties designed to complete the task assigned. The only thing they have in common with auto tires is that they are round. Tires are available in tubeless and radial construction for the heavy iron, but by and large light twins and single-engine, piston-prop aircraft have a choice limited to tube-type, bias-ply tire brands and subsets within brands. Your choice is nominally an economical model, a mid-price version, a high-end model or a retread. Retreads are particularly popular with flying schools. Aircraft tires are approved under the FAA's Technical Standard Order system (TSO). All TSO-C62b-qualified tires with a speed rating of 160 mph or less -- as well as TSO-C62c-qualified tires -- do not require re-qualification to TSO-C62d unless the tire is changed. Tire Selection [ATTACH]1278[/ATTACH] Tires are marked with lots of information you need when you're ready to replace them. (Click here for larger version.) When selecting a tire, check your POH for the requirements for your aircraft. It will include both a size, such as 6.00-6, and a ply rating, and sometimes a brand and model recommendation. The ply rating determines the load-carrying capability of the tire. Stick to the POH on both size and ply, because you can end up with unexpected results if you elect to experiment with unapproved tires or ply ratings. If there is an STC for specialty tires, such as flotation types as may be used on a bush plane, that's fine. You, of course, will pay an airspeed penalty in that case. Note that the term "ply" is used to identify the maximum-rated, static-load capability and corresponding inflation pressure applicable to specific operational requirements. The ply rating is an indication of tire strength and does not specify the actual number of carcass plies within that tire. Only a small number of piston GA type aircraft come with tubeless tires and include the Beech Duke, Queen Air, Twin Beech and Cessna 404 Titan. Note that the same tire may have different inflation pressures (especially nose wheels) due to airplane loading differences. Be sure to check your aircraft's maintenance manual for the correct pressure for your airplane. There is also a good chance that the nose-wheel tire is a different size and different inflation value than the mains. Tire Mounting The valve stem should be aligned with the red dot or triangle on the tire, which indicates the circumferential location of the light spot on the tire. Goodyear tubes are marked with a yellow stripe to indicate the heavy spot; if there is no yellow spot, then the valve is considered the heavy spot. Tire Inflation Due to the properties of the materials from which they are constructed, aircraft tires will expand for up to 12 hours after initial inflation. As the volume of the tire increase, the effective pressure will decrease. Therefore the inflation pressure of newly mounted tires should be checked after a minimum of 12 hours and re-inflated to the required pressure. Consequently, tires should not be placed in service until they have been inflated a minimum of 12 hours, pressure rechecked, and tires re-inflated if necessary. Within the next 24 hours, if the pressure decreases more than five percent, it could be caused by trapped air between the tire and tube, valve-core leakage, or a damaged tube. It's really important to maintain proper inflation, as this affects the tire life (from wear and heat) as well as performance, from hydroplaning to wheel shimmy. (Of course improper maintenance and wear can also cause similar performance problems.) Tire Maintenance [ATTACH]1279[/ATTACH] This tire suffered from both overinflation and an alignment problem. Aircraft with tire wear problems, not attributable to tire balance, need to have the alignment checked. Check your maintenance manual for applicability and specific procedures. Some aircraft have very limited adjustments. Inflation should also reflect the aircraft load and temperature profile on heavier aircraft. Check pressure and tire condition daily with multiple flights or before flight with cool tires. A temperature change of 5°F produces approximately one-percent pressure change. It can take up to three hours after a flight for tire temperatures to return to ambient. This means that tire pressures change on a daily basis. These are all reasons why it is important to check pressure daily or before each flight. Excess inflation pressure should never be bled off from hot tires. All adjustments to inflation pressure should be performed on tires cooled to ambient temperature. When tires are going to be subjected to ground temperature changes in excess of 50°F because of flight to a different climate, inflation pressures should be adjusted to worst case prior to takeoff. The minimum required inflation must be maintained for the cooler climate; pressure can be readjusted in the warmer climate. Before returning to the cooler climate, adjust inflation pressure for the lower temperature. Aircraft Spruce & Specialty has an excellent pressure gauge that reads in one-pound increments, as well as a separate tool that has a specialized adapter for fitting through wheel pants. And while you're at it, always use the MS valve caps with the o-ring core to keep the valve stem clean and the loss of any air through the valve core -- Spruce has them, too. Given a choice, use nitrogen gas in lieu of shop air. Shop air may have excessive moisture, which makes it even less desirable than ambient air for use in tires. Nitrogen will not sustain combustion and will reduce degradation of the tube or liner material, casing plies and wheel due to oxidation. If you find any signs of damaged wheels, be sure to replace them as they are under terrific stress. Aircraft Spruce has an excellent selection. Making Tires Last Besides maintaining proper inflation, tires should be kept clean and free of contaminants such as oil, hydraulic fluids, grease, tar, and degreasing agents, which deteriorate rubber. Contaminants should be wiped off with denatured alcohol and then the tire should be washed immediately with soap and water. When aircraft are washed, ideally, tires should be covered with a waterproof barrier. Goodyear adds antioxidants and antiozonants to the sidewall and tread to help prevent premature aging from ozone in the air and weather exposure. The use of aftermarket tire dressings (especially any automotive type) and wipe-on or spray-on protectants is generally not recommended since they may actually accelerate the loss of factory protectants. Aircraft tires, like other rubber products, are affected to some degree by sunlight and extremes of weather. While weather checking does not impair performance (as long as no carcass is showing), it can be reduced by protective covers when the plane is tied-down outside, especially in hot, dry, sunny climates. If you have spare tires on hand in your hangar, be sure to store them away from fluorescent lights, electric motors, battery chargers, electric welding equipment and electric generators, since these products create ozone, which is harmful to rubber. According to Goodyear, there is no specific shelf life for aircraft tires; it depends on storage conditions. Retractables [ATTACH]1280[/ATTACH] You can see that the room for error in some retractables is very tight. While sizes are reasonably consistent between brands, a retract check is a good idea. Also, a new tire will grow several percent over the first 12 hours of inflation, so it should be rechecked and inflated as required. Retractable aircraft represent a special case for conservatism. If you are switching tire brands or even tire types from what is currently installed, a gear retraction test is a good idea to be sure that the tire will not interfere in any way with the gear wells or the retraction mechanism. Some aircraft have quite limited space around the tires and the retraction mechanisms. And remember the tire will grow a bit in service, so if it's a close call when brand-new, chances are you may have a problem later on. I also recommend against retreads on a retractable. While it's true airlines use retreads, it's a different ballgame there. The airline tires are serial-number tracked, so the carcass history is known from manufacture to retirement. When to Change the Tube When changing tires, it may be hard to dump a tube that appears serviceable, , but it's best to use a new tube with a new tire, because the old tube may have grown as much as 25 percent in service. Thus, reusing the tube may be difficult or you may end up with a fold or binding spot in the tire that will fail prematurely. There is no reason why a tube cannot be patched with an in-service tire, providing the tire passes a safety inspection, e.g., no sidewall punctures allowed. When to Replace a Tire [ATTACH]1281[/ATTACH] This tire had to be re-tired after just one landing when the student landed with the brakes on. Tires should be examined and possibly replaced when they have certain types of cuts, sidewall damage, bulges, fabric fraying, groove cracking or flat spots. The specific criteria for each type of damage is listed below. Tread Cuts: Inspect tread for cuts and other foreign object damage and mark with crayon or chalk. Follow specific cut-removal criteria from aircraft maintenance manuals, operation manuals or tire-cut limits on the tire sidewall when available. When specific cut-removal criteria are not available, use the following Goodyear removal criteria: any cut into the casing plies on bias tires, any cut into the belt package on radial tires, any cut which extends across one or more rubber tread ribs to the fabric, or rib undercutting at the base of any cut. Warning: Do not probe cracks, cuts or embedded foreign objects while tire is inflated. Sidewall Damage: Remove tire from service if weatherchecking, cracking, cuts or snags extend down to the casing ply in the sidewall and bead areas. Cuts and cracks deeper than one ply require the tire to be scrapped. Bulges: Bulges in any part of tire tread, sidewall or bead area indicate a separation or damaged tire. Mark with crayon and remove from service immediately. Fabric Fraying/Groove Cracking: Tires should be removed from service if groove cracking exposes fabric or if cracking undercuts tread ribs. Flat Spots: Generally speaking, tires need not be removed because of flat spots due to touchdown and braking or hydroplaning skids unless fabric is exposed. If objectionable unbalance results, however, rebalance the assembly or remove the tire from service. To help with removing old tires, Aircraft Spruce & Specialty sells a bead breaker that is much easier than stomping on the old tires. Aircraft Spruce also has a wealth of jacks and jacking aids to help cradle the main gear legs in many Cessnas and provide a non-slip, safe jacking point. Problems with New Tires While quality control of tires continues to be high, it is not infallible. New tires should be balanced and the proper weights applied. Ninety-nine percent of the time that is all there is to it. However, on occasion, a tire may be out-of-round as a problem with the construction process and slip through the QC screen. It doesn't take a lot to cause a balance problem. It will not generally be obvious to the naked eye without some form of a reference to continuous diameter checks. So if the tire seems to not want to be balanced, don't dismiss the possibility that the "new" tire needs to have some rubber shaved off to make it round. Retreads [ATTACH]1282[/ATTACH] Here is an example of a pure alignment problem with the aircraft. Such wear issues are sometimes difficult to avoid, so one strategy is to reverse the tires before wear on one side becomes too significant. This will effectively double the life of the tire, notwithstanding other disqualifying issues. Let's look at retread tires. Are they right for you? Generally they are less expensive than new tires of similar quality construction. Goodyear for one has an extensive rejuvenation and testing procedure. As said earlier, some flight schools use them where they get a lot of use over a short time in trainer-type aircraft. That said, the price differential over new is not so significant that I would use them on my plane. Unlike the airlines, you do not know the history of the retread you buy. Top Tire Recommendations For a retractable, I recommend a top-level tire such as a Goodyear FC II or III, or whatever is recommended by the POH. With higher takeoff and landing speeds as well as more likelihood of foul weather use, the best tires are the only choice in my opinion. The Goodyear FC III has the greatest cross-section of tread in the 600x6 compared to other popular brands. Compared to the FC II, the FC III also has Kevlar belts, improved tread design for wet performance, deeper tread, additional resistance to sunlight, and an improved tread compound. These factors add up to about 20 percent more potential landings than the FC II. For most use, however, the question is not the number of landings but how long it stands up to time. If you fly infrequently in, say, a Skyhawk, you may want to save some money with a more economical choice. Here offerings from Specialty Tire Co. (formerly McCreary Tire) may meet your budget. In increasing costs are the Air Trac, Air Hawk and Super Hawk. Mechanics I deal with recommend the middle-line tires as the most cost-effective. General Mounting Guidelines [ATTACH]1283[/ATTACH] Be sure to keep the paper sticker on a new tire. It has a set of basic mounting instructions for that tire. Use a clip-on chuck, an extension hose, and a safety cage for inflation. Use a direct reading or dial-type pressure gauge with 5 psi or finer increments that is calibrated on a regular basis. When inflating a tire/wheel assembly, regulate the supply line to a pressure no more than 50 percent higher than the tire service pressure. Do not inflate a tire above rated pressure to seat beads. Make certain that every valve has a cap to retain inflation and prevent dirt, oil and moisture from damaging the core. Tube Type Mounting Use the correct tire and tube for the wheel assembly. Clean inside of tire, then lubricate lightly with tire talc, not baby powder. Aircraft Spruce sells the proper talc.) Inflate tube to slightly round, and insert in tire. Align yellow stripe on tube with red balance dot on tire; align red dot with valve if no stripe on tube. When mounting tire and tube on wheel, be sure that wheel bolts are torqued to wheel-manufacturer's instructions before inflating. Inflate tire in a safety cage to rated pressure. Deflate assembly to equalize stretch. Reinflate to rated pressure. After 12-hour stretch period, re-inflate to rated inflation pressure. Tire Balancing and Landing-Gear Vibration [ATTACH]1284[/ATTACH] When jacking, be sure to do it properly. While a wing jack is not necessarily required, be sure any method that you use is safe and solid in case the wind blows while the wheel is off the plane. Check your pilot manual for proper jacking methods for your particular aircraft. A couple of 4x4s stacked under the bare axle is a good safety practice. It is important that aircraft wheels and tires be as well-balanced as possible. Vibration, shimmy, or out-of-balance is a major complaint. However, in most cases, tire balance is not the cause. Other factors affecting balance and vibration are: Flat-spotted tire due to wear and braking Out-of-balance wheel halves Installation of wheel assembly before full tire growth Improperly torqued axle nut Improperly installed tube Use of non-aircraft tubes Poor gear alignment Bent wheel Worn or loose gear components Incorrect balancing at wheel assembly In addition, pressure differences in dual-mounted tires and incorrectly matched diameters of tires mounted on the same axle may cause vibrations or shimmy. With some split wheels, the light spot of the wheel halves is indicated with an "L" stamped on the flange. In assembling these wheels, position the "L's" 180 degrees apart. If additional static balancing is required after tire mounting, many wheels have provisions for attaching accessory balance weights around the circumference of the flange.
-
The right instructor will make learning to fly a challenge, but still a pleasure. He/she will play a big part in: how quickly you'll reach your goal, and therefore how much it'll cost to complete your training, whether you'll finish at all, and most importantly how safe you'll truly be when you finish. It's fairly rare in most locations to have a choice of CFIs, but if you do have a choice there are ways to pick the best instructor for you. Sad to say, there are some times when it's better to avoid flying with the only choice available at all, and consider traveling somewhere else to take lessons. Further, when you are just learning to fly you have no frame of reference when forming a relationship with someone who has a huge impact on your future, and that of your family. So…how can you choose a primary flight instructor? The myth of hours It's commonly accepted in flying circles that the more flight time a person has, the better pilot he or she is. Sure, we'd like all CFIs to be recently retired airline captains with thousands of hours just gushing to bring more pilots into the fold. The reality is that most primary CFIs are at the beginning of their career, just recently out of training themselves, and often very overworked from an unpredictable flying schedule and the frequent need to work nights in other industries to make ends meet. Instructing can be boring, repetitive work, and the luster of actually being paid (very little) to fly can wear off rapidly. Countering the myth Hours alone does not a good CFI make. Even that airline or military pilot can severely hamper your progress if he/she is not a teacher first and a pilot second. Knowing what to do does not mean you can see it in others, or coach them smoothly to correctness when they don't do things right the first (or the fortieth) time. Some of the very best CFIs are very low-time pilots…if they have a passion for teaching. Interview your instructor Here's a real novel idea: CFIs are working for you. Like you would any other prospective employee, you should interview instructors wanting to get the job. Ask your instructor not only how many hours he/she has in airplanes, but also: How many hours of instruction have you logged? What else have you taught besides flying? Have you been a tutor, a teacher, a corporate trainer? What formal training have you received on instructional techniques? If you got an airline or charter job tomorrow, would you want to keep instructing on the side? Get references from pilots who have completed training with that instructor, and if possible, talk to persons who have flown with him/her but have not achieved their goal. Aero-tip of the day: Go beyond flight hours, and interview for teaching ability and professionalism when picking a flight instructor.
-
The new issue is due soon but this is a link to the current issue for those that missed it’ http://www.casa.gov.au/fsa/2006/aug/index.htm
-
COMPUTER PILOTS CAN FLY LIKE THE PROS AND AVIATORS THE WORLD OVER WITH JEPPESEN SIMCHARTS v4.0 ENGLEWOOD, COLO., November 1, 2006 - Jeppesen has recently launched the latest offering in its successful, long-running SIMCharts product line. Designed exclusively for flight simulation enthusiasts, virtual airline operators, and those pilots who use PC simulators to develop or hone their skills, SIMCharts v4.0 plugs and plays with Microsoft Flight Simulator X and contains a worldwide terminal chart set that matches the Jeppesen NavData contained in Flight Simulator X. SIMCharts takes realism to the next level by allowing users to sort, view and print real Jeppesen arrival, departure, approach and airport charts that thousands of pilots and airlines around the world use every day. New with SIMCharts v4.0 is a completely digital delivery interface that utilizes the Internet and a small client that resides on the customer's computer--no more CDs to keep track of or physical product to ship. Customers may place orders by calling Jeppesen at 1-800-621-5377, or +49 6102 5070 in the Eastern Hemisphere. SIMCharts v4.0 is offered at one convenient price of 59.95 USD per year for a worldwide coverage. This includes unlimited access for one full year to over 25,000 real Jeppesen terminal charts. Just as with previous versions of SIMCharts, customers can print charts to have on hand for quick and easy access. Charts can also be called up during a Flight Simulator X session and displayed in a separate window. An aircraft position spotter provides real time feedback for added situational awareness and also makes for a great instrument flight training or proficiency tool. "Everyone from seasoned instrument pilots, to serious gamers, to student pilots find value in the added realism that SIMCharts brings to Flight Simulator X," said Dan McGaw, Jeppesen business programs manager, Business and General Aviation. "This latest release of SIMCharts offers all the features and benefits our customers have come to expect, but now with the added convenience of a web-based global data set that contains over 25,000 charts. Now our customers can literally fly just about anywhere in the Flight Simulator X virtual world and be covered with charts for a nominal annual fee." SIMCharts v4.0 provides improved search and filtering capability, so customers can quickly find charts in the worldwide database, sort them, and print, if so desired. Enroute charts are rendered within Flight Simulator X, and, therefore, are no longer offered in the SIMCharts lineup. SIMCharts do not contain current data and are not for actual navigation use. For more than 70 years Jeppesen has made it possible for pilots and their passengers to safely and efficiently reach their destinations. Today this pioneering spirit continues as Jeppesen delivers essential information and optimization tools to improve the efficiency of air, sea and rail operations around the globe. Jeppesen is a subsidiary of Boeing Commercial Aviation Services, a unit of Boeing Commercial Airplanes. Visit www.jeppesen.com/simcharts for product information. Jeppesen corporate information is available online at www.jeppesen.com
-
Is The aircraft registered If so the log book is part of the sale and must be transferred to the new owner Otherwise contact RAA. I believe there are still five of these aircraft on the register, and they may be able to help you with info or contact details for other owners.
-
(article) Beware Symmetry I was with a student teaching the preflight inspection on the six-passenger, retractable-gear airplane he'd just purchased. Looking in the left-wing wheel well I pointed out a broken spring on the landing gear uplock mechanism. It was a small, thin, wiry spring, partially obstructed (as is normal) by a fabric cover. I declared the airplane rejected for flight (I don't want to have to write about by own gear-up landing, especially if it results from a previously noted mechanical cause). But with a lot of new ground-time on our hands we continued the "teaching" preflight. Wouldn't you know, the corresponding spring in the right wheel well was broken also. It looked the same on both sides of the airplane... enough to make me wonder if I had misdiagnosed the problem. Symmetry Admit it, you know what I'm talking about. You get a little pain on one side of your body, but if you feel it on the other side too you declare it "normal" and move on. In our airplane example, my student and I saw something we thought was wrong on one side of the airplane, but comparing the "mirror image" on the other side revealed the same picture. It would have been very easy to declare the airplane airworthy because the discrepancy was symmetric. No doubt this is why it wasn't found by the pilots who had flown the plane before us, or the mechanic that had inspected the airplane before my student bought it (although he/she should have known better). There was no "right" configuration to compare it two and, in airplanes, two wrongs do not make it right. Aero-tip of the day: Check the airplane against informed expectations -- not just against the airplane itself.
-
<H1 style="MARGIN-TOP: 0pt" ="bottomrule"></H1> <H1 style="MARGIN-TOP: 0pt" ="bottomrule">Motoring News</H1> <H1 style="MARGIN-TOP: 0pt" ="bottomrule">Subaru diesel is boxing clever </H1> <TABLE style="CLEAR: both; MARGIN-BOTTOM: 10px; WIDTH: 450px; HEIGHT: 25px" cellSpacing=0 cellPadding=0><T> <T> <TR vAlign=center></TR></T></T></TABLE>Monday 10th April 2006 Japanese firm Subaru is set to become the first mainstream maker to have a diesel engine in a flat-four boxer layout, when it introduces a brand new 2.0-litre unit in 2008. The motor, claimed to match BMW's 2.0-litre TD for performance, will be introduced across the range. Sources say the first car to feature it is likely to be the Legacy Rumors have it as a 2.2L engine, and most likely also turbocharged. I would also expect to see Subaru using an ally block and head, like many modern car diesels. My guess is that Subaru also has a larger version for the Euro-Tribeca. if you add a pair of cylinders to the 2.2 H-4, you end up with a 3.3 H-6, which would be perfect for the larger Tribeca. This engine is very important for Subaru, as nearly 40% of new cars sold in Europe are diesel-powered. If Subaru really wants to make a dent in that market, diesels are a must-have option. I would also hope that, once these engines prove themselves in Europe, that we would them offered in North America, as other clean diesels are on the way for here. turtle
-
(article) Engine Fires On Startup Engine Fires On Startup Engine fires during start can happen any time for any number of reasons, but by far they most frequently occur in cold weather from over-priming.What should we do in the event of an engine fire on the ground? Checklist Most aircraft manuals have a checklist that outlines steps to follow in the vent of an engine fire on the ground. Not that you'd have time to pull out the Pilots Operating Handbook (POH) if it happens to you. You need to look in the POH for the airplane you're flying and memorize the procedure for the unlikely event you'll need to use it. There are several variations on the procedure, but all contain these basic steps: Mixture.................IDLE CUTOFF Fuel selector...........OFF CONTINUE CRANKING TO PULL FIRE INTO INDUCTION SYSTEM EVACUATE THE AIRCRAFT Again, review the POH for the airplane you're currently flying for the best technique to use. Engine Types There are two basic types of reciprocating aircraft engines: Carbureted engines. Fuel is combined with air and then pulled into the induction system through the carburetor venture. If a fire starts as a result of overpriming (or in some types, aggressively pumping the throttle during start) but the engine itself starts, suction may draw the fire inside the engine. Hence the advice to keep cranking the starter, although I know of no POH that provides any guidance on how long to keep cranking. Fuel-injected engines. Fuel is delivered directly to each cylinder, combining with air in the induction manifold just before the intake valve. Overpriming a fuel-injected engine may cause fuel to collect in the intake manifold, and cranking after a fire starts may pull the flames into the cylinders. But often overpriming a fuel-injected engine puts a lot of fuel in the exhaust manifold, and starter operation will do nothing to draw in the fire. So although continuing cranking may help in some cases, it's not as likely to put out the external fire as it might be with a carburetor. Get out, check it out It's fairly rare, but sometimes an engine fire after start eventually consumes and destroys the entire airplane. Crank a few seconds to try to draw in the fire, but then evacuate the aircraft and get well away. If a large-capacity fire extinguisher is available you might be able to put the fire out, but a small in-cabin type may not be adequate. Get your passengers and yourself out of danger. If the fire does go out, whether through cranking or on its own after you evacuate, get a mechanic to remove the cowling and take a very good look at the aircraft for possible damage. If everything checks out okay, consider a local test flight before venturing out of the traffic pattern. Avoidance Carefully prime the engine before a cold-weather start. Preheat the engine if the temperature is below about 40 degrees F to make for an easier start. Better yet, hangar the airplane the night before if at all possible. Even an unheated hangar often keeps the engine warm enough to avoid the need for aggressive priming. Aero-tip of the day: Know how to avoid engine fires during start, and what to do if one happens to you.
-
October 29, 2006 Motor Head #16: Jabiru -- A New Engine That's Not All That New, But Cool Nevertheless article By Marc Cook, Columnist About the Author ... Marc Cook is, besides being a big engine nut, the editor-in-chief of Kitplanes magazine and a freelance journalist living in Long Beach, Calif. He worked on staff at AOPA Pilot magazine from 1988 to 1999, and is a regular contributor to AOPA's Flight Training magazine. He was responsible for overseeing the restoration of three sweepstakes aircraft for the association. ("Nothing like back-to-back restoration projects to gray the hair," he says.) Until recently, he owned a Beech P-35 Bonanza, but currently flies a nearly original '69 Bellanca Turbo Viking -- orange shag carpet and all -- owned by Troy Foster. Read the rest of Marc's Motor Head columns here. Motor Head Unless you've been around homebuilts, you've probably never heard of a Jabiru. (Sure, you may be familiar with the varieties of stork whose name comes from the Tupi-Guarani term meaning "swollen neck.") I mean the Jabiru airplane -- a tidy design that's morphed into several varieties: two- and four-seat, 51% experimental and, soon, a ready-to-fly light sport aircraft -- but, actually more to the point, the Jabiru engine. Even if you're a certified-only kinda pilot, you should know more about Jabiru because one of its engines may well be under the cowling of that hot little light-sport aircraft you just bought. In yet another example of invention shooting out of Mother Necessity, Jabiru started as an airplane company and quickly found that the engine choices in the circa-60-hp class were limited to practically one. And then that manufacturer stopped making the engine. So Jabiru designer Rodney Stiff began work on replacement. If you think about it, there are scores of engine configurations out there -- and that's just for pistons, more even if you're of the mind to harness the exquisiteness of Felix Wankel's (rotary) design -- and the man who pens his own airplane has the luxury of making the space outboard of the firewall anything he chooses. So he can build an engine of pretty much any configuration: inline, V, opposed, W, X ... so many possibilities. Not So Different? ... And yet the clean-sheet Jabiru arrived into this world in 1992 as an air-cooled, opposed-piston, flat engine with a single, central crankshaft bolted directly to the propeller, a single central camshaft that operates two valves per cylinder through pushrods and rocker arms, and many other similarities to our supposedly outdated certified engines. In fact, you could see the Jabiru as the new product of an existing engine company leveraging its knowledge of traditional designs, only making the engine smaller and lighter. Comes to that, the Jabiru's diminutive valve covers in some ways remind me of Continental's technically superior yet ill-fated Tiara series'. Well, how about that? Jabiru's first effort was a 1.6-liter (call it 98 cubic inches) but after the first 40 were delivered, the company turned its quest for more power into a new iteration, now displacing 2.2 liters (134 cubic inches) from a 97.5-mm bore and a comparatively short 74-mm stroke, and producing 80 horsepower. This became the Jabiru 2200. Take it one step further -- as Continental and Lycoming (and Franklin and Pratt & Whitney and Wright) did -- and bolt six cylinders to the case and you have the 3300, capable of 120 hp maximum and 107 continuous. That 3.3-liter displacement is 201 cubic inches, making this a great comparison with the Continental O-200. (More on that further down.) You may also have seen Jabiru's 5100, an eight-cylinder derivative making 180 hp. The company has put that engine on the back burner as it concentrates on the smaller mills. ... Actually, Quite Different Jabiru 5100 Engine (Click here for larger version -- 232 KB.) Take the top off any Jabiru-powered airplane and prepare to be dazzled. The Jabiru glistens in beautifully CNC-machined 5000-series aluminum. The jauntily cut cylinder heads -- separate pieces from the steel-lined barrels, presumably easing valve work in the field -- expose a pair of automotive-style spark plugs, side by side. The induction and exhaust systems are neatly tucked underneath. To ease cooling concerns, each Jabiru comes with a semi-plenum cooling shroud so that the internal layout of the cowling isn't quite so critical. (Being air cooled, though, a clean inlet flow and appropriately valued exit area remain important.) Once your gaze has wandered from the machined cylinders, they alight upon the fully CNC-machined cases. The support structure is internal, so no bumps and lumps, nor do you see the typically grotty casting quality evident on your typical Lyconental. (Yes, I realize that the surface finish of a casting has virtually no impact on its strength, but if I'm paying the equivalent of a decent sports car on an engine alone, I'd at least like it to be attractive.) If finish alone sold engines, the Jabiru would be flying off the shelves. Look further. Notice how the cylinders are staggered side to side? Seems a lot more than usual, something you're at first willing to chalk up to an optical illusion. But the exaggerated offset is real, the result of a five-main-bearing design for the four-cylinder and a seven-main design for the six. Each crank throw is supported on both sides by a main bearing; a traditional aero engine has only a "flying web" between opposed cylinder pairs. So a four-cylinder Lycoming, for example, has but three main bearings, albeit very large ones, particularly the massive bearing between the prop flange and the first set of cylinders. Jabiru's literature calls out eight bearings on the six-cylinder engine, apparently counting the split shells on the crank nose as two. These bearing shells are, like several parts of the engine, automotive in origin. Jabiru uses a removable prop flange so that replacement of the crank nose seal -- a fairly ugly job on a traditional flat engine -- is quite easy. Nice touch. This feature, along with the solid crankshaft, means a fixed-pitch prop or an electrically adjustable one at best. High-Speed Crankshaft, Low-Speed Pistons Back to the crank design. In theory, more main bearings the better, but there is a slight weight penalty and a supposed internal drag penalty as well. However, this design makes sense in light of the Jabiru's high operating speeds. For the 3300, maximum power comes at a lofty 3300 rpm, while maximum-continuous is 2750 rpm. Thanks to the 74-mm stroke (2.91 inches), the piston speeds remain moderate. A Continental O-200 has a 3.88-inch stroke, for comparison. Maximum piston speed for the 3300 is 1602 feet per minute, compared to 1778 fpm for the Continental; at the Jabiru's max-continuous speed (2750 rpm), it's a modest 1335 fpm. Your IO-520 is whipping along at 1800 fpm at takeoff and 1533 fpm at a leisurely 2300 rpm cruise setting. But let's have true perspective: A Yamaha YZF-R6 sportbike, with a teeny-tiny 42.5-mm stroke (1.67 inches), wailing at its (theoretical) 17,500-rpm redline, posts a breathtaking 4880-fpm max. piston speed. You don't want to be anywhere near that sucker when it blows. That's a long way around to suggesting that the Jabiru's operating speeds are, in many ways, conservative. The valvetrain is similarly conservative, with a single, underslung camshaft, two valves in each cylinder and simple screw-and-locknut adjustments in the heads. Jabiru recommends checking the valve lash several times early in the engine's life, but the job appears to be a simple one. Many of the valvetrain components come from Honda, while the pistons are modified Australian-market GM pieces (the modification is to add a piston pin circlip to keep the pin from riding out and scoring the bore.) Those pistons provide a modest 8.0:1 compression ratio, which would be suitable for auto fuel if only Jabiru were confident of the go-juice's quality; because it isn't, the only recommended fuel is 100LL. Rotax Comparison Photo by Kevin Wing Jabiru 3300 Engine in the Jabiru Airframe. (Click here for larger version -- 118 KB.) In many respects, the Jabiru follows the conventions set by the Rotax 912, arguably the most popular "nonstandard" aviation engine in the last decade and a half. (Rotax says there are more than 15,000 of them in service.) A simple, crank-mounted, electrical system powers the airplane and the ignition from a permanent-magnet alternator, much like modern motorcycles do. The timing is fixed at 25 degrees. Where the Rotax uses independent coils, the Jabiru has two modified Honda coils feeding a pair of small distributors for the dual-ignition system. Similarly, while the Rotax employs motorcycle-style Bing carburetors, the Jabiru has one feeding an under-engine plenum that shares space, Lycoming-like, with the oil pan. (Still, carburetor heat is a recommended airframe addition.) Thanks to its greater displacement -- the Jabiru six's 3.3 liters dwarfs the 912's 1201 cc (74 cubic inches) -- the Aussie engine pounds out more power than even the turbocharged Rotax 914, and does so at much lower engine speed. (Remember that the Rotax has a reduction gearbox.) Bigger and simpler, too: No liquid cooling setup to deal with, one fewer carb (and no need to synchronize), and a pilot-friendly wet-sump oiling system that obviates the need for an external tank and the traditional "burping" required of the 912 to read the oil level properly. That and the Jabiru uses traditional aviation oil, so there'll be no need to stomp out to the Mobil station down the road from the airport when you need a quart. In many respects, the 3300 is the perfect "tweener" engine, bigger than the stoutest Rotax (for now) and still smaller, lighter, and cheaper than the lowest Lycoming or Continental. With the low-end LSAs becoming modern darlings, Jabiru could be well placed. Take It For A Spin As everyone knows, there are specifications and company propaganda, and then there's flying. I had the good fortune to spend a day with a Jabiru 3300 in a Jabiru airframe recently. And while my Rotax 912 time -- probably 200 hours or more, but well spread out among a variety of airframes -- isn't terribly recent, I think I can still offer a few useful observations. Like most good engines, the Jabiru comes to life without fuss, thanks to a decent ignition system and well-considered jetting in the single Bing. Spinning a lightweight Sensenich composite prop -- carbon fiber over wood, ground adjustable -- the engine feels responsive, and moves the J230 Experimental with ease. Runup is conventional but short: Check the ignition and glance at the gauges. There's no prop control, no mixture. (As on the Rotax 912, the Bing carburetor self-adjusts. It's a simple and largely effective system. Inside the carburetor throat is a piston [called a slide] that descends to block air flow. Its movement is controlled by a large diaphragm above that responds to air density [volume] through the carb. At high volume, like takeoff, the slide rises, allowing more air to flow. That's great, but the trick is the needle attached to the slide. This tapered needle descends into the main jet cavity. The higher the slide, the further the needle comes out of the main jet tube and the more fuel flows. At altitude and/or reduced throttle, the slide descends and the needle blocks more of the main jet tube, reducing fuel flow. My experience with the 912 is that the system works as advertised but EGTs inevitably drop at altitude, hurting fuel efficiency. In fact, Jabiru lists the 75% cruise consumption of the 3300 as 6.87 gph, which calculates out to a specific fuel consumption of 0.51 pounds per hour per horsepower. A carbureted Lycoming can do better, manually leaned, at around 0.45-0.47 pph/hp; an injected six-cylinder Continental, with balanced injectors, can do an impressive 0.385.) Yes, But How Does It Sound? Jabiru 2200 Engine in Twister Homebuilt. (Click here for larger version -- 180 KB.) Stand outside and witness a takeoff, and you hear a short burst of prop-tip noise and a very quiet engine note somewhere between an IO-360 Continental and a Porsche. Not exactly grumbly but not bumblebee, either. From inside, the 3300 moves the Jabiru smartly down the runway and results in very good climb considering the power loading. In this airplane, the temps seemed very well controlled, with CHTs staying below the magic 380 degrees -- though I don't know if that number is magic for the Jabiru or not. Cruising is as simple as setting the rpm for the desired power and watching the temps. While I don't doubt that a controllable carb (or fuel injection) would improve the 3300's fuel specifics, somehow the drop from 7 gph to, say, 6 seems hardly worth the effort. During the approach and landing, the engine is extremely well behaved, and the ability to basically ignore it and fly the airplane is wonderful. I did manage to botch the first landing -- trying out my Beech A-36 flare on a knee-height airplane -- and noticed the only quirk of the day. The engine is very responsive, which is no surprise with a lot of cubes and a single, smallish carburetor, and asking for just a bit of power can result in actually getting a lot. Whoa, boy. The final comparison comes with the Continental O-200. The Continental is two inches longer than the six-cylinder Jabiru, nearly five inches taller, and almost nine inches wider. Continental lists the O-200's dry weight as 170 pounds, which probably doesn't include the charging or ignition systems. The Jabiru, including an exhaust system, all electrics, and the carburetor, is said to weigh 178. (A basic 912 is some 50 pounds lighter.) In all, the more I look at the Jabiru, the more impressed I become. Now to scam another ride in that Jabiru airplane, under the guise of continued research of course ...
-
I would think all the info would be in your maintenance log book.
-
How To Build A Fixed-Wing Aircraft
Wilfred posted a topic in Aircraft Building and Design Discussion
This is a quite interesting video worth the time to watch broadband only http://vnvlain.blogspot.com/2006/10/how-to-build-fixed-wing-aircraft.html -
A blonde went to a flight school insisting she wanted to learn to fly that day. As all the planes were currently in use, the owner agreed to instruct her on how to pilot the helicopter solo by radio. He took her out, showed her how to start it and gave her the basics, and sent her on her way. After she climbed 1000 feet, she radioed in. "I'm doing great! I love it! The view is so beautiful, and I'm starting to get the hang of this." After 2000 feet, she radioed again, saying how easy it was becoming to fly. The instructor watched her climb over 3000 feet, and was beginning to worry that she hadn't radioed in. A few minutes later, he watched in horror as she crashed about half a mile away. He ran over and pulled her from the wreckage. When he asked what happened, she said: "I don't know! Everything was going fine, but as I got higher, I was starting to get cold. I can't remember anything after I turned off the big fan."
-
Generally if it has a headset then it will be posible to buy or make an adapter. Ask the shop where you purchased it what is available. or the headset supplier will sometimes carry adapters or know where to obtain them.
-
<TABLE height=125 cellSpacing=0 cellPadding=0 width=125> <T> <TR> <TD vAlign=center align=middle width=125> </TD></TR></T></TABLE><a href="http://www.daydeal.com/product.php?productid=13306&cat=1787&page=1" target="_blank">3.5mm Stereo Audio Adapter for Motorola RAZR V3 V3i SLVR L7 L6 PEBL U6 KRZR K1</A> http://cgi.ebay.com.au/3-5mm-Motorola-Headphone-Adapter-MP3-Adaptor-V3-V3i-AU_W0QQitemZ230042396651QQihZ013QQcategoryZ42404QQrdZ1QQcmdZViewItem http://stores.ebay.com.au/i-fever-Express
-
List of reference books on Aviation Matters
Wilfred replied to facthunter's topic in Aircraft Building and Design Discussion
<TABLE =lowerblocksbasic width="100%"> <T> <TR> <TD =smallblocktitle>Emergency Maneuver Training by Rich Stowell </TD></TR> <TR> <TD> "Rich Stowell, who has been in the forefront of Emergency Maneuver Training for years, has just written a book that provides similar advice for general aviation pilots. Emergency Maneuver Training is destined to contribute significantly to general aviation safety, and I recommend it to all who want to keep their airplanes out of the scrap yard." --Barry Schiff, author, video host, airline pilot. BOOK AVAILABLE NOW FROM AOPA - signed by the author . $59 inc Post & Handling All proceeds from sales of this book go to the Ron Bertram Memorial Fund, which has been established to honour the memory of Ron Bertram by promoting aviation awareness through sponsorship of TIF's, GPFT's, and Emergency Manouevre Training. Donations can be made to the AOPA office.</TD></TR></T></TABLE> -
"If you have wings you are most welcome" The SAAA is holding it’s National Convention at Wagga Wagga airfield during Friday 27th, Saturday 28th and Sunday the 29th October 2006. This year the Association is again opening its door to all aviation enthusiasts. 2006 is also the 40th anniversary of the Corby Starlet. It is hoped many Corby Starlets will be in attendance. The Association will provide workshops and forums for every one as we continue to celebrate our years of supporting experimental aircraft building and flying. This event attracts hundreds of aviation enthusiasts annually, and we have provided the following to entertain and educate : Latest trade and aviation products display. Check out the news and trade terms. Workshop forums for all aircraft owners and builders. Discussion by CASA and Airservices Australia on their latest procedures and products. Demonstrations of particular interest to aviators covering the latest in GPS, ADS-B and other equipment. A Dinner with a fascinating speaker on the Saturday evening. On-field camping facilities. Off-field activities</A> for partners and families refer to Wagga Tourism website www.tourismwaggawagga.com.au. Motels and Hotels book at [email protected] or 1800-100-122. Enquire about how you can save even more off your fuel bill with our special BP Fuel card deal contact - [email protected]. Enquire about our special SAAA QBE Insurance deal - [email protected]. Flying In - check here for reporting details. Get the latest news update here. Get the aircaft judging form and award details here
-
http://www.auf.asn.au/cagit_trophy/cagi.html
-
List of reference books on Aviation Matters
Wilfred replied to facthunter's topic in Aircraft Building and Design Discussion
How about '' Anyones guide to becoming a pilot" http://anyonespilotguide.com/ turtle -
I have a lightspeed 30G headset which has a built in phone adapter which works greatand as far as coverage goes i have a telsta service on digital and very rarely find an area out of service while in the air. we tried a next G phone last week but the coverage at present is not that good . As you say they assure us it will be better than the existing CDMA network by mid next year. Having said that the allthough coverage is great in the air i often find on landing that their is no coverage in that area while on the ground. By the way that is in the Jab . I would think a metal aircraft could have some reception problems. Also with the microair transponder, it often reads incorrect altitudes when the mobile is turned on, so be careful if in controlled airspace. Also that ericsen phone in your photo is probably about 10 years old. They were never a model renownded for ther reception qualities. turtle
-
(article) Improper Use Of Flight Controls
Wilfred posted a topic in Student Pilot & Further Learning
Last on the FAA's list of the Top 10 contributors to pilot-error mishaps is "improper operation of flight controls." It's fairly rare when stick-and-rudder ability alone result in an accident; in most cases pilot distraction plays a part even in these basic-skills events. Flying to distraction From the NTSB: The pilot had just departed when the cowling came open and he elected to return to the airport. During the landing roll he lost control of the airplane, ground looped and departed the runway to the left, resulting in substantial damage to the right wing. A post-accident examination of the airframe and airplane's systems revealed no anomalies. Probable cause: the pilot's failure to maintain directional control of the airplane resulting in a ground loop. Contributing factors include the inadequate preflight inspection, the pilot's failure to properly latch the cowling, and the pilot's diverted attention to the open cowling "Braking" ground From the NTSB: During a soft field landing the airplane contacted a bump in the terrain and the airplane bounced into the air. The pilot applied aft elevator control and used rudder to maintain directional control. He inadvertently applied the brakes while attempting to maintain rudder control. When the airplane came to a stop, the tail lifted and the airplane nosed over. Probable cause: the pilot's inadvertent excessive use of the toe brakes during the landing roll Don't "over" do it From the NTSB: While practicing soft-field takeoffs a student pilot flying with a CFI over-rotated causing premature flight. The CFI attempted to correct the situation but the aircraft settled into an uncontrolled descent beyond the airport boundary where it struck terrain.</BLOCKQUOTE> Aero-tip of the day: Practice basic flying skills so that your stick-and-rudder responses are almost instinctive. Pay special attention to the adage "fly the airplane" when presented with distractions. -
(article) Off-Airport Landings 2 Reviewing the FAA's Top 10 list of pilot error mishaps, yesterday we discussed off-airport landings-precautionary (such as when weather is moving in) and intentional (a preplanned landing on an unimproved surface). Today we'll look at another aspect of "selection of unsuitable terrain" as a mishap cause: what to do if the engine quits and you can't make it to a runway. Spiral down I consistently had trouble getting to a good landing spot in my early simulations of the engine-failure off-airport landing. I'd pick a field and aim for it, only to glide out of range during a circuit down to final approach. That's when someone mentioned that I should not fly to a field, I should pick a field very nearby and spiral down over it. This keeps you constantly within range of the field, so if you misjudge your glide you can always turn directly toward it and land. Notes: This requires that you pick a field that is wide as well as long. Best survivability comes when touchdown ground speed is as slow as possible. This requires landing into the wind; a misjudged glide and turn toward the field may result in landing at a higher groundspeed, increasing the risk of injury. The Commercial Pilot Practical Test Standards include evaluation of this maneuver, the Steep Spiral (Area of Operation V Task B). Getting real Picking the field requires evaluation of a number of variables. There's an excellent <STRONG title=http://www.auf.asn.au/emergencies/forced_landing.>on-line narrative by John Brandon[/b] that warrants reading. Scroll down especially to section 3.3 and his description of criteria for choosing an emergency off-airport landing site. Aero-tip of the day: Be on the lookout for potential emergency landing zones continually while in visual flight.
-
Although they aren't ranked in order of frequency, the ninth item on the FAA's Top 10 list of contributors to pilot-error accidents is "selection of unsuitable terrain". This cause category can apply to planned landings on unimproved surfaces, precautionary landings for weather or other reasons, and unplanned landings that result from engine or other in-flight failures. The Aeronautical Information Manual (AIM) tells us: In the event of an off-airport landing, pilots have used a number of different visual cues to gain reference. Use whatever you must to create the contrast you need. Natural references seem to work best (trees, rocks, snow ribs, etc.) Over flight. Pass over the intended landing spot at a safe but slow airspeed, at a safe but low altitude-this gives you the best view of surface conditions. Use of markers. Any sort of items on the ground or dropped to the ground that delineate the landing zone. Weighted flags. Again, to outline the area of intended use. Smoke bombs. Any colored rags. Dye markers. Kool-aid. Oh, yeah. Trees or tree branches. Dropping items from the aircraft to use as reference points should be used as a visual aid only and not as a primary landing reference. Unless your marker is biodegradable, be sure to retrieve it after landing. Never put yourself in a position where no visual references exist. Abort landing if blowing snow obscures your reference. Make your decisions early. Don't assume you can pick up a lost reference point when you get closer. Exercise extreme caution when flying from sunlight into shade. Physical awareness may tell you that you are flying straight but you may actually be in a spiral dive with centrifugal force pressing against you. Having no visual references enhances this illusion. Just because you have a good visual reference does not mean that it's safe to continue. There may be snow-covered terrain not visible in the direction that you are traveling. Getting caught in a no visual reference situation can be fatal. Watch! The wind When picking a landing area don't forget to gauge the direction and strength of surface winds. Look for: Motion of trees, branches or large shrubs. Blowing dust or debris on or near the surface. Waves on nearby ponds or lakes. Animals, especially livestock. Cattle tend to turn so their faces are away from the wind; if wind speeds are great (and it's cold outside) cows usually lie down. Aero-tip of the day: Look closely at surface conditions and wind characteristics before choosing an off-airport landing surface.
-
We've been reviewing the FAA's Top 10 list of pilot-error accident causes. Next up: "misjudgment of distance and speed". What the Feds are really getting at here are two types of accident: Runway undershoot, resulting in landing short of the runway and/or stalling on approach. Landing long, and going off the far end of the runway. Coming up short Landing short of the runway is usually the result of flying at too low an airspeed on final approach. As angle of attack increases it takes more and more power to maintain a given glide path. If the pilot does not add power or adjust pitch (to reduce angle of attack) the "sink rate", or rate of descent, may become excessive, and the angle of descent take the airplane to a point short of the prepared surface. If the pilot is lucky the plane will roll onto the runway without damage. If not... Of course if angle of attack gets completely out of hand the airplane may stall, potentially impacting the ground at a higher rate of descent and out of control, with even more dire consequences. It's counterintuitive to push the nose down if the ground is coming up too fast. It's also considered bad form to have to add power on final approach, despite the real need when the glidepath is too steep. Making sense of the relationship between power and pitch, and angle and rate of descent, is one of the main reasons we have to practice landings so much before the first solo flight, and why pattern practice is a staple of flight reviews throughout a pilot's entire flying lifetime. Landing long Although (as the adage goes) it's better to go off the far end of the runway at, say, 20 knots than to hit the approach end at a much higher speed, running off the end of the runway is another common cause of mishaps. This usually results from too fast a speed on final approach. As a rough rule, for ever extra five knots of airspeed on short final a typical light piston airplane will increase its landing distance by about 10%. Come in 10 knots fast and you'll use up about 20% more runway, all else being equal. If you misjudge your angle of descent and land farther down the runway than expected you're also more likely to run off the far end. Combine "hot" (too much airspeed) and "high" (too shallow a descent) and you may find yourself on the evening news as they hoist your airplane out of somebody's parking lot. What's the answer to both scenarios? Good airspeed control. This comes from using a target power setting and pitch attitude. You may have to adjust these for any given landing, but you can't tell what adjustments to make unless you have a "standard" approach (and its resulting performance) in mind to start. Aero-tip of the day: Practice precise airspeed control on final approach to make more accurate landings
-
RAA site with al the latest AD's A link to our own RAA site with al the latest AD's http://www.auf.asn.au/airworthiness/index.html
-
We've been reviewing the FAA's Top 10 list of pilot-error accident causes. Today's item is also the cause of the majority of all aircraft engine failures-fuel mismanagement. Fuel management mishaps come in two varieties: Fuel starvation: fuel is available somewhere on the airplane, but the flow is interrupted and the engine quits from lack of fuel. Fuel exhaustion: the engine simply runs until there is no fuel left on board. Auxiliaries on landing (From the NTSB): The airplane [was] on a downwind leg to land…. When it was abeam the north end of the runway, it began to descend below 500 feet agl…then made a descending right turn…. Subsequently…the right wing impact[ed] the ground…. The fuel selector was found in the "auxiliary" fuel tanks position…. No defects or anomalies were found with the engine that could have precluded normal engine operation. The fuel pump was removed and did not contain any fuel. The fuel screen was free of debris. A review of the before landing checklist in the airplane flight manual revealed that prior to landing, the fuel selector must be positioned to the "MAIN TANK MORE NEARLY FULL." She "hoped she'd make it" (From the NTSB) The pilot and passenger flew…to the destination airport approximately one hour away. Prior to departing from the destination airport, the pilot performed several touch-and-go landings at night for currency…and then the pilot and passenger departed for the return flight. After flying for about an hour, the pilot declared an emergency, and was radar vectored to the closest airport. She advised air traffic control that the airplane was "out of fuel," and that she "hope[d] to make it to the runway." The airplane impacted a utility pole and a building approximately 1/4 mile from the end of the runway. Examination of the airplane and engine revealed no mechanical anomalies. Four gallons of fuel were drained from the right fuel tank, and the left tank was empty. The pilot refueled the airplane on the day prior to the accident, at an airport 50 miles from her home airport. According to the…Owner's Manual, the average fuel burn rate was between 8 gallons per hour (gph) and 10 gph. Probable cause: The pilot's inadequate preflight planning, which resulted in fuel exhaustion and subsequent loss of engine power. Fuel management is a four-step process: Preflight planning to assure you have adequate fuel plus a comfortable (not just legal) reserve. Preflight verification that you actually have the fuel load you think you have. In-flight monitoring to ensure you're getting the fuel flow you expect, and that your ground speed matches or exceeds your expectations-in other words, repeatedly confirming what you planned for will actually come true. Fuel tank selection, as appropriate to the aircraft, to get maximum fuel out of each tank without causing a power interruption, and leaving yourself plenty of fuel in a tank approved for use (and selected) during approach and landing. Deviate as soon as you detect you will not arrive at destination without a comfortable fuel reserve. Aero-tip of the day: Don't skimp on fuel planning and in-flight management, and avoid this very common cause of lightplane mishaps.